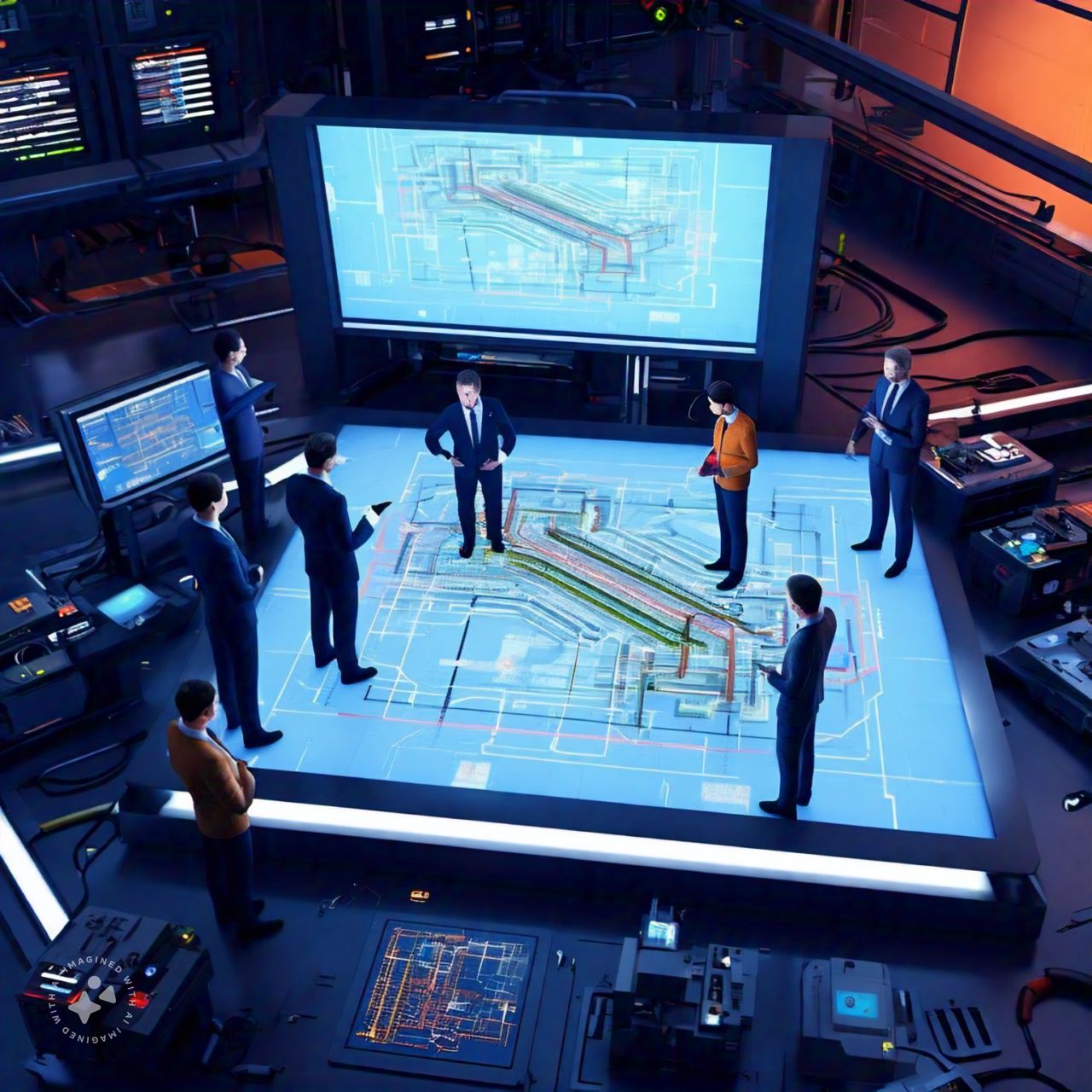
Digital Twin technology has been steadily revolutionizing industrial processes, offering unprecedented opportunities for simulation, monitoring, and optimization. As we move into an era of increased digital transformation, the role of Digital Twins in industrial applications is set to grow exponentially. This article explores the future potential of Digital Twin technology and its transformative impact on industries worldwide.
What is Digital Twin Technology?
A Digital Twin is a virtual replica of a physical asset, system, or process. By integrating real-time data with advanced analytics, it allows businesses to simulate and monitor operations in a digital environment. This technology not only enhances operational efficiency but also aids in predictive maintenance, reducing downtime and costs.
Key Benefits in Industrial Applications
-
Predictive Maintenance
With Digital Twins, industries can predict potential failures before they occur. By analyzing real-time data from sensors, businesses can schedule maintenance activities proactively, reducing unexpected downtimes and extending the lifespan of equipment. -
Process Optimization
Digital Twins allow for the simulation of different scenarios, enabling industries to identify inefficiencies and optimize workflows. This results in reduced waste, lower costs, and improved productivity. -
Enhanced Safety
Industries like manufacturing and energy face significant risks. Digital Twins can simulate hazardous scenarios, allowing operators to test safety protocols in a risk-free environment. -
Real-Time Monitoring
Real-time data integration ensures continuous monitoring of operations. This transparency helps industries maintain quality control and quickly adapt to any changes in conditions.
Emerging Trends in Digital Twin Technology
-
Integration with AI and Machine Learning
The combination of Digital Twins with AI and machine learning is paving the way for smarter systems. AI-driven insights can provide even more accurate predictions and automation of complex processes. -
5G Connectivity
The rollout of 5G networks is enhancing the capabilities of Digital Twins by enabling faster data transfer and real-time communication, crucial for industries relying on IoT devices. -
Sustainability Applications
As sustainability becomes a global priority, Digital Twins are being used to model and optimize energy consumption and reduce carbon footprints. -
Advanced Simulations in Complex Systems
Industries such as aerospace and healthcare are leveraging Digital Twins for highly complex systems, including aircraft engines and human organs. These advancements demonstrate the versatility and potential of the technology.
Future Impact on Industries
- Manufacturing: Digital Twins will drive the adoption of smart factories, enhancing productivity and efficiency through automation and predictive analytics.
- Energy: Power grids and renewable energy projects will benefit from precise simulations and efficient resource management.
- Healthcare: Virtual replicas of medical devices and even patient-specific models are being developed to personalize treatment plans.
- Construction: Digital Twins can simulate entire buildings, enabling better project planning and maintenance.
Conclusion
Digital Twin technology is set to redefine industrial applications by delivering cost savings, operational excellence, and enhanced safety. Its integration with emerging technologies such as AI and IoT will further cement its role as a cornerstone of the digital revolution. As industries continue to innovate, Digital Twins will undoubtedly play a critical role in shaping the future of industrial operations.
Leave a Reply