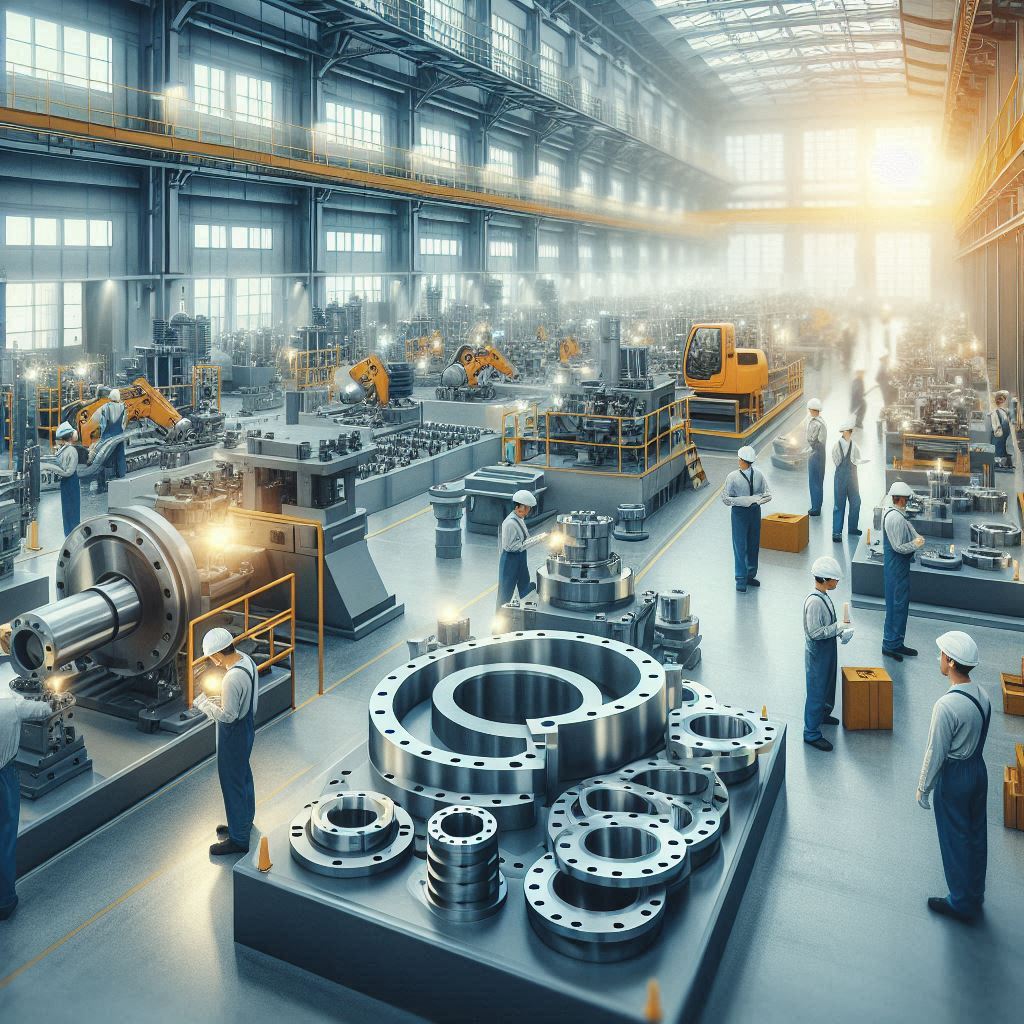
Forged flanges are those readily available and very important where piping systems connect pipes with valves, pumps, or other appurtenances. The correct selection of forged flanges is very important in the structural integrity of piping systems, avoiding leaks, and ensuring compatibility with different kinds of industrial applications. Types, materials, and specifications knowledge provide excellent matching for specific operational requirements. Different forged flanges can read the use parameter variously depending on the pressure rated difference types. Among the most common include:
- Weld Neck Flange (WN): With the long tapered hub, it is the most perfect flange for reinforcement in high-pressure and high-temperature applications.
- Slip-On Flange (SO): Designed with tolerances that give the facility for convenient installation and internal welding; best for all low-to-low-pressure applications requiring immediate assembly.
- Blind Flange (BL): It seals one end of pipe systems, which is for maintainence and pressure-testing.
- Socket Weld Flange (SW): This is best suited for high pressure-low diameter applications having tough and very durable connections.
- Threaded Flange (TH): Contemplating an application of a threaded flange would be in cases where welding may be done but practically unfeasible, and it could provide airtight seal by a screw mechanism.
- Lap Joint Flange (LJ): They are used along with stub ends for easy dismantling and alignment in those systems that frequently need maintenance.
- Orifice Flanges: Apply to those assembly types regarding flow measurement applications that are applicable orifice plates for fluid flow measurement.
Materials Used in Making Forged Flanges
The choice of material will greatly have to do with the way that applied forged flanges will need to be operationally functional over the years of its service life. Material selection may include factors such as operating temperature and pressure and might further include factors such as chemical exposure. Here is the list of materials that constitute an extensive application in forged flanges:
- Carbon Steel: The most generally and widely preferred because of its strength, economy, and the working average at temperature and pressure.
- Stainless Steel: High corrosion resistant, it has a wide application in food processing and pharmaceuticals, as well as in marine conditions.
- Alloy Steel: Alliance of steel flanges renders a considerable amount of strength along with resistive property with the involvement of chromium and molybdenum as the alloying elements.
- Duplex & Super Duplex Steel: Built out of a combination of both austenitic and ferritic stainless steel. Both kinds have excellent strength in addition to resistance to corrosion, intact under extreme conditions.
- Nickel Alloys: Flanges of these make nickel based alloys applicable in high temperature and corrosive environments, typically for chemical processing and especially in aerospace applications.
- Copper Alloys (Brass and Bronze): These materials are known for their corrosion resistance and thermal conductivity, especially for application to marine and heat exchange applications.
Major Specifications to Look For
Selecting forged flange requires consideration of several specifications to make a forged flange most suited for its application:
- Pressure Ratings : Each flange is pressure rated on the basis of ANSI/ASME class (150, 300, 600, 900, 1500, and 2500) for several pressure applications.
- Dimensions: Verify against the applicable standards with respect to flange dimensions such as ASME B16.5, B16.47 or API 6A that will differ from industry to industry.
- Types of Facing: The flange faces used most frequently would be raised face (RF), flat face (FF), and ring-type joint (RTJ), with a different seal between each one.
- Bolt Hole Patterns: The number and arrangement of bolt holes must be the same as the connecting counterparts for secure fit.
- Temperature Resistance: Select strong materials and coatings which are suitable for operation temperature and will not fail with time.
- Compliance with the Industry Standards: These flanges shall conform to all international standards of ASME, ASTM, DIN, EN and also those relating to quality and safety.
Conclusion
However a more sophisticated manner is required in order to appraise type material and specification to be equated with the applications. The selection shall help improve the reliability, safety and effectiveness to be improved in all those high pressure, corrosive chemical processing pipelines of oil and marine applications. Organizations operating in a well-understood way according to production needs and standards are likely to experience quality high efficiency and value in the maintenance of their piping systems.
Leave a Reply