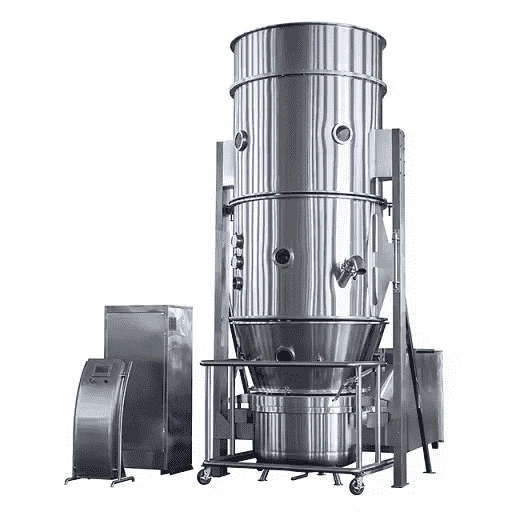
A fluid bed dryer is an essential piece of equipment in many industries, including pharmaceuticals, food processing, and chemical manufacturing. It provides efficient drying of powders, granules, and other particulate materials by using a controlled flow of heated air. Selecting the right fluid bed dryer for your production needs requires careful consideration of several factors, such as capacity, material properties, energy efficiency, and regulatory compliance. This article explores key aspects to help you make an informed decision.
Understanding the Basics of a Fluid Bed Dryer
A fluid bed dryer operates by suspending solid particles in a stream of hot air, causing them to behave like a fluid. This process enhances heat and mass transfer, leading to rapid and uniform drying. The drying process occurs in a specially designed chamber where airflow and temperature are controlled to achieve optimal moisture removal without damaging the material.
There are two primary types of fluid bed dryers: batch and continuous. Batch fluid bed dryers process materials in discrete loads, making them ideal for smaller production volumes and applications requiring frequent product changes. Continuous fluid bed dryers, on the other hand, are better suited for large-scale production, offering consistent throughput and efficiency.
Key Factors to Consider When Selecting a Fluid Bed Dryer
1. Material Characteristics
Understanding the physical and chemical properties of the material to be dried is crucial. Factors such as particle size, moisture content, density, and thermal sensitivity influence the choice of dryer. Some materials may require specialized fluidization techniques to prevent issues like agglomeration or degradation. Conducting material tests before purchasing a fluid bed dryer ensures compatibility with the intended application.
2. Production Capacity
Selecting a dryer that matches your production volume is essential for efficiency and cost-effectiveness. Batch fluid bed dryers are suitable for small to medium-scale operations, while continuous fluid bed dryers are ideal for high-throughput manufacturing. It is advisable to choose a dryer with a slightly higher capacity than your current needs to accommodate future production growth.
3. Energy Efficiency and Operating Costs
Energy consumption is a significant factor in choosing a fluid bed dryer. Look for models equipped with energy-saving features such as heat recovery systems, variable frequency drives (VFDs), and advanced airflow controls. Investing in an energy-efficient dryer can reduce operational costs and improve overall sustainability.
4. Drying Performance and Uniformity
A high-quality fluid bed dryer should provide uniform drying across all particles. Uneven drying can lead to product inconsistencies and reduced quality. Advanced drying technologies, such as multi-zone drying chambers and precision airflow distribution, enhance drying uniformity and prevent overheating or under-drying.
5. Customization and Flexibility
Production requirements can vary significantly across different industries. A customizable fluid bed dryer allows for adjustments in airflow, temperature, and residence time to meet specific drying needs. Features like interchangeable drying chambers and modular designs provide flexibility for future modifications.
6. Regulatory Compliance
Industries such as pharmaceuticals and food processing have stringent regulatory requirements regarding product safety and hygiene. Ensure that the chosen fluid bed dryer complies with relevant industry standards, such as Good Manufacturing Practices (GMP), FDA regulations, and CE certifications. Hygienic designs with easy-to-clean components help maintain compliance and prevent contamination.
7. Automation and Control Systems
Modern fluid bed dryers come equipped with advanced automation and control systems that enhance efficiency and ease of operation. Features such as programmable logic controllers (PLCs), touchscreen interfaces, and real-time monitoring improve process control and reduce human intervention. Automated drying systems also enhance reproducibility, ensuring consistent product quality.
8. Maintenance and Durability
The longevity and reliability of a fluid bed dryer depend on its build quality and maintenance requirements. Choose a model with robust construction and minimal wear-prone parts to reduce downtime and repair costs. Features like quick-access panels, self-cleaning filters, and modular components facilitate easier maintenance and prolong equipment lifespan.
Choosing Between Batch and Continuous Fluid Bed Dryers
Selecting between batch and continuous fluid bed dryers depends on production needs and operational requirements.
-
Batch Fluid Bed Dryer: Ideal for applications requiring flexibility, small production batches, or frequent product changeovers. It allows better control over drying parameters for specialized materials.
-
Continuous Fluid Bed Dryer: Suitable for high-volume production where consistent output is necessary. It offers efficient energy use and uniform drying, making it the preferred choice for large-scale operations.
Common Applications of Fluid Bed Dryers
Fluid bed dryers are widely used across various industries:
-
Pharmaceuticals: Drying granules for tablet formulation, improving powder flow properties.
-
Food Processing: Removing moisture from food ingredients such as coffee, spices, and milk powder.
-
Chemicals: Drying detergents, fertilizers, and catalysts.
-
Minerals and Metals: Processing powders and granules for industrial applications.
Optimizing the Performance of Your Fluid Bed Dryer
To maximize the efficiency and lifespan of your fluid bed dryer, consider the following best practices:
-
Regular Calibration: Ensure that temperature and airflow sensors are regularly calibrated to maintain accurate drying conditions.
-
Proper Loading: Avoid overloading the drying chamber, as it can lead to uneven drying and reduced efficiency.
-
Routine Maintenance: Schedule preventive maintenance to clean filters, inspect wear parts, and check airflow distribution.
-
Process Optimization: Monitor and adjust drying parameters based on real-time data to improve performance and reduce energy consumption.
Conclusion
Choosing the right fluid bed dryer for your production needs involves evaluating several critical factors, including material properties, production capacity, energy efficiency, and compliance with industry regulations. Whether opting for a batch or continuous system, selecting a well-designed and properly maintained fluid bed dryer ensures optimal drying performance, cost savings, and consistent product quality. By understanding your specific requirements and exploring available options, you can invest in a drying solution that enhances productivity and meets long-term manufacturing goals.
Leave a Reply