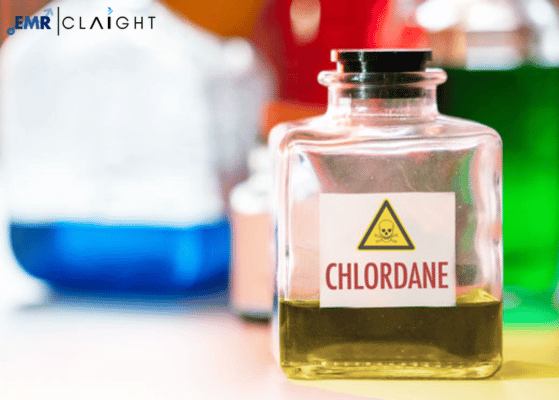
Chlordane is a synthetic organic compound primarily known for its historical use as a pesticide. Despite being banned or restricted in many countries due to environmental and health concerns, it remains an area of interest for certain niche applications and research purposes. Manufacturing chlordane requires careful adherence to safety protocols and regulatory guidelines due to its toxic nature. Establishing a Chlordane Manufacturing Plant Project demands advanced production technologies, strict quality control measures, and comprehensive compliance with environmental and occupational safety standards.
Applications and Market Demand
Historically, chlordane was extensively used as a pesticide to control termites, ants, and agricultural pests. Although its use in agriculture and pest control has been largely phased out in many regions, limited production continues under strict regulatory oversight for specific purposes such as:
- Research Applications: Chlordane is occasionally used in research to study its environmental impact, chemical properties, and potential remediation strategies.
- Specialised Industrial Uses: Some industries may use derivatives of chlordane or related compounds in tightly controlled conditions for niche applications.
The demand for chlordane is highly restricted and regulated, primarily focusing on non-agricultural applications. Any manufacturing initiative must cater to highly specific and legally sanctioned markets.
Get a Free Sample Report with Table of Contents@ https://www.expertmarketresearch.com/prefeasibility-reports/chlordane-manufacturing-plant-project-report/requestsample
Key Steps in Setting Up a Chlordane Manufacturing Plant
- Market Research and Feasibility Study Conducting thorough market research is essential to understand the demand for chlordane in the specific sectors where its use is permitted. A feasibility study evaluates the projectβs viability by analysing production costs, market trends, and potential challenges. This ensures that the manufacturing plant aligns with legal and industry requirements.
- Business Plan Development A detailed business plan outlines the projectβs objectives, production capacity, financial estimates, and marketing strategies. It serves as a roadmap for the plantβs establishment, ensuring efficient resource allocation and operational success. The plan also identifies potential risks and outlines mitigation strategies, particularly those related to regulatory compliance.
- Location Selection and Infrastructure Selecting an appropriate location is critical for operational efficiency and safety. Factors such as proximity to raw material suppliers, access to transportation networks, and availability of utilities like electricity and water should be considered. The infrastructure must include secure production units, storage facilities, quality control labs, and waste management systems. Compliance with zoning laws and environmental regulations is essential.
- Procurement of Equipment and Machinery Manufacturing chlordane requires specialised equipment, including reactors, distillation units, and filtration systems. Safety features such as containment systems and ventilation units are crucial to minimise risks associated with handling toxic chemicals. Collaborating with reliable equipment suppliers for installation and maintenance support is vital for long-term success.
- Raw Material Sourcing The production of chlordane involves sourcing chemical precursors and reagents. Establishing a reliable and legally compliant supply chain ensures a steady flow of raw materials while adhering to safety and quality standards. The sourcing process must also align with the regulations governing the use of hazardous substances.
Manufacturing Process Overview
The production of chlordane involves several critical stages designed to ensure precision, safety, and compliance:
- Raw Material Preparation: The raw materials are inspected and prepared to meet quality and safety standards.
- Chemical Synthesis: The synthesis of chlordane is carried out under controlled conditions to minimise environmental and occupational risks.
- Purification: The compound is purified to achieve the desired concentration and quality standards.
- Waste Management: Hazardous by-products are treated and disposed of according to environmental regulations.
- Packaging and Labelling: The final product is securely packaged and labelled with detailed safety information for distribution.
Quality Control Measures
Maintaining high-quality standards is essential in chlordane manufacturing. Quality control measures include:
- Raw Material Testing: Ensuring that all inputs meet the required specifications.
- Process Monitoring: Conducting regular checks during production to maintain consistency and safety.
- Final Product Testing: Verifying the purity, stability, and compliance of the finished product with regulatory standards.
Adherence to international safety certifications and regulatory guidelines enhances product reliability and ensures compliance with legal frameworks.
Packaging and Distribution
Effective packaging is vital to ensure the safe handling and transportation of chlordane. Packaging materials must meet stringent safety standards to prevent leaks, contamination, or exposure. Proper labelling with hazard warnings, usage instructions, and regulatory details is essential. Distribution should be limited to authorised users and markets under strict regulatory oversight.
Sustainability and Environmental Considerations
Given the environmental and health concerns associated with chlordane, sustainability and safety are paramount in its production. Implementing eco-friendly practices, such as optimising energy consumption and minimising waste, helps reduce the environmental impact of manufacturing. Advanced waste treatment systems and compliance with international environmental regulations further enhance the plantβs sustainability credentials.
Emerging Trends and Opportunities
While the demand for chlordane is limited, emerging research and advancements in chemical science may open new avenues for its derivatives or alternative applications. Opportunities lie in:
- Environmental Research: Developing safer and more effective methods for the remediation of chlordane-contaminated sites.
- Specialised Industrial Applications: Exploring niche uses for chlordane or its chemical analogues in controlled environments.
Staying updated on scientific developments and investing in research and development ensures that the manufacturing plant remains relevant and compliant with evolving industry needs.
Challenges in the Industry
Establishing a chlordane manufacturing plant involves significant challenges, including:
- Regulatory Compliance: Adhering to stringent national and international regulations governing the production, handling, and distribution of hazardous chemicals.
- Environmental and Health Concerns: Managing the risks associated with chlordane production and ensuring safe disposal of by-products.
- Market Limitations: Navigating the restricted demand for chlordane and focusing on legally sanctioned applications.
Addressing these challenges requires meticulous planning, robust safety protocols, and continuous innovation to ensure operational excellence and compliance.
Leave a Reply