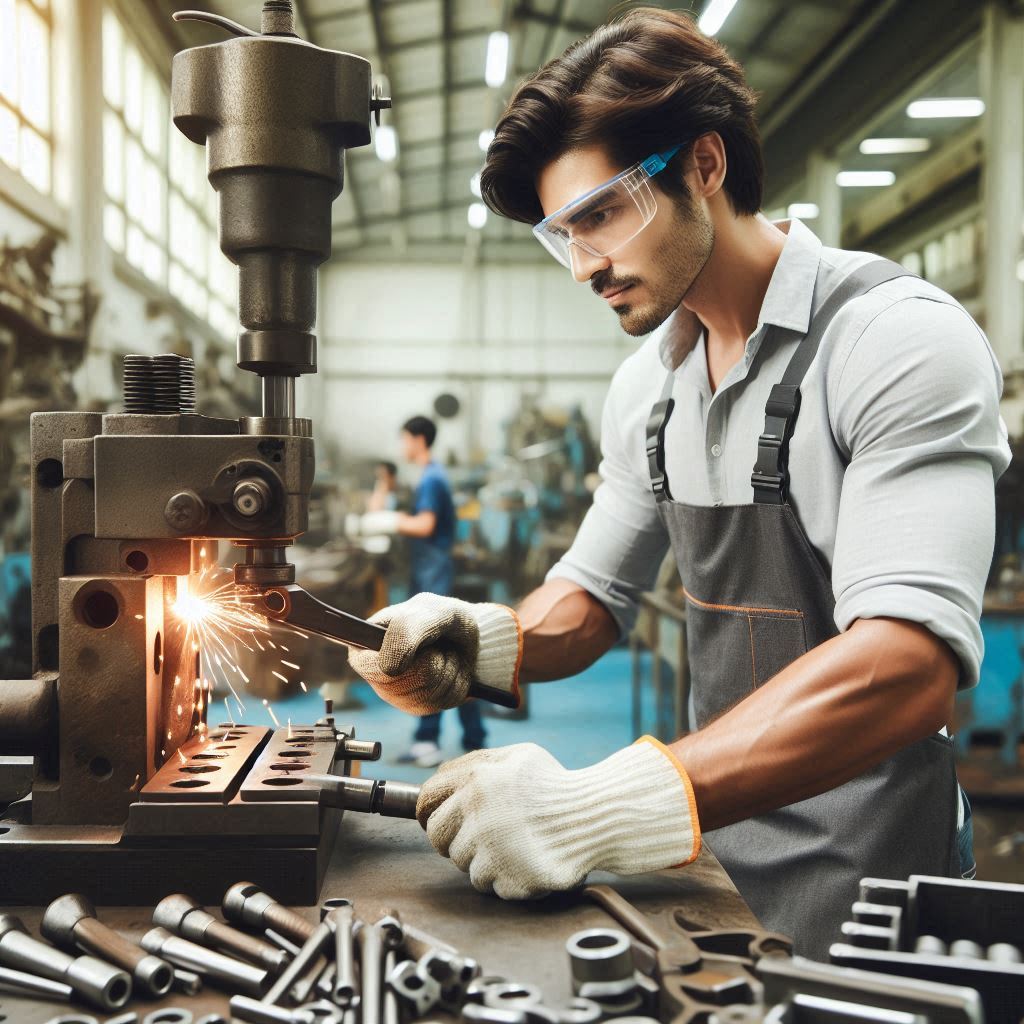
The forging process is when a metal is subjected to stress at high temperature and pressure to develop a grain structure that imparts strength, toughness, and resistance to impact. The main methods: open-die forging for larger and simple shapes; closed-die forging for high-volume production of more intricate parts; cold forging for higher precision at room temperature; hot forging for higher ductility. With the completed forging process, these parts are made strong and tough enough, while machining gets them to finer tolerances and surface finish.
On the other hand, these processes machining by which the created parts are to desired shape dimensions and functional surfaces finishing. The conventional processes here would be turning, which function for cylindrical surfaces, while milling would be used for more complex geometries, drilling, and boring for making holes and cavities, and grinding would be used for surface finishing purposes. In order to keep the levels of the required precision, repeatability, and efficiency high for executions for industrial applications, up-to-date CNC machining has been enormously sustained.
Advantages of Forging Machining
Forging machining has certain additional design advantages; these advantages can be found to be growing in quite a few sectors of manufacturing. In essence, forging-built grain flow adds strength and further augment durability by eliminating any internal defects. On the other hand, machining provides the equal dimensional stability required in making high-performance applications like automotive engines and aircraft parts. In the cost-benefit scenario, the defects that form during the forging process are minimized, while machining reduces finishing aspects, thus making the process effective in high production with less scrap. Moreover, machining provides better surface finish, which gives component value for attractiveness, wear resistance, and functionality. This high versatility of forgings applied for machining works gives a multiplied value to areas like automotive, aerospace, oil & engines, and heavy machinery. Crankshafts, turbine blades, valve bodies, and hydraulic cylinders are examples of components that demand such considerations of notorious high strength, precision, and durability.
Closing Remarks
Forging machining is a suspect process, fast, and unobtrusive in the manufacture. It thus gets composite strength from forging and a hint of variability from machining along the way. It improves the mechanical properties and minimizes the waste of raw material with the surfacing of good quality for the first items. Therefore, with the requirements of component in industry for strength, precision, and cost-efficiency, forging with machining definitely finds itself still amidst the most accepted variables in present-day manufacturing.
Leave a Reply