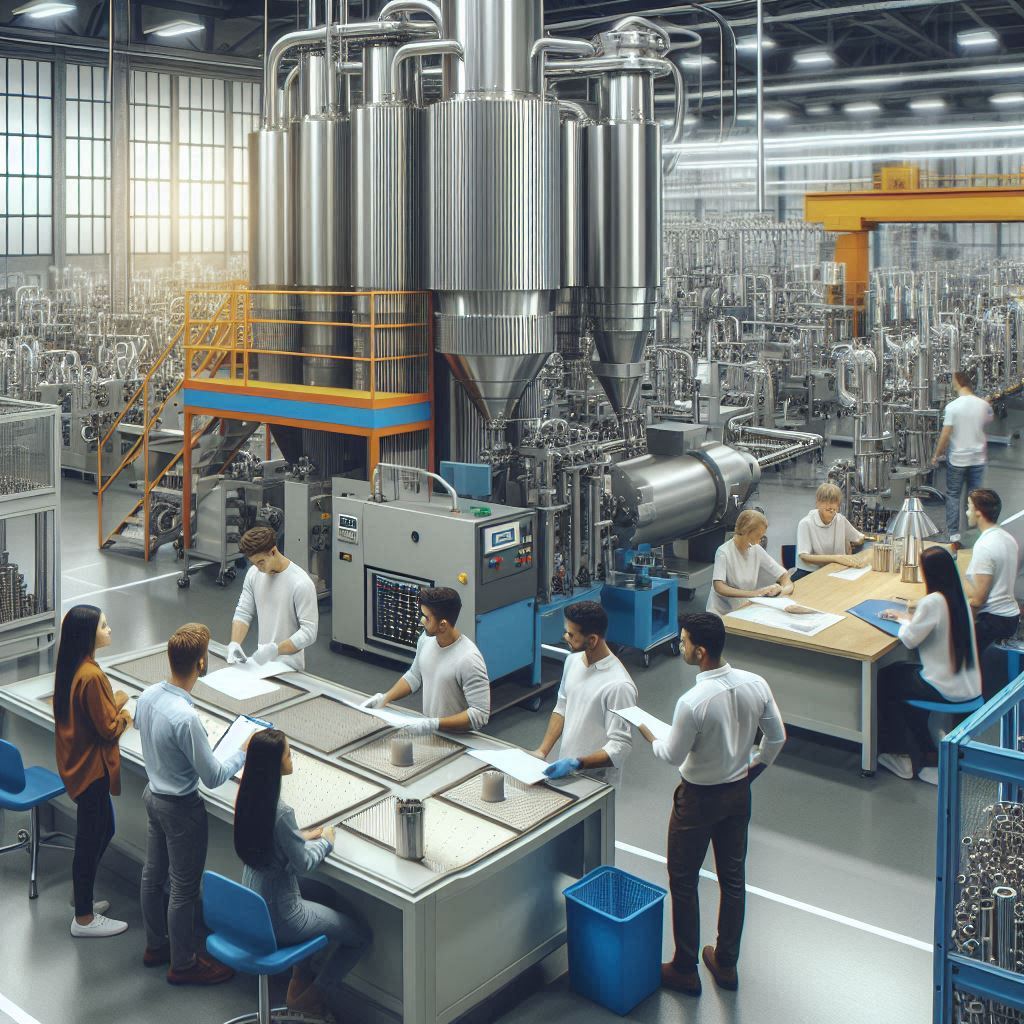
Selecting a expansion bellows manufacturer as the qualification for maintaining skillful operational performance in acoustic arrangements within the necessary system parameters on a case basis. This must include looking into the manufacturer’s experience and expertise with high-quality manufacturing of custom applications-whether for high-temperature bellows, high-pressure bellows, or corrosive-type bellows. Ensure compliance to industry standards like ASME, EJMA, or ISO to ascertain quality assurance. Assess the materials of construction employed since good metals or elastomers play a role in performance and durability. The manufacturer must have capabilities for customizing or adapting their solutions to fit your unique operational requirements. Finally, good customer support service and after-sale services may guarantee success during installation, troubleshooting, and maintenance. The above-mentioned will go a long way to winning you from your very exposed expansion bellows manufacturer, which expects to serve well in the purposes of your system while ensuring optimum performance.
Top Factors to Consider When Selecting an Expansion Bellows Manufacturer
When selecting the appropriate Expansion bellows manufacturer, there will include several important factors that would really come to mind in determining the most suitable for the said individual needs. First, ascertain the relevant experience and reputation of the manufacturer; a trustworthy outfit with solid years of proven presence in the industry is usually the one that comes through with reliability and good quality. Further, ensure such company is compliant with all the necessary industry standards such as ASME, ISO, or EJMA. This is because getting certified by one of these bodies ought to mean their commitment to quality and safety. These materials are equally important in producing a proper flow; emphasis should mainly be offered to superior grade metals like stainless steel and long-lasting elastomers, allowing the operation of the bellows at extreme temperatures, high pressures, and corrosive environments. Furthermore, also take into account the potential for customization of the manufacturer, for a lot of systems may need custom solutions for their conditions of operations. It could also be worth taking a look, just as important, into their quality control program, including tests and inspections, for product performance. Check into after-sale support availability, as well as warranties that could basically cover that maintenance plan and service for coming into action should anything go wrong post-installation, finally.
The Role of Expansion Bellows in Industrial Applications
Essentially, expansion bellows can act as stopgap measures for thermal expansion, vibration, and movements in the pipe and equipment applications found over different industries. These elastic components take up thermal expansion and contraction and reduce stress in the piping system to avoid any potential damage or failure. These situations are seen in oil and gas, power, chemical processing, and HVAC industries. Thus, expansion bellows preserve the piping systems’ integrity, enabling them to operate safely and effectively under varying condition parameters. Expansion bellows improve the longevity of motive systems, cut down maintenance costs, and are higher in performance.
Also, expansion bellows are made to face specific environmental conditions like high pressure, corrosivity, or temperature extremes, thus being part of modern industrial infrastructure.
How Expansion Bellows Manufacturers Ensure Quality and Durability
Quality and durability in expansion bellows come from stringent selection processes in sourcing the materials, accurately controlled manufacturing processes, and thorough testing procedures. These materials, for example, stainless steels, alloy steel, and elastomers, are chosen for their ability to withstand very high temperatures and pressures, and corrosive environments, among others. Precision in design with minimal defects to maximize performance-latest technologies themselves including automated welding, CNC machining, and hydroforming are employed. Additionally, the bellows are subjected to thorough quality control inspections, validating NDT, internal pressure testing, and fatigue testing, all in the quest of ensuring operational loads. It is a further guarantee that the products comply with the global quality standards by manufacturing them according to the respective guidelines of ASME, EJMA, and ISO. Manufacturers are constantly innovating, and the customization made for specific industrial needs helps ensure durability and reliability under super challenging conditions.
Leave a Reply