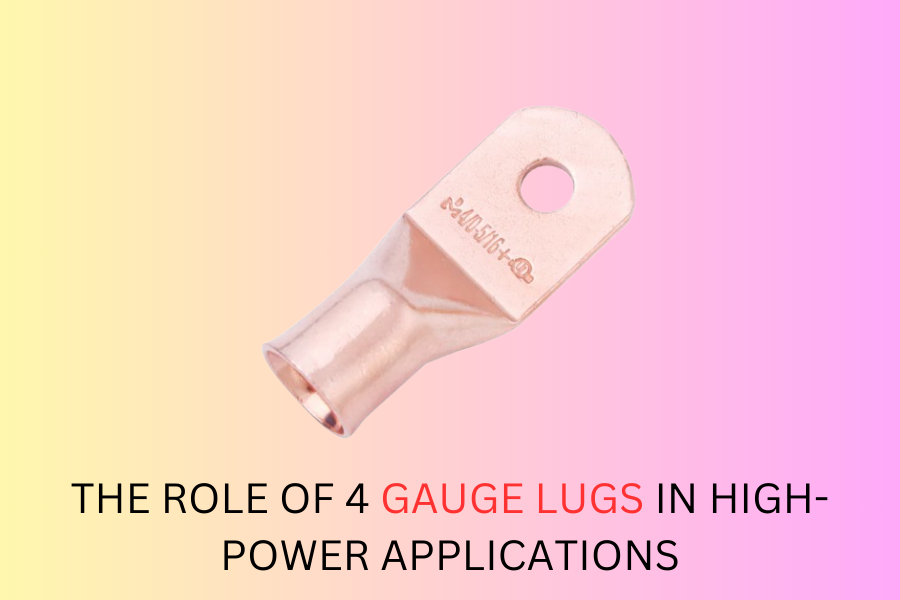
In the realm of high-power electrical systems, the reliability and efficiency of power delivery depend on every component in the circuit. One such critical component is the cable lug, specifically 4/0 AWG Cable Lug, which play a significant role in ensuring secure, efficient, and safe electrical connections. These lugs, designed for 4 AWG (American Wire Gauge) cables, are integral in high-power applications ranging from automotive systems to industrial machinery and renewable energy installations. This article explores the role of 4 gauge lugs, their design, material choices, and importance in high-power systems.
Understanding 4 Gauge Lugs
4/0 AWG Cable Lug are terminal connectors specifically designed for 4 AWG cables, which are commonly used in high-current scenarios. These cables, with a diameter of approximately 5.2 mm (0.204 inches), are capable of carrying substantial currents, often exceeding 100 amps depending on the insulation and application. The lug serves as the termination point where the cable is securely attached to a terminal, device, or power distribution system.
Key Features of 4 Gauge Lugs
- Material Composition: Most 4 gauge lugs are made from highly conductive materials like copper or aluminum. Copper lugs are preferred in high-performance applications due to their superior conductivity and resistance to corrosion. Aluminum lugs, though less conductive, are lightweight and cost-effective, making them suitable for specific uses.
- Plating Options: Copper lugs often come with a tin or nickel plating to enhance corrosion resistance, especially in harsh environments. Tin-plated lugs are common in automotive and marine applications where exposure to moisture and salt can lead to oxidation.
- Design Variants: Lugs come in various designs, such as ring, spade, or pin terminals, catering to different connection requirements. Ring terminals are popular for their secure fit, as the bolt passes through the lug, ensuring a firm connection even under vibration.
- Compatibility with Insulation Types: 4 gauge lugs are compatible with different cable insulation types, including PVC, XLPE, and silicone. Heat-shrink tubing or molded insulation is often applied after crimping to provide additional electrical insulation and mechanical protection.
Applications in High-Power Systems
The use of 4 gauge lugs is widespread in applications where high currents and durability are paramount. Below are some prominent areas where these components are indispensable:
- Automotive and Marine Systems: Modern vehicles and marine vessels rely heavily on robust electrical systems to power engines, auxiliary devices, and communication systems. 4 gauge lugs are used for battery connections, alternators, and grounding systems, providing reliable performance in high-vibration environments.
- Renewable Energy Installations: Solar panels, wind turbines, and energy storage systems utilize 4 AWG cables and lugs for interconnections. These systems demand high-efficiency components to minimize energy losses, making copper lugs a preferred choice.
- Industrial Machinery: Heavy machinery in manufacturing and mining operations often requires 4 gauge cables to handle high currents. Lugs ensure secure connections in motor control panels, power distribution units, and other critical components.
- Audio and Home Theater Systems: High-end audio systems often use 4 AWG cables and lugs for amplifiers and speakers, ensuring minimal signal loss and superior sound quality.
Installation Best Practices
For 4/0 Ring Terminals to perform optimally, proper installation is crucial. Here are some best practices:
- Crimping: Crimping is the most common method for attaching lugs to cables. Using a high-quality crimping tool ensures a secure and consistent connection, reducing the risk of resistance or overheating at the joint.
- Soldering: In some applications, soldering may be used alongside crimping to enhance mechanical strength and conductivity. However, itβs essential to avoid over-soldering, which can weaken the joint.
- Insulation: After installation, covering the lug with heat-shrink tubing or insulation tape is vital to protect against short circuits, moisture, and physical damage.
- Torque Specifications: When fastening lugs to terminals, adhering to the manufacturerβs recommended torque specifications is important to prevent loosening or damage to the lug or terminal.
Advantages of 4 Gauge Lugs in High-Power Applications
- Efficiency: With their high conductivity and secure fit, 4 gauge lugs minimize electrical resistance and energy losses in high-power systems.
- Durability: Designed to withstand harsh conditions, these lugs provide long-lasting performance in environments exposed to temperature extremes, moisture, and mechanical stress.
- Safety: Properly installed 4 gauge lugs reduce the risk of overheating, short circuits, and loose connections, enhancing the overall safety of electrical systems.
- Versatility: Available in various designs and materials, these lugs are adaptable to a wide range of applications and environments.
Conclusion
4/0 Ring Terminals are an essential component in high-power electrical systems, playing a pivotal role in ensuring efficient and reliable power delivery. Their robust design, high conductivity, and versatility make them a cornerstone in industries ranging from automotive to renewable energy. By adhering to proper installation practices and selecting the appropriate lug for the application, engineers and technicians can maximize the performance and longevity of electrical systems. In high-power applications where reliability is non-negotiable, 4 gauge lugs are a small but indispensable piece of the puzzle.
Leave a Reply