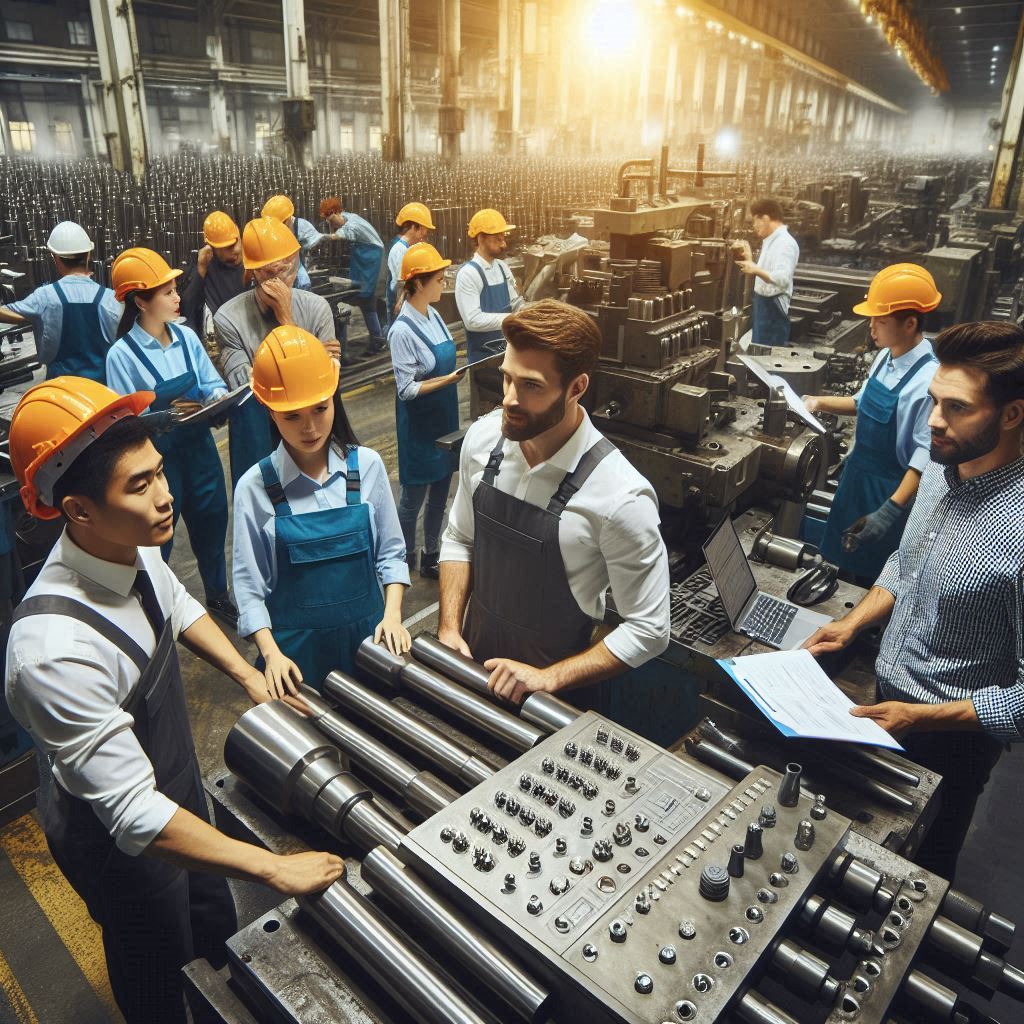
Forged shafts are mechanical parts produced using the forging process in which metal is heated and deformed under high pressure in order to achieve a high degree of strength and durability. Besides, forging process also cleanses grain structure of the metal enhancing mechanical properties such as toughness, fatigue resistance, and impact strength. Forged shafts are produced from carbon steel, alloy steel, stainless steel, or titanium depending on application needs. They are designed to be employed in a host of industries where high performance in rotation relative to power transmission and load-carrying ability is needed.
Which applications can benefit from forged shafts?
The application areas for forged shafts include, but are not limited to, Automotive, which includes crankshafts, camshafts, transmission shafts, all of which bear a relationship to engine performance; Rigidity and resistance to fatigue are some other important characteristics of forged parts intended for use in proximity to aircraft engines and landing gear. Forged shafts find their application mainly in the automotive sector but also in sectors such as aerospace, power generation, heavy machinery, shipping, and oil and gas. In the domain of power, turbines would employ such forged shafts, as would generators; marine ships would employ forgings in rudder and propeller shafts. Other industrial machinery such as rolling mills, hydraulic presses, or railway locomotives would require such forged shafts in terms of operational efficiency and life expectancy, respectively.
What is basic working principle of forged shaft?
The fundamental operating concept of forged shafts is that they are elements of mechanical devices utilized to pass on torque, motion, or load. Whenever these radial or axial forces are applied on the shaft, it passes or shifts power to a component from another, and everything is accomplished under the condition of maintaining the structure intact. Once forged, the component will be able to bear heavy load, extremely high temperature, or even alternating stresses without fracture. Depending on usage, such forged shafts might have keyways, splines, or threads for an effective joining to other mechanical parts. Their enhanced strength and accuracy make them essential in high-performance engineering applications.
Role of Forged Shaft Manufacturer in automobile and aviation industry
The contribution made by Forged Shaft Manufacturer in automotive and aerospace industry is not excluded in producing high-strength precision-engineered shafts necessary for efficient performance as well as safety in such systems. In the automotive sector, these manufacturers would supply the crankshafts, camshafts, and transmission shafts that energize such engines. In such transmissions, these shafts need to function properly under high stress conditions in the long term. Winner of countless products casting its vote in Favor of airworthiness in the manufacture of any aircraft engine shafts, landing gear components, and rotor shafts able to withstand high temperature and high rotational speeds, with very high safety factors, these forgings and their application provide a high-victory margin on safety. The effective application of putative advanced forging technologies with quality control and material selection will deliver performance efficiency, serviceability, and safety of the entire aerospace and automobile.
How Forged Shaft suppliers ensure better logistics and avoid delay in product delivery?
Suppliers of forged shafts provide improved logistics and avoid product delivery delays by using effective supply chain management, strategic warehousing, and real-time tracking integrated systems. They have a well-organized inventory management system to prevent stockouts and ensure instant dispatch on orders. They align those with trusted transport networks and apply sophisticated logistics planning software to maximize route efficiency, minimize transit time, and avoid probable delays. Most suppliers pursue Just-in-Time (JIT) manufacturing to achieve fast replenishment and respond readily to customer demands. In addition, a strict quality control process reduces probable rework or rejection. Thus, only excellent forged shafts find their way to the customers within time, enhancing overall customer satisfaction and reliability.
Quality control measures Forged Shaft exporters need to assure for fair trade compliance
Adopt extremely stringent quality control procedures compiled with forged shaft exporters to meet trade fair requirements and global standards. This includes the supply of raw materials which are certified, metallurgical inspection, and other NDT techniques like ultrasonic, magnetic particle and radiographic testing to identify internal defects. Requirements according to ISO, ASTM, and DIN standards would also have to be met for strength consistency, dimensional accuracy, and endurance. Good traceability of documents and third-party certificates are deemed essential for regulations in international market environments. Now quality assurance converters could increase reliability on the products and prevent trade disputes, and establish trust with foreign buyers. Understanding Forged Shaft manufacturing process
Forging manufacturing of a shaft process includes pivotal steps related to strength, strength, and also precision-related factors.
This begins with material choice, where good-quality carbon steel, alloy steel, or stainless steel are used based on application requirements. The metal is then currently heated to some temperatures to make it malleable, and subsequently, under pressure, is melded through hammers or presses to forge it really high. That process provides mechanical improvement alongside improvement in grain structure. The shaft will later be made hard and tough by heat treatment processes such as quenching and tempering. The operations that give a finished product include dimensional accuracy in turning, grinding, and polishing while creating surface smooth satin finishes. Moreover, it includes on-site ultrasonic testing and hardness testing to ensure that the shafts have been processed satisfactorily for critical applications under industry specifications.
Leave a Reply