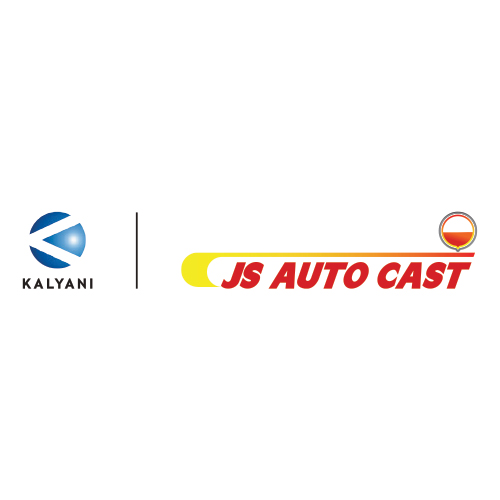
Finding the Right SG Iron Casting Manufacturer: A Comprehensive Guide
JS Auto Cast Pvt Ltd is a prominent producer of Spheroidal Graphite Iron (SG Iron), also known as ductile iron, which stands as a versatile and robust material in modern manufacturing. Its unique blend of strength, ductility, toughness, and wear resistance makes it a preferred choice for a wide spectrum of industrial applications, from automotive components and agricultural machinery to heavy-duty industrial equipment and wind turbine parts. The quality of SG iron castings directly impacts the performance, reliability, and longevity of the final product. Therefore, selecting the right SG iron casting manufacturer is a critical decision for any business. This comprehensive guide delves into the essential factors to consider when choosing a manufacturing partner, ensuring you receive high-quality castings that meet your specific needs and contribute to your project’s success.
- Experience and Expertise: The Foundation of QualityΒ
A manufacturer’s experience and expertise are fundamental indicators of their ability to deliver consistent, high-quality SG iron castings. Don’t underestimate the value of a proven track record in this specialized field.Β Β
- Years in Business: The number of years a manufacturer has been operating provides valuable insight into their accumulated knowledge, understanding of the casting process, and ability to navigate industry challenges. A longer presence often suggests a stable and reliable business, demonstrating a commitment to the industry and a capacity to adapt to evolving market demands. While newer companies can offer innovative approaches, established manufacturers typically possess a deeper understanding of material properties, process optimization, and quality control.
- Specialization and Industry Focus: Some manufacturers specialize in specific types of SG iron castings, such as complex geometries, thin-walled castings, or high-volume production. Others cater to particular industries, like automotive, agriculture, or energy. Choosing a manufacturer whose specialization aligns with your specific product requirements and target industry can be advantageous. They will likely have a deeper understanding of the specific challenges and quality standards associated with your application.
- Technical Expertise and Engineering Capabilities: Assess the manufacturer’s technical capabilities beyond just production. Do they have a team of experienced engineers, metallurgists, and technicians who can provide valuable support throughout the product lifecycle? Can they offer design assistance, material selection guidance, simulation and analysis, and process optimization? A strong engineering team can help you optimize your casting design for manufacturability, performance, and cost-effectiveness. They can also troubleshoot potential issues and ensure the final product meets your performance requirements.
- Manufacturing Capabilities and Facilities: The Tools for Success
The quality of SG iron castings is heavily dependent on the manufacturing facilities and processes employed. A thorough evaluation of the manufacturer’s infrastructure is crucial.
- State-of-the-Art Equipment and Technology: Modern and well-maintained equipment is essential for producing high-quality castings with consistent dimensional accuracy and surface finish. Enquire about the manufacturer’s molding processes (e.g., green sand, no-bake, investment casting), melting furnaces (e.g., induction furnaces), pouring systems, and finishing processes (e.g., shot blasting, heat treatment, machining). Advanced technologies like automated molding lines, robotic pouring systems, and CNC machining centers can significantly improve efficiency, quality, and consistency.
- Production Capacity and Scalability: Evaluate the manufacturer’s production capacity to ensure they can meet your current and future volume requirements. Consider their ability to handle both small prototype runs and large-scale production orders. A scalable manufacturing process is crucial for long-term partnerships, allowing you to increase production as your business grows.
- Quality Control and Testing Facilities: A robust quality control system is paramount in SG iron casting manufacturing. Look for manufacturers with certifications like ISO 9001, IATF 16949 (for automotive), or other relevant industry-specific certifications. Enquire about their quality control procedures, including incoming material inspection, in-process checks, and final product testing. Do they have in-house testing facilities or partnerships with accredited labs to perform necessary tests, such as chemical composition analysis, mechanical property testing (e.g., tensile strength, yield strength, hardness), metallographic analysis, and non-destructive testing (NDT) like ultrasonic testing, magnetic particle inspection, or radiographic inspection?
- Material Quality and Testing: Ensuring Integrity
The quality of the raw materials used and the rigorousness of testing procedures directly impact the integrity and performance of the final SG iron castings.
- Sourcing of Raw Materials: Inquire about the source of the raw materials, including pig iron, scrap steel, ferroalloys, and other additives. Reputable manufacturers prioritize high-quality raw materials from trusted suppliers to ensure the consistency and purity of the molten metal. Understanding the origin and quality of the raw materials provides confidence in the final product’s properties.
- Material Composition and Traceability: Ensure the manufacturer can provide detailed material composition reports and traceability information for each batch of castings. This is crucial for verifying that the castings meet the specified material grade and chemical composition requirements.
- Testing and Analysis: Verify that the manufacturer performs appropriate testing and analysis to ensure the castings meet the required mechanical properties, microstructure, and dimensional tolerances. Discuss the types of tests they conduct and the frequency of testing. A comprehensive testing program demonstrates a commitment to quality and helps identify potential defects early in the production process.
- Customization and Design Support: Tailoring to Your Needs
Many applications require custom-designed SG iron castings to meet specific functional and performance requirements.
- Design Assistance and Collaboration: If you require assistance with the design or optimization of your castings, choose a manufacturer with a strong engineering team that can offer valuable input. They should be able to collaborate with you to optimize the casting design for manufacturability, performance, and cost-effectiveness. This includes considering factors like gating and risering systems, solidification modeling, and stress analysis.
- Customization Options and Flexibility: Discuss your specific requirements for size, shape, tolerances, surface finish, and any other unique features. A flexible manufacturer can tailor their processes to meet your individual needs, whether it’s a small batch of prototypes or a large production run of customized castings.
- Cost and Lead Times: Balancing Value and Time
Cost and lead times are important factors in any procurement decision. However, it’s crucial to balance these factors with the overall quality and reliability of the castings.
- Competitive Pricing and Value for Money: Obtain quotes from multiple manufacturers to compare pricing. However, don’t solely focus on the lowest price. Consider the overall value proposition, including the quality of the castings, the manufacturer’s expertise, their production capabilities, and their reputation for reliability. A slightly higher price from a reputable manufacturer might be a better investment in the long run, preventing costly rework or failures due to inferior castings.
- Realistic Lead Times and Delivery Schedules: Discuss lead times and ensure they align with your project schedule. A reliable manufacturer will provide realistic and achievable delivery timelines. Communicate your project deadlines clearly and discuss any potential challenges that might affect delivery. A manufacturer with efficient production planning and inventory management systems can often offer shorter lead times and more reliable delivery schedules.
- Communication and Customer Service: Building a Strong Partnership
Effective communication and responsive customer service are essential for a successful long-term partnership.
- Open and Transparent Communication: Choose a manufacturer who is responsive to your inquiries and provides clear and timely communication throughout the process. They should be willing to answer your questions, provide updates on the production progress, and address any concerns you might have.
- Proactive Problem Solving and Support: Assess the level of customer support offered. A good manufacturer will be proactive in identifying and addressing potential issues. They should be willing to work with you to find solutions and provide technical assistance even after the castings are delivered.
- Industry Reputation and References: Validating Performance
A manufacturer’s reputation in the industry and feedback from previous clients provide valuable insights into their performance and reliability.
- Industry Recognition and Awards: Look for manufacturers with a good reputation in the industry. Check for awards, certifications, and memberships in relevant industry organizations. These can indicate a commitment to quality and best practices.
- Client Testimonials and Case Studies: Ask for references or testimonials from previous clients. Reading case studies or speaking with previous customers can provide valuable insights into their experience with the manufacturer, the quality of castings, and their level of customer service.
Conclusion: Making an Informed Decision
Choosing the right SG iron casting manufacturer is a critical decision that can significantly impact the success of your projects. By carefully considering these factors β experience and expertise, manufacturing capabilities, material quality and testing, customization options, cost and lead times, communication and customer service, and industry reputation β you can find a partner who can deliver high-quality castings that meet your specific requirements and contribute to the success of your business. Don’t hesitate to visit the manufacturer’s facilities, meet their team, and ask detailed questions. A thorough due diligence process will help you make an informed decision and establish a strong, long-term partnership with a reliable and capable SG iron casting manufacturer.
Β
Leave a Reply