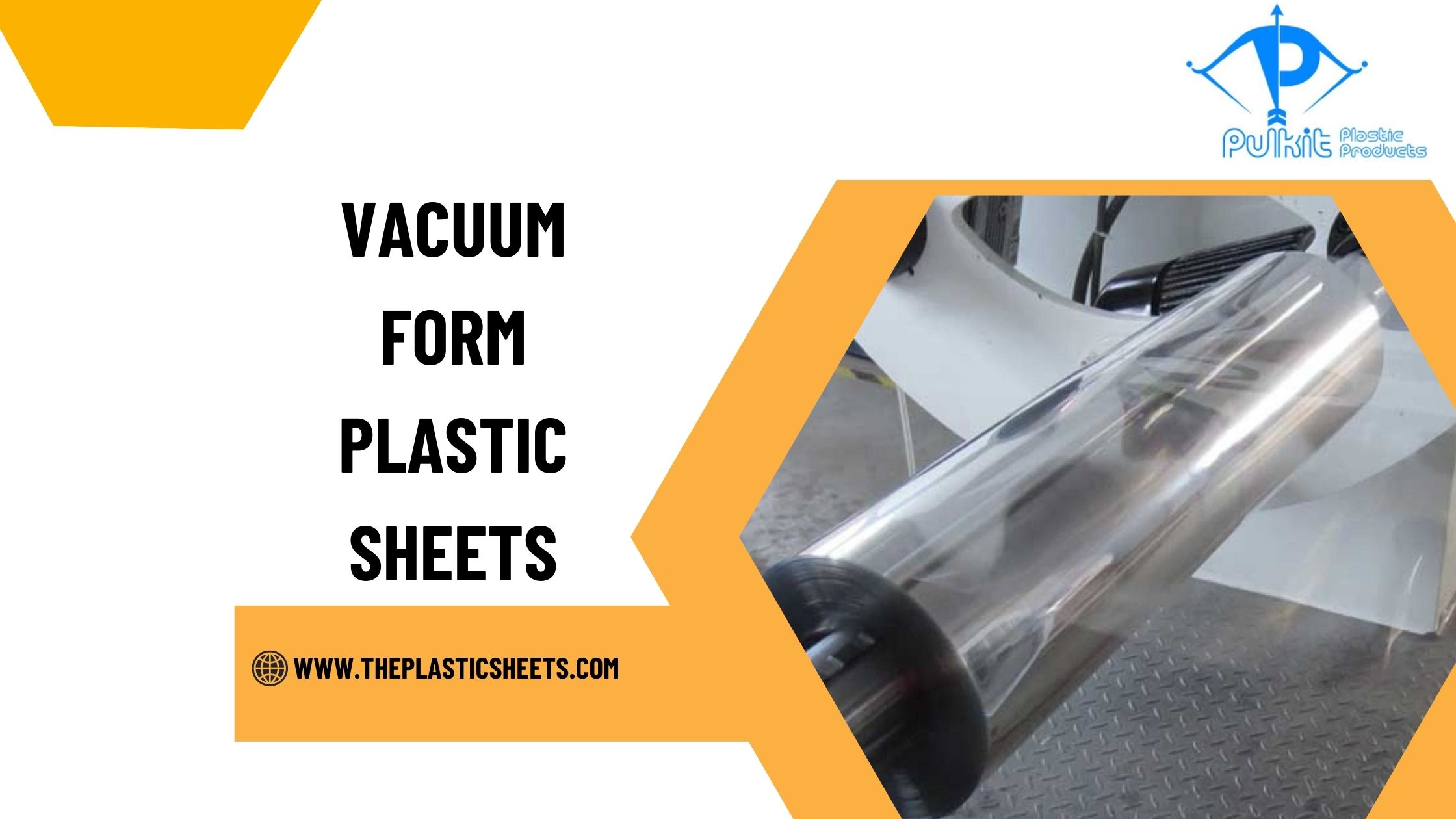
In todayβs fast-paced world of product design and manufacturing, innovation is at the core of success. Industries are constantly on the lookout for new ways to improve efficiency, reduce costs, and provide more versatile, durable, and aesthetically pleasing products. One technology that has greatly transformed product design in recent years is vacuum forming. This process, combined with high-quality vacuum forming machine plastic sheets, has opened up a wealth of opportunities for designers and manufacturers across a range of industries. In this article, we will explore how vacuum form plastic sheets are revolutionizing product design and the various advantages they offer.
What Are Vacuum Form Plastic Sheets?
Vacuum form sheets are flat plastic sheets that are heated to a specific temperature and then molded into a three-dimensional shape using a vacuum forming process. During this process, the heated thermoplastic sheet is placed over a mold. A vacuum is then applied, pulling the plastic tightly around the mold to create a precise, custom shape. Once cooled, the plastic sheet retains the form of the mold, providing a high-quality product that can be used in a wide range of applications.
One of the main advantages of using Thermoplastic sheets for vacuum forming is their ability to be reshaped and remolded. Thermoplastics can be heated to their melting point, which allows them to be formed into virtually any shape, offering unparalleled versatility compared to other materials. The ability to reuse and remold thermoplastic sheets makes them highly sustainable, reducing material waste.
How Vacuum Forming Works
The vacuum forming process involves several key steps:
-
Sheet Preparation: The plastic sheet, typically made from thermoplastic materials such as ABS, polystyrene, or PVC, is selected based on the product’s requirements. These sheets are typically between 0.25mm to 10mm thick and are chosen for their strength, flexibility, and ability to maintain shape.
-
Heating: The plastic sheet is heated in an oven until it becomes soft and flexible. The temperature must be carefully controlled to ensure that the plastic does not become too hot and lose its ability to be molded.
-
Molding: Once the sheet reaches the desired temperature, it is quickly placed over a mold. The mold can be made of metal, wood, or other materials, depending on the application. A vacuum is then applied to the sheet, pulling it tightly against the mold and forcing it to take the shape of the moldβs contours.
-
Cooling: After the plastic has conformed to the mold, it is cooled to solidify the material. This step ensures that the vacuum-formed sheet retains its new shape.
-
Trimming: Once the sheet is cooled, the excess material around the edges is trimmed, and the final product is inspected for quality.
How Vacuum Form Plastic Sheets Are Revolutionizing Product Design
Vacuum forming has brought significant improvements to product design, and the use of vacuum forming machine plastic sheets has only accelerated this transformation. Letβs take a closer look at the key benefits vacuum forming offers in modern product design.
1. Cost-Effective Production
One of the primary benefits of using vacuum form plastic sheets is the cost-effectiveness of the manufacturing process. Unlike traditional injection molding, vacuum forming requires fewer materials and lower labor costs, making it a more affordable option for manufacturers. Additionally, the tools and molds used in vacuum forming are generally less expensive and easier to produce. This makes vacuum forming a great choice for companies looking to produce high-quality products in smaller quantities or with limited budgets.
For industries that require rapid prototyping, vacuum forming offers a more affordable alternative to other methods of production. Manufacturers can quickly create prototypes and test them in real-world applications without investing in expensive tooling or large-scale production runs.
2. Versatility in Design
Another significant advantage of Vacuum form sheets is the versatility they offer in design. The ability to use different types of thermoplastic materials allows designers to create products with a wide range of properties, such as flexibility, durability, and resistance to environmental factors.
Because the vacuum forming process involves heating and molding the plastic, designers have the freedom to create complex shapes, contours, and designs that may be difficult or impossible to achieve using traditional manufacturing methods. This flexibility is particularly beneficial for industries like automotive, consumer electronics, packaging, and medical devices, where intricate designs are often needed to meet specific functional and aesthetic requirements.
3. Lightweight Yet Durable Products
One of the key benefits of using thermoplastic sheets for vacuum forming is the ability to produce lightweight but strong products. The use of materials such as ABS, polystyrene, PVC, and polypropylene allows designers to create lightweight products without compromising on durability. These materials are often chosen for their ability to withstand impact, resist corrosion, and offer excellent UV stability.
For industries like automotive or aerospace, where weight is a critical factor, vacuum forming enables the production of lightweight components that do not sacrifice strength or performance. This is particularly important for improving fuel efficiency and overall performance in these industries.
4. Customization and Prototyping
Vacuum forming allows for easy customization and prototyping. Once a mold is created, it can be used repeatedly to create multiple products with the same design. This means that manufacturers can create customized products for individual customers or clients, which is particularly beneficial in industries like packaging or consumer goods.
The vacuum forming process is ideal for creating prototypes for product testing or market research. Designers can quickly create prototype designs and test them for functionality, ergonomics, and appeal before proceeding to large-scale production. This flexibility in prototyping helps businesses reduce the time-to-market for new products and makes the design process more agile.
5. Sustainability and Eco-Friendliness
The use of thermoplastic sheets for vacuum forming offers an eco-friendly solution for product design. Thermoplastics can be recycled and remolded, reducing waste and promoting sustainability. When products made from thermoplastic materials reach the end of their life cycle, they can often be recycled into new products, helping to reduce the environmental impact of plastic waste.
Moreover, the ability to create thin yet durable materials means that less plastic is needed for each product, further reducing the amount of material waste generated during the manufacturing process.
Applications of Vacuum Form Plastic Sheets in Product Design
Vacuum forming is used in a wide range of industries, from automotive and medical devices to packaging and consumer products. Some of the most common applications include:
-
Packaging: Vacuum form sheets are commonly used to create protective packaging for fragile or delicate items. These sheets are molded to fit the contours of the product, providing a secure and protective barrier against damage during transport and storage.
-
Automotive Industry: Vacuum forming is used to produce interior components, such as dashboard panels, door panels, and trim pieces, due to the lightweight and durable properties of thermoplastic materials.
-
Consumer Goods: Many consumer products, such as kitchen appliances, electronics, and toys, are made using vacuum formed plastic sheets due to their ability to create intricate designs at a low cost.
-
Medical Devices: Vacuum forming is also used to create medical device components, such as trays, containers, and packaging for medical products, where precision and hygiene are paramount.
-
Signage and Displays: Vacuum-formed plastic sheets are often used to create signs and displays with three-dimensional designs, allowing businesses to create eye-catching marketing materials.
Pulkit Plastic Products: A Leading Supplier of Vacuum Form Sheets
As demand for vacuum forming continues to rise, companies like Pulkit Plastic Products play a crucial role in providing high-quality vacuum form sheets to businesses across a variety of industries. Pulkit Plastic Products specializes in offering a wide range of Vacuum forming machine plastic sheets, including thermoplastic materials suitable for different applications. Their products are known for their durability, precision, and versatility, making them an excellent choice for businesses looking to integrate vacuum forming into their product design process.
Pulkit Plastic Products ensures that their vacuum form sheets meet the highest standards of quality and performance, offering customized solutions to meet the specific needs of their clients. With a commitment to innovation and customer satisfaction, Pulkit Plastic Products is a trusted partner for companies seeking reliable and cost-effective solutions for their vacuum forming needs.
Conclusion
Vacuum form plastic sheets are undoubtedly revolutionizing product design by offering manufacturers and designers an affordable, versatile, and sustainable method for creating custom products. Whether it’s in packaging, automotive, medical devices, or consumer goods, the ability to mold thermoplastic materials into intricate shapes opens up endless possibilities for product development. As businesses continue to seek innovative solutions to streamline production and enhance design capabilities, vacuum forming will remain at the forefront of manufacturing technology, enabling companies to bring new and exciting products to market with greater speed and efficiency.
Frequently Asked Questions (FAQ)
1. What types of materials are used for vacuum forming?
Common materials used in vacuum forming include ABS, PVC, polystyrene, polypropylene, and PET. These thermoplastic materials are chosen for their flexibility, durability, and ease of molding.
2. What are the advantages of using vacuum forming for product design?
Vacuum forming offers several benefits, including cost-effectiveness, versatility, lightweight durability, and the ability to create complex and custom shapes. It is also ideal for prototyping and small to medium production runs.
3. Can vacuum forming be used for large-scale production?
Yes, vacuum forming can be used for both small and large-scale production runs. The process is particularly efficient for medium-volume production, offering a balance between cost and customization.
Leave a Reply