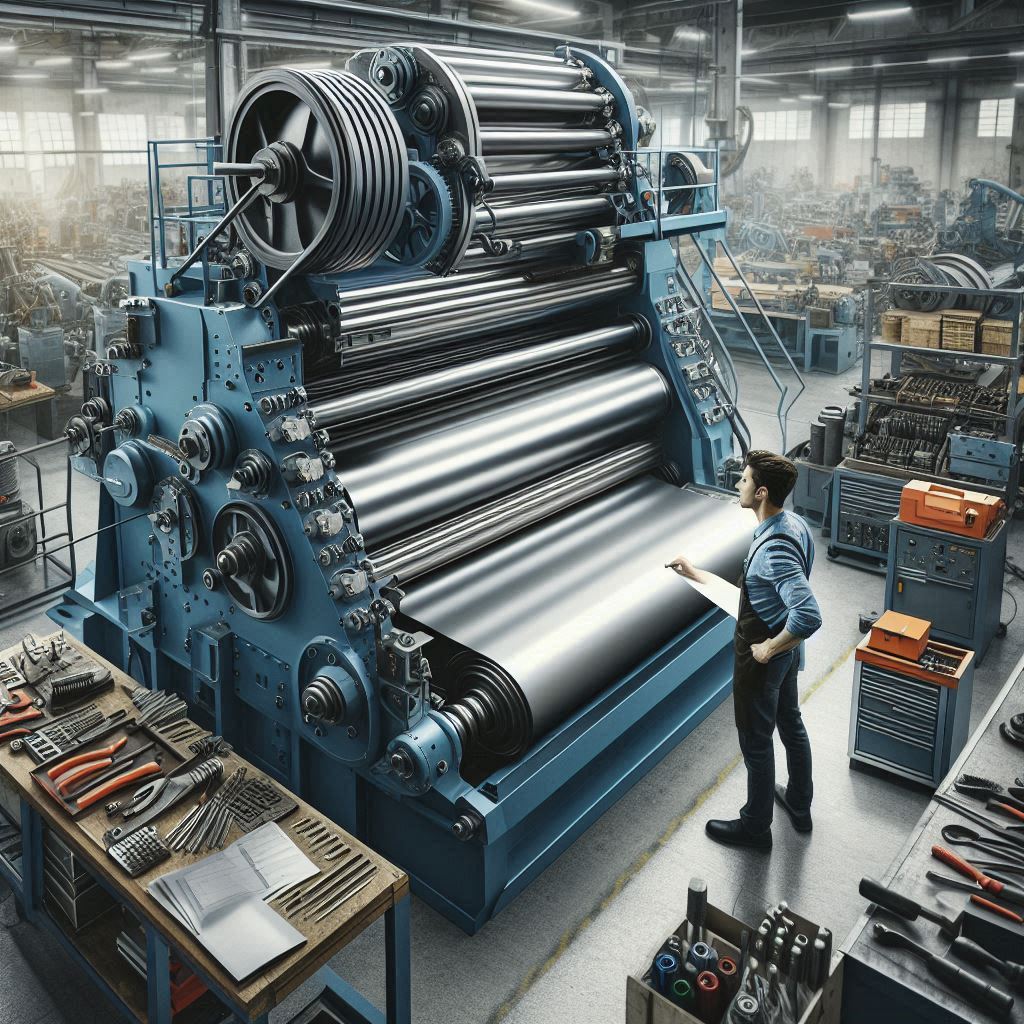
These sheet metal rolling machines have become the necessities in industries engaged in metal fabrication for rolling metal sheets into cylindrical or curved shapes. However, it is quite a detailed task to choose the right machine from evaluation on various significant factors to ensure accuracy in efficiency and durability. Be it a small shop conveyor or a big production source, when appropriate machinery and its application can make a lot of difference in production quality and cost-effectiveness. These are the features one should consider while buying a sheet metal rolling machine.
1. Roller Configuration and Design
Stringing the roller configuration is essential since the machine performance determines whether the sheet metal processing performs well or otherwise in its bending capacity and precision. Most standard bending shapes apply to three-roll machines, making them very common in general fabrication that depends on simple and reliable features. Further precision and automation could be gained from four-roll machines by ensuring better grips and positioning of materials, which would result in better accuracy and efficiency. Pyramid-type rollers are very good for heavy-duty industrial applications, where defined strength and extra control allow the bending of thick and rigid metal sheets with higher capabilities. Selecting the right roller configuration ensures performance maximized by the complexity and size of metal rolling.
2. Material Thickness and Capacity
It is essential to know the maximum sheet thickness and width that the machine can handle. The different metals with which this machine can work might include stainless steel, aluminum, and mild steel. Selecting the rolling machine based on your production requirements will guarantee its optimum working condition and longevity.
3. Manual, Hydraulic, or CNC Control
Sheet metal rolling machine India have their varying kinds specifically designed to meet different purposes of production. Manual machines are best suited for small work and low-volume metal processing applications- offering a cost-efficient and straightforward metal rolling solutions. Because they operate on higher force and efficiency compared to these, hydraulic machines can perform medium to heavy-duty applications where bending capacity is greater. CNC-controlled machines are for high-precision and industrial automation requirements, as they allow programmable operations, repeatability, and improved productivity during large-scale manufacturing processes. Selection of rolling machine, therefore, depends on volume of production, material thickness and level of automation needed for efficient metal processing.
4. Pre-Bending Capability
Pre-bending minimizes flat ends and ensures a smooth curve, allowing the bending of material before it is fully engaged into the rolling zone. Machines with good pre-bending capabilities lay the foundation for an exceedingly good finish that does not require additional post-processing.
5. Speed and Efficiency
Production speed is a huge factor in ensuring that schedules are kept and operational costs are kept low. Machines with variable speed control are adjustable according to the type and thickness of the material, thereby promoting speed at a comfortable level of accuracy.
6. Durability and Build Quality
A strong frame with high-quality rollers provides for long life and reduced maintenance. Hardened steel rollers provide resistance to wear and tear, especially when working with heavy-gauge metals.
7. Safety Features
Safety is an indispensable concern for all industrial machines installed, used, and maintained to ensure the safety of operators and avoid accidents when these machines are operated in the production processes. All modern sheet metal rolling machines have important safety features to minimize risks and improve security at the workplace. Emergency-stop buttons provide an immediate mechanism to shut down the machine in case of an unintentional malfunction to prevent severe damage or injury from occurring. Overload protection puts the machine in safety mode to prevent an aspect of excessive force from being applied to it, thus prolonging its life and maintaining efficient operations. The safety guards are the other protecting barriers through which direct access to moving parts is limited to avoiding injury by accidents. The implementation of these safety measures, however, ensures that the company fulfills safety standards for industries and promotes a healthier and safer working environment altogether.
8. Operational Ease and Maintenance
User-friendly controls and maintenance ease allow for smooth operations. Machines with touch-screen controls and digital displays automatically control functions and minimize the need for extensive training while maximizing productivity.
9. Versatility and Customizability
Industries may require different bending capabilities; therefore, the ability to choose machines with adjustable roller positions and interchangeable dies, as well as multi-radius bending, gives them versatility. Customizable machines are flexible for diverse applications.
10. After-Sales Support and Warranty
Good customer support, spare parts availability, and a good warranty keep your mind at ease and your operation smooth. Working with a manufacturer with good after-sales service minimizes your maintenance costs and downtime.
Conclusion
Selecting a suitable sheet metal rolling machine is very important for getting precision, efficiency, and affordability in metal fabricating. Some of the features which include roller configuration, material capacity, automation, safety, and durability must be considered by companies during their processes in buying a machine that satisfies their particular needs. With a constant increase in technology, modern sheet metal rolling machines are turning more efficient and friendly, making them a must-have for industries such as automotive, aerospace, construction, and shipbuilding.
Leave a Reply