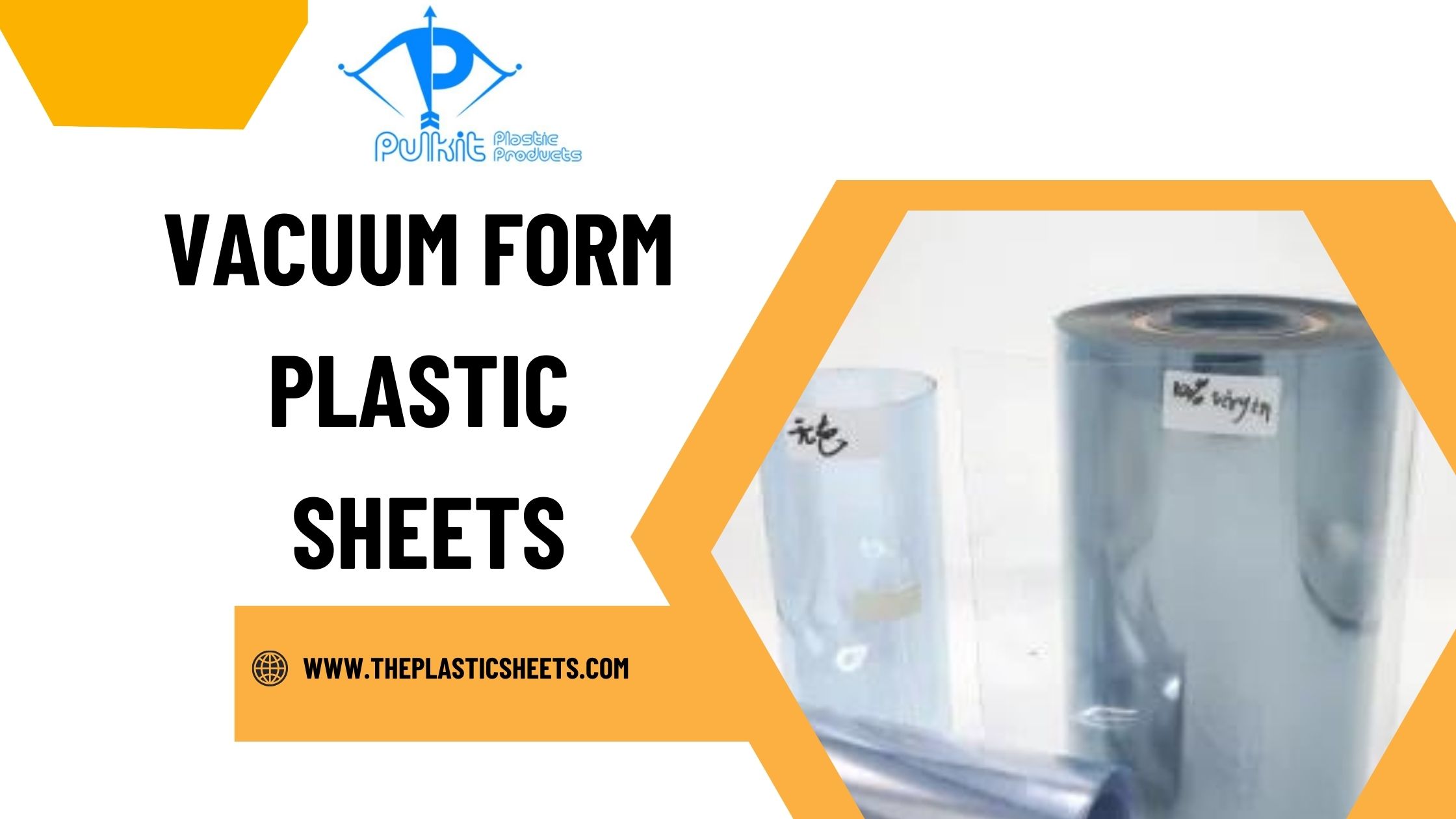
Β
In the world of manufacturing, efficiency and precision are key to ensuring that products meet both quality and cost expectations. One of the most innovative techniques used in various industries is vacuum forming, a method that involves molding plastic into specific shapes by applying heat and pressure. The main tool in this process is the vacuum form plastic sheets, which play an essential role in producing a wide range of items across different sectors. From packaging to automotive parts and medical devices, vacuum-formed plastic sheets offer remarkable versatility that manufacturers can rely on for consistent, high-quality results.
In this article, we explore the benefits, applications, and key considerations for using Vacuform plastic sheets in manufacturing, as well as provide answers to frequently asked questions. We will also introduce vacuum forming plastic sheet suppliers and companies like Pulkit Plastic Products, which specialize in providing top-quality plastic sheets for vacuum forming processes.
What Are Vacuum Form Plastic Sheets?
Vacuum form plastic sheets are thin, flat sheets of thermoplastic material used in the vacuum forming process. The material is typically made from plastic resins such as polystyrene, ABS, polycarbonate, or PET, depending on the application. These sheets are heated to a specific temperature where they become soft and pliable. They are then placed over a mold, and a vacuum is applied to form the plastic tightly around the moldβs contours, creating a custom shape. Once the plastic has cooled and solidified, it retains the shape of the mold, making it ideal for producing intricate, detailed, and consistent products.
The versatility of Vacuum form plastic sheets lies in their ability to take on complex shapes with high accuracy, while being cost-effective and efficient. The process is highly customizable, making it suitable for a wide range of applications across various industries.
Benefits of Vacuum Form Plastic Sheets
-
Cost-Effectiveness: Compared to other molding methods like injection molding, vacuum forming is more affordable, especially for small to medium production runs. The tooling costs for vacuum forming are typically lower, making it an ideal choice for startups and companies looking to produce custom products without a large initial investment.
-
Speed and Efficiency: Vacuum forming is known for its fast turnaround time. Since the process uses pre-formed plastic sheets, the overall cycle time is reduced, making it an ideal method for meeting tight deadlines. Additionally, the ability to quickly modify molds allows manufacturers to adapt and make changes to designs with minimal delay.
-
Customization: One of the biggest advantages of using vacuum form plastic sheets is the high level of customization they allow. Whether it’s the shape, size, texture, or color, vacuum forming can be tailored to meet specific design and functional requirements. This makes it a versatile solution for creating unique products that stand out in the market.
-
Durability and Strength: Plastic materials used in vacuum forming are incredibly durable and lightweight. This makes the resulting products resistant to damage and wear while remaining easy to handle and transport. Vacuum-formed plastic is also resistant to corrosion and environmental degradation, ensuring a long lifespan for most applications.
-
Low Waste: The vacuum forming process is highly efficient in terms of material usage. Since the plastic is heated and molded directly to the required shape, waste is minimized compared to other processes like injection molding, which involves excess material that needs to be removed.
-
Variety of Material Choices: Manufacturers can choose from a wide range of thermoplastic materials for their vacuum form plastic sheets, depending on the product’s requirements. These materials can include clear, colored, or textured finishes, allowing for a diverse range of visual and functional properties.
Applications of Vacuum Form Plastic Sheets
The versatility of vacuum forming makes it suitable for a broad spectrum of industries. Here are some of the most common applications:
-
Packaging: One of the most prominent uses of vacuum-formed plastic is in the packaging industry. Custom trays, blister packs, and clamshell packaging are often made from vacuum form plastic sheets. These products protect delicate items while providing a transparent view, making them both functional and visually appealing.
-
Automotive Parts: Vacuum forming is used to manufacture lightweight, durable parts for the automotive industry, such as dashboard panels, door trims, and exterior body panels. The ability to mold plastic around complex curves and shapes makes it a favored method for producing parts that are both aesthetically pleasing and functional.
-
Medical Devices: The medical industry relies heavily on vacuum forming to create customized, sterile packaging for medical instruments and devices. Vacuum-formed plastic sheets are also used to make components such as trays, casings, and protective covers, where cleanliness and precision are paramount.
-
Signage: Vacuum-formed plastic is widely used to create custom signs and displays. The ability to mold plastic sheets into 3D shapes makes it an ideal solution for creating eye-catching signs, logos, and other promotional displays for businesses.
-
Consumer Goods: From kitchen appliances to toys, vacuum-formed plastic sheets are commonly used to produce parts and casings for consumer products. The versatility of plastic materials allows manufacturers to produce intricate designs that are both functional and attractive.
-
Electronics: Vacuum forming is used in the electronics industry to create custom housings, protective casings, and internal components for a variety of electronic devices, such as computers, smartphones, and television sets.
Choosing the Right Vacuum Form Plastic Sheet Supplier
When selecting a supplier for vacuum form plastic sheets, itβs essential to consider factors like material quality, range of options, and customer service. Companies like Pulkit Plastic Products specialize in providing high-quality plastic sheets for vacuum forming processes, offering a variety of materials and thicknesses to suit specific applications.
Itβs also important to ensure that the supplier can meet your production volume and delivery requirements, especially if you have tight deadlines. Established Vacuum forming plastic sheet suppliers like Pulkit Plastic Products have the necessary expertise to provide tailored solutions and guidance on selecting the best materials for your needs.
Β
Conclusion
The versatility of vacuum form plastic sheets in manufacturing cannot be overstated. Their ability to be molded into complex shapes, combined with cost-effectiveness and efficiency, makes them an indispensable tool in numerous industries, from packaging to automotive and electronics. Companies like Pulkit Plastic Products provide high-quality materials that can help manufacturers create durable, customized products to meet their specific needs.
By leveraging the benefits of vacuum forming, businesses can streamline production, reduce costs, and bring innovative products to market quickly and efficiently. Whether you’re looking for packaging solutions, custom components, or intricate designs, vacuum form plastic sheets are the perfect solution for a wide range of manufacturing needs.
FAQΒ
1. What materials are used for vacuum forming plastic sheets?
Common materials for vacuum forming include polystyrene (PS), acrylonitrile butadiene styrene (ABS), polycarbonate (PC), polyethylene (PE), and polypropylene (PP). Each material offers unique properties such as flexibility, impact resistance, and clarity, allowing manufacturers to select the best option for their application.
2. Can vacuum forming be used for both small and large production runs?
Yes, vacuum forming is highly versatile and can be used for both small and large production runs. However, for large runs, injection molding may be more cost-effective, as it offers faster cycle times. For small runs, vacuum forming is often the preferred method due to its lower tooling costs.
Leave a Reply