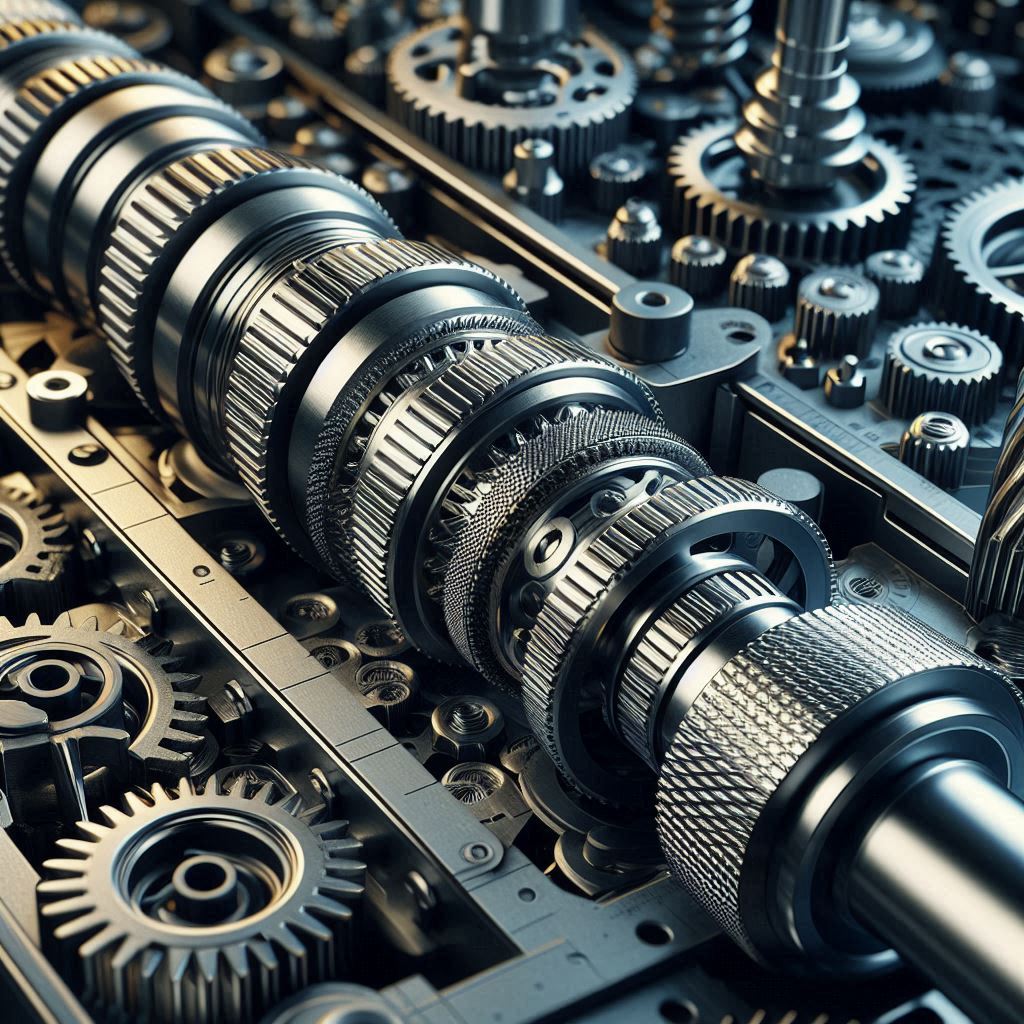
Balancing shafts are critical components in engine and industrial machines that ensure sufficient counter actions between forces that cause vibration, so that the machines work at their best performance levels. This calls for very stringent requirements in the strength, wear resistance, and thermal stability of materials for effectiveness and durability when making these shafts. Let’s dwell on the materials being those that take Center stage in the making enduring balancing shafts.
1. Alloy Steel: Strength and Toughness
Alloy steel mainly plays important role in ensuring balance shaft manufacture because of its high-performance strength and toughness along with its good machining performance in these applications. This surface withstanding wear and fatigue is created by an addition of chromium, nickel, and molybdenum in order to keep the stability and performance of the shaft under constant stress caused by operation of an engine. Further improvement in mechanical properties may be carried out thermally through quenching and tempering processes.
2. Carbon Steel: Worth Durability in Dollars
Cost is the most important factor in the use of carbon steel as one of the common materials for balancing shaft production. It provides high tensile strength and good machinability suitable for components with no need for high corrosion resistance. Different hardness and strength levels are acquired for different operating conditions, depending on carbon content.
3. Stainless Steel: Resistance to Corrosion
If such applications in the environment exist, say marine or chemical processing industry where the material of preference is stainless steel, then steel grade 304 or 316, would expect material deriving from excellent quality combining strength and robust durability with good resistance to corrosion and rusting. Indeed, stainless shafts are especially apt to operate in conditions where moisture and chemicals or other extreme temperature need to be an issue.
4. Cast Iron: Damping Tolerance is Admired
Cast iron has very good characteristics in dampening; hence, it is suitable in shaft balancing in particular applications. Cast iron has high compressive strength, high resistivity against wear and thus is insensitive to wear out. Since it is much weaker in tension than steel, cast iron has an application in specific situations where its cost effectiveness is more and capable of dampening vibrations.
5. Titanium Alloys: Light yet high strength
The demand for high performance balancing shafts has tremendously increased in modern applications, especially in aerospace and motorsport applications. Such material avails both the necessary strength required with minimum-profile mass and therefore whole component. Additionally, the corrosion and not being affected by very extreme temperatures are some of the excellent properties of the material making titanium one of the best to apply in critical conditions. The high cost, however, limits the applicability of the material compared to others.
6. Composites: Modern Material for Advanced Use
Forging is usually made with composite materials such as carbon fibbers and polymers. These materials are for making lightweight applications for industrial use. Costlier and complicated to manufacture, these composites are claimed to be of the future when it comes to elements that are lightweight and strong.
Material Considerations for Choosing
Selection of material for balancing shaft is related to major factors determining their performance in terms of working and durability. Exposures with respect to operations would include temperature, pressure, and corrosion of the components; hence, the selection would be primarily based on these, which in turn determines a reliable choice. Required characteristics of a particular application for strength and efficient weight-savings combined with vibration-attenuation properties would lead to suitable material choice that would meet functional requirements as per application. Cost must also be ensured with a balance between highest efficiency and budget limitations. Thus, based on these considerations, manufacturers could select materials that just satisfy the requirement for any application.
Conclusion
As much as the durability and, thus, the performance of the balancing shaft heavily depends on the materials used for fabrication, with alloy and carbon steel, advanced capabilities will end with titanium and composites, as each has added benefits. In the end, with higher performance and efficiency from the industries, materials might be the highly regarded in the near future, when talking about innovation in manufacturing balancing shafts. The proper materials allow manufacturers to produce balancing shafts that keep pace with the stringent demands of machines today and provide long-lasting reliability.
Leave a Reply