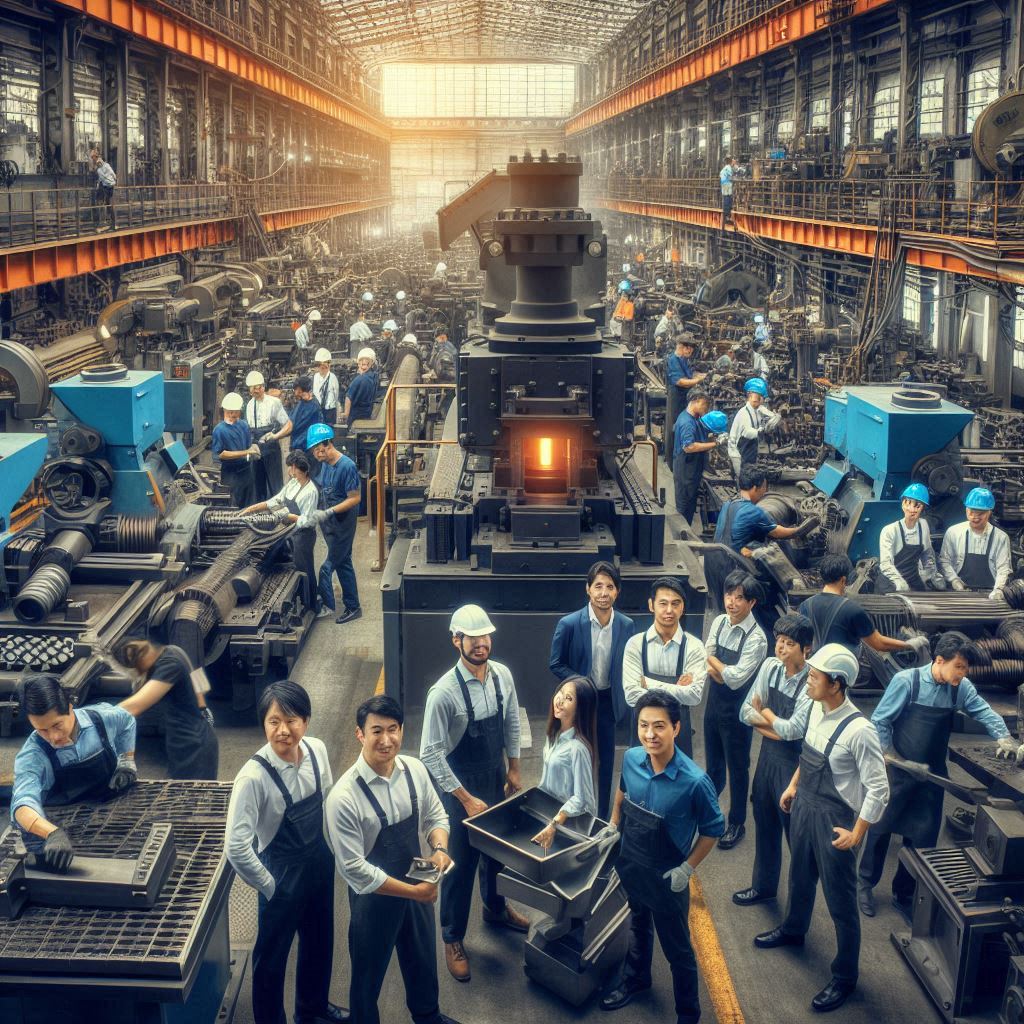
Steel forging suppliers help to meet industrial demands for forged components, which are tough, high performance, and have higher tensile strength. Industries continue to evolve, and the demands grow higher for precision and reliability. Only then can the steel forging suppliers create innovations and shape the future of manufacturing. It is these suppliers, by providing quality, cost-effective, and custom-forged steel components, who enable producers to create in response to modern-day production demands while upholding strict regulatory standards and sustainability practices. The article will concentrate on how steel forging suppliers are shaping the future of industrial manufacturing and thus continuing its evolution.
Innovation at the Leading Edge of Manufacturing Improvement
Steel forging supplier is at the very heart of innovation in the manufacturing environment. With the development of automation, robotics, and 3D modeling, forging technology is being advanced, resulting in the production of highly accurate and complex forged parts. Design flexibility, cost-effective production, and a fast turnaround of parts have been achieved with these systems. An example is the forging of parts assisted with CNC machines and die simulation software that work in tandem to aid manufacture in an efficient way and with maximum accuracy. Further development of these technologies enables these manufacturers to produce complex and high-quality steel for all applications across the automotive, aerospace, medical device, and energy sectors.
The other facet of this is that there is a synergy of additive manufacturing or 3D-printing being used with traditional forging. This has opened the door for complex geometries that couldn’t have been achieved earlier. In this respect, steel forging suppliers are in the move to seek new technologies as far as increased complex client requirements are concerned. The integration of high-end tools and techniques enhances the quality of a product; at the same time, however, it demands new standards of performance, efficiency, and cost-effectiveness to usher in the future of industrial manufacturing.
Strength, Durability, and Precise Workmanship Offered by Steel Forgings
Strength, durability, and precise workability characterize steel forgings. Steel forging suppliers serve different industries, including automotive, aerospace, energy, and defense sectors that demand especially aggressive and hard components. The basic attributes of forged steel that can withstand the highest stresses and endure the most hostile working environments make it suitable for critical applications. Steel forging suppliers have the raw materials and the craftsmanship to ensure these parts stay with their integrity, even under the most extreme operating conditions.
Steel forging, therefore, serves the automobile with critical products such as engine parts, crankshafts, and connecting rods that have to work with extremely high pressure and elevated temperature. Also, engineering components such as turbine blades, landing gear, and other structural components must meet stringent safety requirements; steel forgings serve aeronautics as an important component in this area. Steel forging suppliers now find themselves on the front line in producing goods that empower innovation in these applicable sectors owing to increasing demands for better and more reliable products.
Forging Sustainability and Green Citizenship
Forging suppliers must abide by world standards and guidelines for the environment in ways that reduce industrial wastes which would leave carbon footprints and have devastating effects on ecology or life system in biosphere. Established forging plants utilize energy-efficient and carbon-friendly technologies in its operations. Old methods, for example, are replaced with induction heating, which is more environmentally friendly. Most steel forging suppliers are now looking ahead to establishing programs where scrap metals from forging get recycled back into resource recovery, thus providing greener manufacturing of relevant products at lesser costs.
The underlying reason for all these happenings was occasioned by the regulations and a significant demand from the customers for green product supplies in the related firms. Suppliers are finding that, as a result, they must adopt rigorous self-regulation with regard to the environment and best practices concerning resource utilization. Therefore, industrial manufacturers will, in turn, be assisted in making their supply chains sustainable and products in line with increasing environmental standards. This facet of sustainability will also have an impact on steel forging in the future and define its place in the larger manufacturing landscape.
Flexibility of the Global Supply Chain
Another noteworthy factor of determining the future industrial manufacturing is acquiring the potential for flexible global supply chains. Steel forging suppliers thereby play an important role providing industrial manufacturers proper components to deliver on their promise for global operations. With more global trading and further integration of the supplier chains, the steel forging supplier have to cater to their needs of the manufacturers around the world. This entails that forged parts have to be duly delivered on time and international standards, all at a cost-effective price.
In response to this new environment, steel forging suppliers are developing a reputation for better customer service, shorter lead times, and production schedules that offer much more flexibility.
Leave a Reply