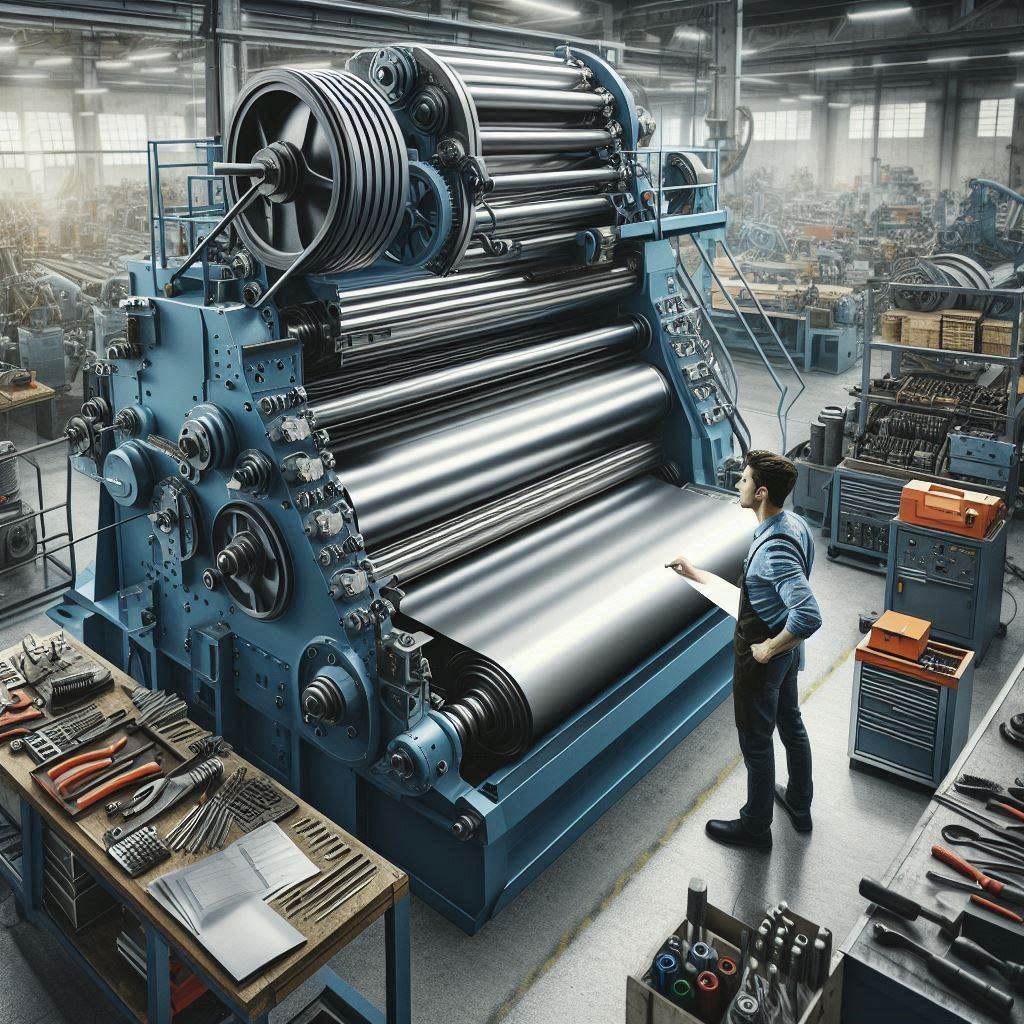
An excellent example of a rolling machine for sheet metal is designed for bending and forming sheet metals into tubular shapes with high precision, curvilinear shapes, and even conical shapes. The material is bent using several rollers, which are pressed together under controlled conditions while passing the metal through the rollers for gradual bending into shape. Such machines are vital in the automotive, aerospace, shipbuilding, and metals fabricating industries as they require parts rolled to fine tolerances both for strength in buildings and accuracy in design. The evolution of rolling machines has now led to hydraulic, mechanical, and CNC-controlled rollers, enabling sheet metal rolling machines to be more effective, repeatable, and customizable compared to earlier models. Such machines have become indispensable in producing quality metal forming.
Essential components of Sheet metal roller machines
According to this statement about a machine essentially working on metal forming, some of the most important components of a sheet roller machine act together in order to achieve an accurate and effective process. The rollers (or rolls) are the prime distinguished elements made up of hardened steel that apply pressure to the metal sheet in order to shape it into the desired curvature. The frame provides that stability, supporting the rollers with other mechanical components. The drive system has hydraulic motion drivers, mechanical drivers, or electric motors, influencing the motions and velocities of the rollers. The adjustment mechanism permits the operator to change roller positions in compliance with different bending situations. Modern sheet metal rollers, therefore, have CNC controls for automation that make it possible to program with precision, followed by repeatable accuracy. Safety considerations, such as an emergency stop and overload protection, assist in keeping the operator secure, which is why these machines are trustworthy and manufactured by reliable Sheet metal roller manufacturer.
Working principle of Sheet metal roller machines
Sheet metal roller machines work on the principle of controlled bending of metal sheets by means of multiple rollers to produce the desired curvature. These machines generally consist of three or four rollers arranged in such a way as to receive the metal sheet between them. The top roller pushes down while the bottom rollers provide support and movement, thereby forcing the gradual bending of the metal through the rollers. By changing the position of the rollers, the adjustments can be made for the bending radius in which the operators can get exactly curved parts or cylindrical ones. This process is automated for consistency, accuracy, and efficiency on modern CNC-controlled roller machines. This method finds application in industries such as shipbuilding, automotive, and construction, where the forming of curvilinear shapes in metals is essential.
Conclusion
To conclude, sheet metal roller machines are vital for the metal-processing industry as they enable the accurate yet efficient bending of metal sheets into the cylindrical, curved, or conical shapes. Therefore, high-quality results with little room for variation allow their application across the automotive, aerospace, and shipbuilding industries. Advancements in CNC automation, hydraulic systems, and safety features make the modern roller machine more efficient, accurate, and customizable than the older machines. As technology develops, sheet metal roller machines will continue to serve as an invaluable tool for industries to satisfy the increasing demand for complex and high-precision metalwork.
Β
Leave a Reply