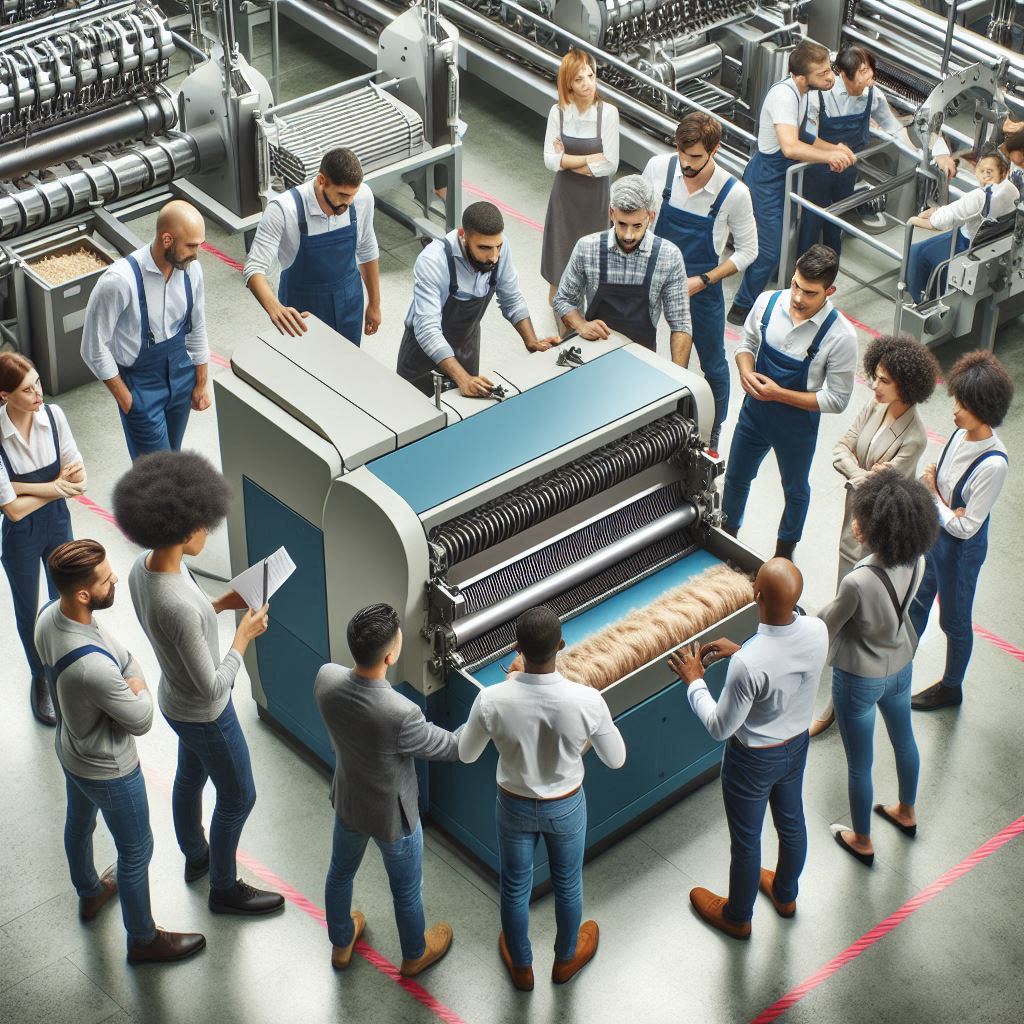
A sheet metal press brake works on the principle of subjecting metal sheets to a controlled amount of forces to bend them into required shapes. The sequence of operations begins with positioning the metal sheet onto the die, which is the base for forming. The ram (or punch) moves downwards applying controlled force against the sheet pressed against the die, providing the required bend angle. The back gauge works as an assurance that repeatable bends can be accurately positioned, while the new CNC-controlled press brakes can program bending sequences that allow for improved precision and efficiency. Different dies and punching tools can be set up in accordance with the thickness of a material, the angle of bend, and the complexity of the design. The press brake, with its ability to generate forces, provide positioning, and automate, produce high-quality, consistent bends for the automotive, aerospace, and metal fabrication industries.
Applications and uses of Sheet metal press brake machine
Sheet metal press brake machines are used in different industries to fulfill their requirements in a very accurate bending and shaping task of metal sheets. Precision bending in automotive manufacturing is done for producing body panels, chassis components, and brackets. The aerospace industry has press brakes for the purposes of forming aircraft structures and, hence, facilitation of their lightweight and durability characteristics. The construction sector depends greatly on press brake machines for producing metal frames, doors, and roofing elements. Still, electrical enclosures, furniture, and kitchen equipment are made through precise bends and custom designs using a press brake. The press machine works with all metals such as steel, aluminum, and copper, and is, thus, a necessity in metal fabrication, shipbuilding, and in heavy machinery production, facilitating the capability of producing high-quality, accurate, and repeatable metal components efficiently.
How Sheet metal press brake machine helps in revolutionizing the forging sector?
The sheet metal press brake machine has brought revolution in forging in terms of high precision, better efficiency, and automation involved in metal bending and shaping processes. Old forging techniques, where huge manpower and heat were involved, have been replaced by modern press brakes that use CMC controls, hydraulic systems, and servo-electric technology, such that without wasting materials, bending works accurately and reproducibly. These pieces of equipment enable forgers to use strong metals, thereby ensuring such machining products are of a higher quality and more consistent in manufacturing automotive, aerospace, and heavy lift equipment components. Besides, complex bending sequences programmed for automation production have considerably reduced lead time and labor cost, ultimately making the forging sector very competitive in meeting advanced industrial application demands.
Conclusion
This machine works by bending metal sheets with controlled pressure application on sheet metal working. These press brakes are made to be accurate with each and every bend in all industries because of integrating CNC automation with adjustable dies or probes, as well as precision positioning systems. They can perform varieties of materials and very complex designs, making them classics in most automotive, aerospace, construction, and metal fabrication industries. The improvement in precision and efficiency keeps advancing, making these sheet metal press brake machines one of the modern manufacturing tools to innovate and maintain the highest-quality production among industrial applications.
Leave a Reply