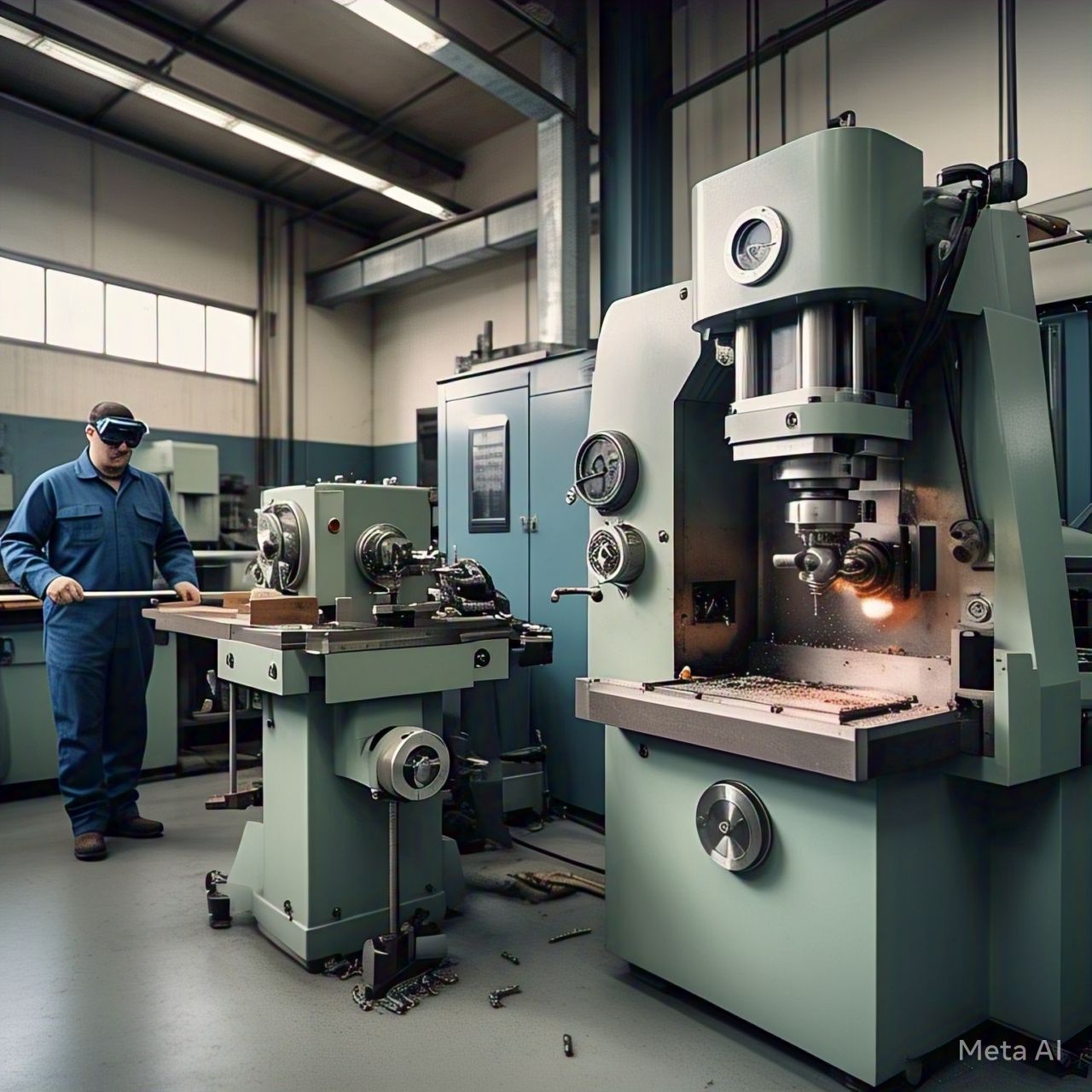
Precision custom machining manufacturers plays a crucial role in modern industries, enabling the production of high-accuracy components tailored to specific requirements. From aerospace to medical devices, precision machining manufacturers provide essential services for businesses that demand tight tolerances, superior quality, and customized solutions.
In this article, we will explore what precision custom machining is, the different types of machining processes, key industries that rely on it, and how to choose the best precision machining manufacturer for your needs.
What is Precision Custom Machining?
Definition
Precision custom machining is the manufacturing process of creating highly accurate parts and components using advanced machining techniques. These parts are often made from metals, plastics, or composites and are used in industries where high tolerances and exact specifications are required.
Why is Precision Machining Important?
- Ensures tight tolerances and high precision
- Reduces material waste through efficient machining techniques
- Enhances product durability and performance
- Allows for customization based on specific engineering needs
Materials Used in Precision Custom Machining
- Metals: Aluminum, Titanium, Stainless Steel, Brass, Copper
- Plastics: ABS, Polycarbonate, PTFE, PEEK
- Composites & Special Alloys: Carbon fiber, Inconel, Hastelloy
Types of Precision Custom Machining Processes
1. CNC Machining (Computer Numerical Control)
CNC machining is the most common precision machining technique. It uses computer-controlled tools to cut, drill, and shape materials with extreme accuracy.
Types of CNC Machining
- CNC Milling β Rotating cutters remove material to shape a workpiece.
- CNC Turning (Lathe Machining) β A rotating workpiece is shaped using cutting tools.
- CNC Grinding β Produces smooth, fine finishes with extreme precision.
2. Electrical Discharge Machining (EDM)
EDM uses electrical discharges (sparks) to shape hard metals that are difficult to machine using traditional methods.
3. Laser Cutting & Waterjet Cutting
- Laser Cutting: Uses a high-powered laser for fine, detailed cuts.
- Waterjet Cutting: Uses high-pressure water mixed with abrasives to cut thick and heat-sensitive materials.
4. Swiss Machining
Swiss machining is ideal for high-precision small parts, commonly used in medical and aerospace applications.
Industries That Rely on Precision Custom Machining
1. Aerospace & Defense
- Aircraft components β Engine parts, landing gear, brackets
- Satellite & space technology β Lightweight, high-strength custom parts
2. Automotive & Motorsports
- Custom engine components β Pistons, crankshafts, turbo parts
- Performance-enhancing modifications β Racing-grade precision parts
3. Medical & Healthcare
- Surgical instruments β Scalpels, forceps, implants
- Prosthetics & orthopedic devices β Custom-made bone plates, screws
4. Electronics & Semiconductor Industry
- Precision micro-components β Circuit boards, heat sinks, housings
- Miniaturized parts β Used in microchips and medical devices
5. Industrial Equipment & Automation
- Robotic system components β High-precision gears, arms, actuators
- Manufacturing machinery β Custom CNC parts for assembly lines
Manufacturing customer service
Manufacturing customer service focuses on providing support to clients by addressing product inquiries, order issues, and technical concerns. It ensures smooth communication between manufacturers and customers, helping resolve complaints, track shipments, and offer after-sales assistance. A strong customer service team enhances customer satisfaction, builds trust, and strengthens long-term business relationships.
Advantages of Working with Precision Custom Machining Manufacturers
1. High-Accuracy Components
Precision machining ensures extremely tight tolerancesβsometimes within Β±0.001mmβfor high-performance applications.
2. Customization for Unique Applications
Manufacturers offer tailor-made solutions for specific industries, allowing businesses to develop custom parts that meet exact design specifications.
3. Scalability for Production Needs
Manufacturers can produce prototypes, small-batch, or large-scale production runs, depending on project requirements.
4. Cost-Effective Manufacturing
Precision machining reduces material waste, improves efficiency, and lowers production costs in the long run.
5. Quality Assurance & Compliance
Leading manufacturers adhere to ISO 9001, AS9100, and other quality certifications to ensure components meet industry standards.
How to Choose the Best Precision Custom Machining Manufacturer
1. Industry Expertise & Experience
Look for manufacturers with experience in your specific industry, whether it’s aerospace, medical, or automotive.
2. Machining Capabilities & Technology
A reputable manufacturer should have CNC machines, EDM, grinding, and laser cutting capabilities to meet diverse machining needs.
3. Material Selection & Customization
Check if the manufacturer can work with specialized metals, plastics, and composite materials.
4. Quality Control & Certifications
Ensure the company meets ISO 9001, AS9100, or FDA compliance for regulated industries.
5. Production Capacity & Lead Times
Choose a manufacturer that can handle your order volume and delivery timelines efficiently.
6. Customer Support & Engineering Assistance
A good manufacturer offers technical support, design optimization, and post-production services to improve product performance.
Future Trends in Precision Custom Machining
1. AI-Driven Machining & Automation
AI-powered machining improves speed, accuracy, and efficiency, reducing human errors.
2. 3D Printing & Hybrid Manufacturing
Combining CNC machining with 3D printing allows for rapid prototyping and complex geometries.
3. IoT & Smart Factories
Sensors and real-time monitoring improve machine efficiency and predictive maintenance.
4. Sustainable & Eco-Friendly Machining
Manufacturers are adopting recyclable materials, energy-efficient processes, and waste reduction techniques.
Conclusion
Precision custom machining manufacturers play a critical role in delivering high-quality, custom-engineered components for industries requiring extreme accuracy and reliability. Whether you’re in aerospace, medical, automotive, or electronics, choosing the right precision machining partner can enhance your production efficiency and product performance.
By leveraging advanced CNC precision machining, Swiss turning, laser cutting, and EDM technology, businesses can achieve superior precision, customization, and long-term cost savings.
If you’re looking for a precision custom machining manufacturer, consider experience, technology, certifications, and production capacity to ensure the best results for your project.
FAQs
1. What is the difference between CNC machining and Swiss machining?
CNC machining is used for general precision components, while Swiss machining is ideal for small, intricate, high-precision parts commonly used in medical and aerospace applications.
2. What industries require precision custom machining?
Industries such as aerospace, automotive, medical, electronics, and industrial automation rely on precision machining for high-accuracy components.
3. What are the tolerances in precision machining?
Precision machining can achieve tolerances as tight as Β±0.001mm, depending on the manufacturing process and materials used.
4. How do I choose the right material for precision machining?
Material selection depends on strength, durability, weight, heat resistance, and industry standards. Common choices include stainless steel, aluminum, titanium, and high-performance plastics.
5. Can precision machining be used for prototyping?
Yes, precision machining is commonly used for rapid prototyping to test and refine product designs before full-scale production.
6. What is the cost of precision custom machining?
Costs depend on material, design complexity, tolerances, and order volume, but precision machining offers long-term cost savings through material efficiency and quality.
7. How long does it take to manufacture a precision-machined part?
Lead times vary based on complexity, material availability, and production volume. Simple parts may take a few days to a week, while complex components requiring multiple machining processes may take several weeks.
8. What quality certifications should a precision machining manufacturer have?
Look for certifications like:
- ISO 9001 β General quality management standard
- AS9100 β Aerospace industry standard
- ISO 13485 β Medical device manufacturing certification
- IATF 16949 β Automotive industry standard
9. Can precision machining be automated for mass production?
Yes, automated CNC machining centers allow for high-volume production of precision components with consistent accuracy, making it a cost-effective option for large-scale industrial applications.
10. How do I choose the right precision machining manufacturer?
Consider the following factors:
- Industry expertise β Choose a manufacturer experienced in your sector.
- Technology & capabilities β Ensure they have advanced CNC, EDM, laser cutting, and grinding machines.
- Material expertise β Check if they can work with the materials required for your project.
- Certifications & compliance β Look for ISO, AS, or other industry-specific standards.
- Production capacity β Ensure they can handle your order volume and timelines.
- Customer support β A good manufacturer provides engineering assistance, quality assurance, and after-sales support.
Leave a Reply