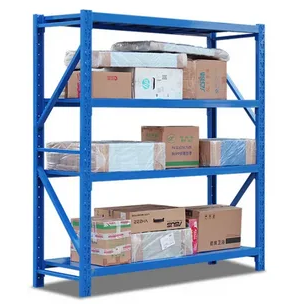
Warehouse storage racks are essential for optimizing storage space, improving inventory management, and enhancing workflow efficiency in warehouses, distribution centers, and industrial facilities. With the right racking system, businesses can maximize space utilization, reduce operational costs, and increase productivity. This guide explores different types of warehouse storage racks, their benefits, and key considerations for selecting the best system for your needs.
Understanding Warehouse Storage Racks
Warehouse storage racks are structured frameworks designed to store goods efficiently. They provide organized storage, allowing easy access to inventory while maximizing vertical and horizontal space utilization. The selection of an appropriate racking system depends on factors such as the type of inventory, warehouse layout, load capacity, and accessibility requirements.
Types of Warehouse Storage Racks
1. Selective Pallet Racking
Selective pallet racking is one of the most commonly used systems in warehouses. It allows for easy access to every pallet, making it ideal for facilities with a high SKU (Stock Keeping Unit) variety. This system is flexible, scalable, and suitable for businesses that require frequent inventory turnover.
Advantages:
-
Direct access to each pallet
-
Cost-effective and easy to install
-
Compatible with various forklift types
2. Drive-In and Drive-Through Racking
These systems are designed for high-density storage, minimizing aisle space and increasing storage capacity. Drive-in racking allows forklifts to enter from one side, while drive-through racking permits entry from both ends.
Advantages:
-
Ideal for storing large quantities of similar products
-
Maximizes warehouse space
-
Suitable for Last-In, First-Out (LIFO) and First-In, First-Out (FIFO) inventory systems
3. Push-Back Racking
Push-back racking utilizes inclined rails and rolling carts to store multiple pallets in a single lane. When a new pallet is loaded, it pushes the previous pallet back, optimizing space while ensuring efficient inventory retrieval.
Advantages:
-
High storage density
-
Reduces forklift travel time
-
Ideal for LIFO inventory systems
4. Cantilever Racking
Designed for long and bulky items such as lumber, pipes, and steel bars, cantilever racks feature horizontal arms extending from vertical columns, providing open-front access.
Advantages:
-
Accommodates oversized and irregularly shaped items
-
Easy loading and unloading
-
Customizable to different load capacities
5. Pallet Flow Racking
Pallet flow racking, also known as gravity flow racking, uses inclined rollers or wheels to allow pallets to move smoothly from the loading end to the retrieval end. This system supports FIFO inventory management, making it suitable for perishable goods.
Advantages:
-
Ideal for high-turnover inventory
-
Reduces manual handling and labor costs
-
Increases picking efficiency
6. Mezzanine Racking
Shelving and racking utilize vertical space by adding an additional storage level within the warehouse. This cost-effective solution helps businesses expand their storage capacity without relocating.
Advantages:
-
Maximizes vertical space utilization
-
Customizable for different warehouse needs
-
Enhances storage efficiency
Key Factors to Consider When Choosing a Warehouse Storage Rack
1. Load Capacity and Weight Distribution
Understanding the weight and size of the items stored is crucial for selecting a racking system with the appropriate load capacity. Overloading racks can compromise structural integrity and lead to safety hazards.
2. Warehouse Layout and Space Optimization
Analyzing the warehouse layout helps determine the best racking configuration to maximize space utilization while ensuring smooth workflow and easy access to inventory.
3. Accessibility and Picking Frequency
For warehouses with high inventory turnover, selective racking systems provide quick and direct access to goods. High-density storage systems like drive-in or push-back racking are more suitable for bulk storage with lower picking frequency.
4. Safety and Compliance
Warehouse storage racks should comply with safety regulations and industry standards to prevent accidents. Regular inspections, load capacity signage, and employee training contribute to a safer working environment.
5. Scalability and Future Expansion
Choosing a modular and adaptable racking system allows businesses to expand storage capacity as operational needs grow. Investing in scalable solutions ensures long-term efficiency.
Benefits of Efficient Warehouse Storage Racks
-
Maximized Space Utilization: Optimizes vertical and horizontal storage, reducing wasted space.
-
Improved Inventory Management: Enhances organization and accessibility, minimizing retrieval time.
-
Increased Productivity: Streamlines warehouse operations, reducing downtime and labor costs.
-
Enhanced Safety: Properly designed racks reduce the risk of accidents and product damage.
-
Cost Savings: Efficient racking solutions lower storage costs and improve warehouse efficiency.
Conclusion
Selecting the right warehouse storage rack system is essential for optimizing storage capacity, improving operational efficiency, and ensuring workplace safety. By understanding the different types of racking systems and their benefits, businesses can make informed decisions that align with their storage needs. Whether you require selective pallet racking for quick access, drive-in racks for high-density storage, or cantilever racking for oversized items, investing in a well-structured storage system can significantly enhance warehouse operations.
Leave a Reply