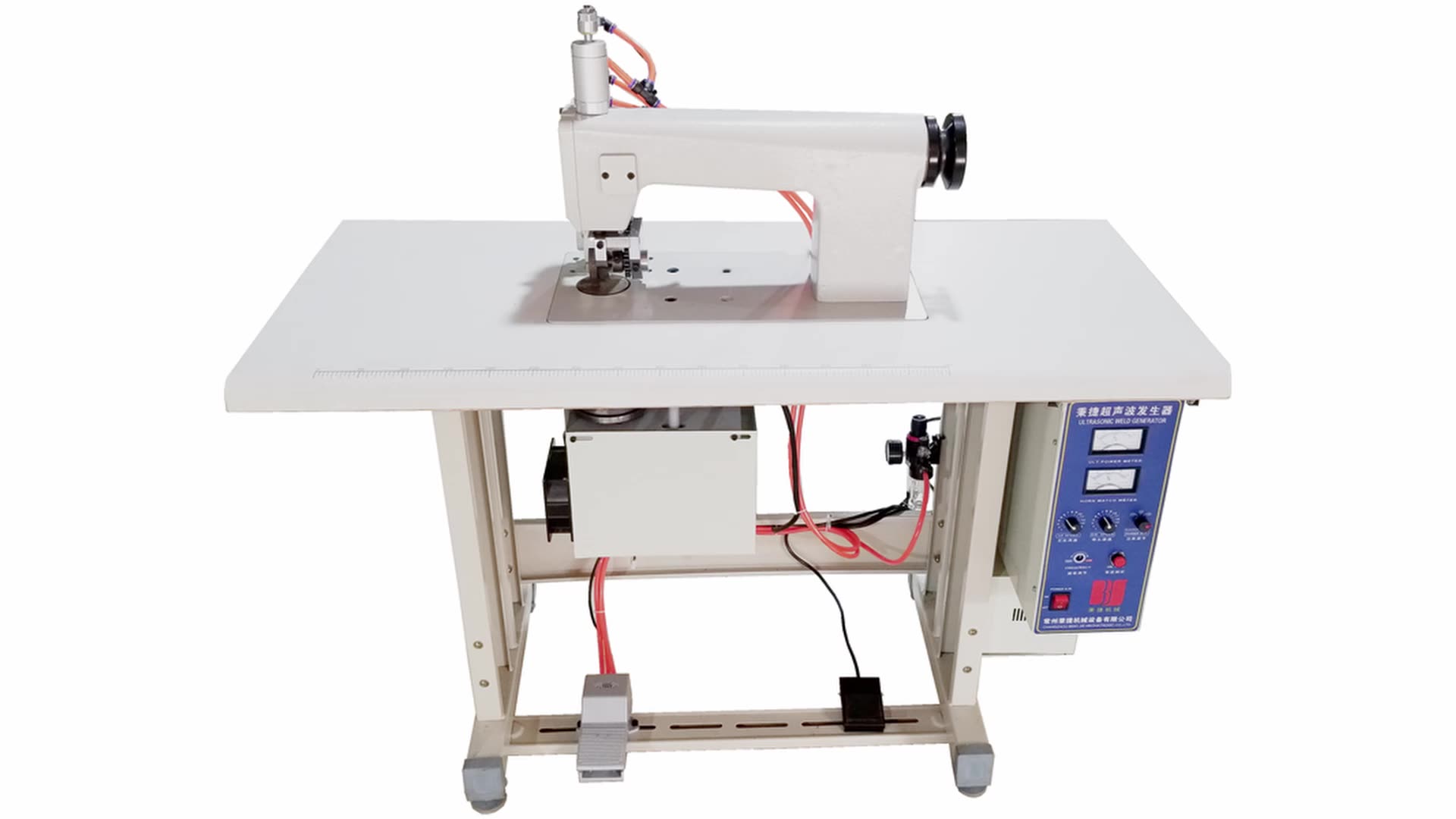
The demand for ultrasonic stitching machines has grown rapidly due to their efficiency, versatility, and ability to produce high-quality seams without traditional threads or adhesives. Among the top suppliers, Chinese manufacturers stand out, offering innovative solutions that cater to diverse industries. This guide is designed to help beginners understand how to operate a China ultrasonic stitching machine effectively while gaining insight into the technology and its benefits.
Understanding Ultrasonic Stitching Machines
Ultrasonic stitching machines use high-frequency sound waves to bond materials together. This innovative technology eliminates the need for traditional sewing components, making it ideal for industries such as textiles, medical, automotive, and packaging. A China ultrasonic stitching machine is particularly popular for its affordability, advanced features, and reliability.
Key Components of an Ultrasonic Stitching Machine
-
Ultrasonic Generator: Converts electrical energy into high-frequency sound waves.
-
Transducer: Amplifies sound waves and transfers them to the horn.
-
Horn/Anvil: Applies the ultrasonic energy to the material, bonding it together.
-
Control Panel: Allows users to adjust settings such as speed, pressure, and amplitude.
-
Material Feed System: Guides materials through the machine for continuous stitching.
Understanding these components is crucial for smooth operation and optimal performance.
Step-by-Step Guide to Operating a China Ultrasonic Stitching Machine
Step 1: Preparation and Setup
-
Read the Manual: Familiarize yourself with the machineβs manual provided by the ultrasonic sewing machine manufacturer. It contains detailed instructions and safety guidelines.
-
Inspect the Machine: Check for any visible damages or loose parts.
-
Choose the Right Materials: Ensure the machine is compatible with the materials you intend to stitch, such as nonwoven fabrics, synthetic textiles, or plastic sheets.
-
Set Up the Machine: Place the machine on a stable surface and connect it to a reliable power source.
Step 2: Configuring the Machine
-
Adjust Settings: Use the control panel to set parameters like amplitude, frequency, and pressure according to the material being used.
-
Install the Horn: Secure the horn and ensure it aligns correctly with the anvil.
-
Load Materials: Position the materials in the feed system for smooth operation.
-
Test Run: Conduct a trial run with scrap material to ensure proper bonding and alignment.
Step 3: Operating the Machine
-
Start the Machine: Turn on the power and initiate the ultrasonic generator.
-
Guide Materials: Feed the materials gently into the machine, ensuring steady and even pressure.
-
Monitor Performance: Observe the stitching process for consistency and quality.
-
Adjust as Needed: Modify settings if issues like uneven seams or weak bonding occur.
Step 4: Post-Operation Maintenance
-
Turn Off the Machine: Disconnect the power supply to avoid accidents.
-
Clean the Components: Wipe down the horn and anvil to remove residue.
-
Inspect for Wear and Tear: Check for any signs of damage or wear on the parts.
-
Store Properly: Cover the machine to protect it from dust and environmental factors.
Benefits of Operating a China Ultrasonic Stitching Machine
1. High Efficiency and Speed
Ultrasonic stitching is faster than traditional methods, reducing production time and increasing output. Chinese machines are designed for bulk production, making them ideal for high-demand industries.
2. Superior Seam Quality
The technology ensures strong, clean, and precise seams. This is particularly important in industries like medical manufacturing, where product integrity is critical.
3. Cost-Effective Operation
With no need for threads or adhesives, operating costs are significantly reduced. Additionally, China ultrasonic stitching machines are competitively priced, offering excellent value for money.
4. Environmentally Friendly
The process generates minimal waste and doesnβt involve harmful chemicals, aligning with sustainable manufacturing practices.
5. Versatility Across Industries
From nonwoven textiles to plastic components, these machines handle a wide range of materials, making them suitable for various applications.
Troubleshooting Common Issues
Even the most advanced machines can encounter problems. Here are solutions to common issues:
-
Uneven Seams: Check the horn alignment and adjust the pressure settings.
-
Weak Bonding: Increase the amplitude or frequency for stronger seams.
-
Machine Overheating: Ensure adequate ventilation and avoid prolonged use without breaks.
-
Noise During Operation: Tighten loose components and inspect the transducer for damage.
Consulting the ultrasonic sewing machine manufacturer for technical support can also resolve persistent issues.
Tips for Optimizing Performance
-
Regular Maintenance: Clean and inspect the machine frequently to prevent downtime.
-
Use Compatible Materials: Stick to materials recommended by the manufacturer for best results.
-
Employee Training: Ensure operators are well-trained to handle the machine safely and efficiently.
-
Upgrade Software: If applicable, keep the machineβs software updated to access new features and improvements.
Why Choose a China Ultrasonic Stitching Machine?
1. Trusted Manufacturers
Chinese manufacturers have a proven track record of delivering high-quality machines that meet international standards. Their dedication to innovation and customer satisfaction ensures reliable products.
2. Competitive Pricing
By leveraging economies of scale and advanced production techniques, Chinese suppliers offer machines at prices that suit bulk buyers and small businesses alike.
3. Customization Options
Many ultrasonic sewing machine manufacturers in China offer customization services, tailoring machines to specific industry needs.
4. Robust After-Sales Support
Manufacturers provide comprehensive after-sales support, including training, spare parts, and technical assistance, ensuring smooth operations.
Conclusion
Operating a China ultrasonic stitching machine is a straightforward process once you understand its components and functionality. With proper preparation, configuration, and maintenance, these machines can significantly enhance production efficiency and product quality. Chinese manufacturersβ commitment to innovation, affordability, and reliability makes their ultrasonic stitching machines a valuable investment for businesses across industries.
Whether youβre new to ultrasonic stitching technology or looking to optimize your current operations, following this guide will help you achieve seamless results and maximize the potential of your machine.
Leave a Reply