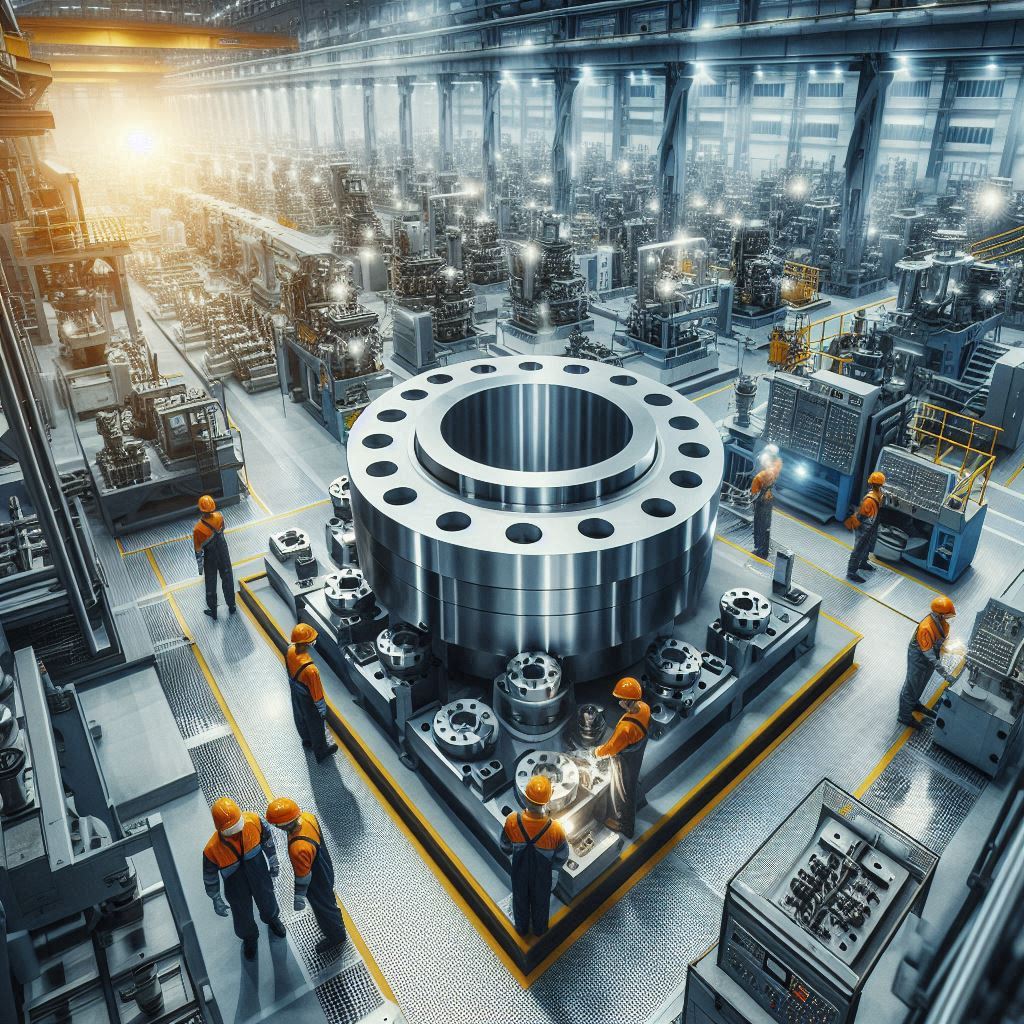
Choosing the right material to forge the flange is one of the most critical decisions taken by a Forged Flanges Manufacturers in the preparation of the manufactured product. Depending on the selected material, the developed flange will exhibit high strength plus durability or ability to perform efficiently in the said application. Forged flanges generally form the link in a piping system required as an essential tool to various pipes, valve assembles, and most equipment. They need resistance to high pressure levels, high temperature, and highly corrosive environments. The selected material guarantees that the flange will operate in an efficient manner and safety for some considerable time. The article here gives a more extensive view of what needs to be checked in terms of forging flange material selection and the common material utilized in flange manufacturing.
1. Application Requirements
The right materials for forged flanges are chosen with a minimal idea of the application requirement in view. Nonetheless, conditions and environments diverge a lot, when one considers industries like oil and gas, petrochemicals, thermal power plant generation, and construction. For example, flanges in power sector high-pressure steam systems have to withstand very high pressures, while those in chemical pipelines have to withstand attack and degradation by corrosive media. Some main factors include pressure rating since it has to be carbon steel or alloy steel when a high-pressure system application is required, temperature resistance meaning it should withstand both high temperature and low temperature, and corrosion resistance where severe environment applicability particularly for marine and chemical processing application calls for either stainless steel or even titanium. This helps the chosen material to ensure that working is done efficiently and in safety within the proposed application.
2. Strength and Toughness of Materials
Forged flanges must possess tensile strength to resist stresses that may apply mechanical loads or outer helper forces. The more a material can withstand such mechanical or physical impacts, unfortunately, the less reliable it becomes because the chance of failure due to deformation, or shear by imparted forces, is the opposite. In this respect, failure will occur. Such failure will critically affect reliability. Carbon steel has often been favored for its strength, toughness, and economy, which are critical for meeting most general application requirements for most low-to-medium pressure systems. Alloys like ASTM A182 F5 and F22 greatly improve strength assets under high-pressure environments, with the F22 being way stronger than carbon steel at elevated temperatures. Stainless Steel alloys 304 and 316 with high corrosion resistance are chosen wherever chemical integrity or moisture processes are a major concern when it comes to impeding the performance of the flange. The right choice of material for tensile strength for a given application will ensure that it fulfills the requirements.
3. Resistance To Corrosion
Corrosion is one of the main causes of flange failure. Every industry exposed to failure by corrosion is dealing with either chemicals, water, or saltwater. So, to counter this possible failure, selection should be made for materials that can resist corrosion-to-an-extent. Some stainless steel grades-304 and 316-take the plaudits here. These are fairly safe in moist conditions exposed to chemicals or seawater, and are all the more so for food processing, pharmaceutical, and marine industries. Nickel-based alloys like Hastelloy and Inconel find applications in other cases requiring extreme resistance to corrosive environment involving wide ranges of aggressive chemicals-acids and alkalis. Titanium has excellent resistance to corrosion, but it is extremely expensive; its application is in highly corrosive service like chlorides or acids, for example, aerospace and chemical processing, where the risk of material failure is very high. The right material keeps the flange lighter on corrosion failure.
4. Cost Factors:
Manufacturing costs for forged flanges also depend on their material. Specialty materials such as titanium or first-grade alloys carry far more cost than carbon steel. Thus, the performance requirement versus price becomes a consideration. In contrast, manufacturers could choose coated or plated carbon steel flanges when a lower price is required, but corrosion resistance is a concern. These alternatives would not get full protection; however, they can provide price and partial protection against corrosion.
5. Welding and Fabrication Compatibility:
After forging, carbon steels and some alloy steels welding is not a big issue but some other materials including stainless alloys, nickel, etc., difficult to weld using conventional techniques might require special approaches or filler metals during welding. In many occasions, those flanges need to be welded after forging towards pipelines or equipment at installation site directly, therefore, the proper materials would need to be more assured that once they are welded provide the strength and integrity and would not be damaged in any way.
6. Industry Standards and Certifications:
Last but not least were the industry standards and certifications taken into consideration when selecting a material to forge flanges. This would also ensure that within the desired limits, the selected alternative must possess the required stringent quality, safety, and performance characteristics, thereby permitting its application in an application. Ordinary industrial standards for forged flanges are ASME (American Society of Mechanical Engineers), ASTM (American Society for Testing and Materials), API (American Petroleum Institute), and above all, the DIN (Deutschers Institute fur Normung). The creamy highlight of this road map is that the flange would work rightly, and once again support the operation’s demands, boasting safety and regulatory requirements that can be assured to protect system integrity.
Leave a Reply