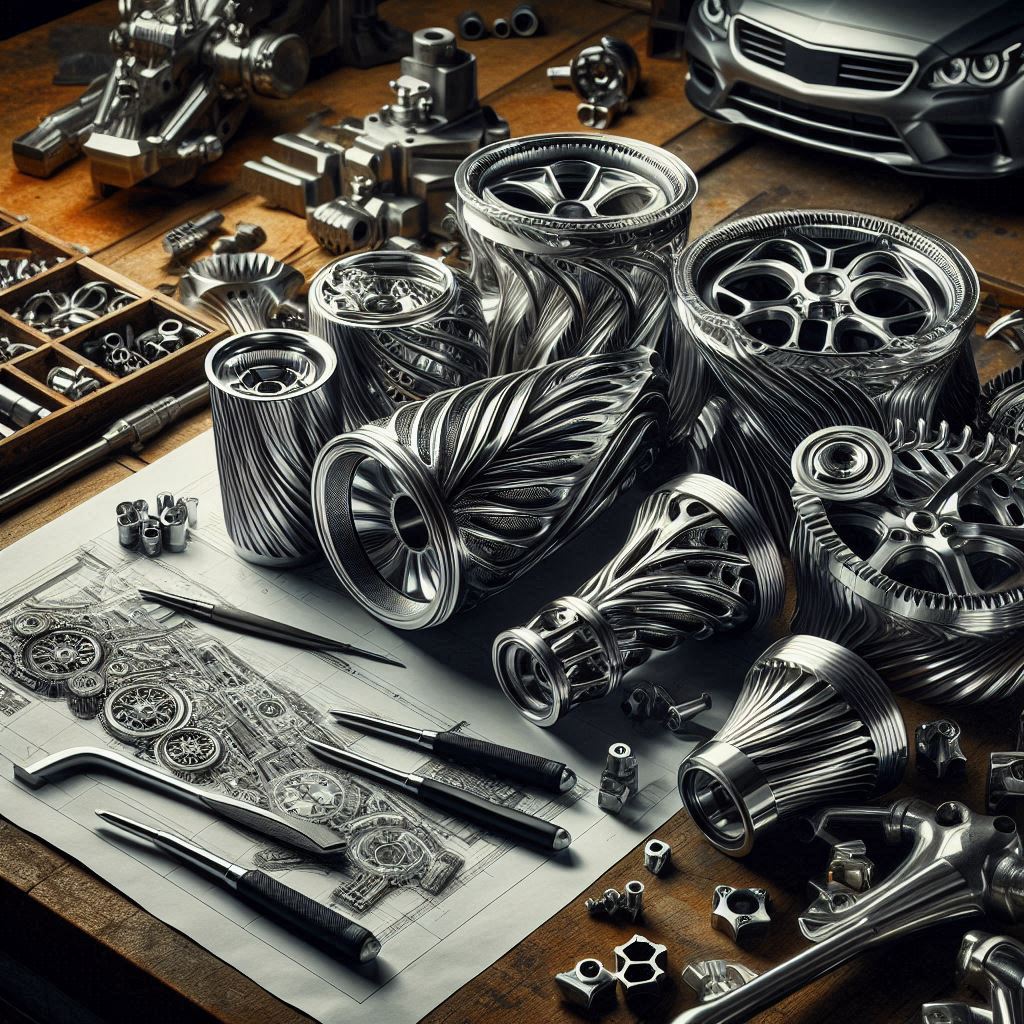
The demand of the automotive industry is always for high performance, high strength and very durable to ensure safety to the consumer, optimal performance and highest efficiency. Indeed, forging is one such trusted process in fabricating critical automotive components since forging improves the mechanical properties of the metals associated with toughness, impact resistance, and fatigue strength. The article focuses on the Types, Advantages, and Applications of forged automotive components presently found in modern automobiles.
Types of Forged Automotive Components
Forged components are very much used at different assemblies of an automobile, especially those requiring high strength and resistance to wearing and load bearing. Most of the common forged automotive parts include:
Indeed, forged components are used all modern engines for strength, durability, and high performance, within the engine and transmission, and within the suspension and braking systems. It converts the back and forth (reciprocating) movement of pistons into a rotating (rotational) force, thus proving to have extreme resistance to fatigue at high speeds. These factors have made forged connecting rods the primary choice for employing them in high-performance and racing engines. A camshaft, which sets the timing of the valves while undergoing enormous pressure loading and friction, is forged for optimal performance and longevity of the component. All the transmission gears, shafts, and differential parts work on the principle of very high wear resistance, which should be obtained for the smooth transmission of power; steering knuckles, control arms, and tie rod ends are the most important ones in vehicle control and shock absorption along the road surface. Forged axles and drive shafts resist torsional stresses and heavy loads to provide better stability and durability. Universal wheel hubs and wheel bearings should give very long service life under extreme conditions since all their weights are carried by the vehicle on them. Most of the braking components such as calipers, rotors, and brackets undergo high temperatures and friction, where forging assists in improving heat dissipation and integrity of the structure for safe and efficient braking performance.
Advantages of Forged Automotive Components
Forged components have significant advantages over cast or machined components. For this reason, they are selected for applications in automobiles. The process of forging refines metal grain and strengthens, impacts-resistance, and durability, all qualities required in high-performance and high-duty vehicles. Superior load-bearing capacity and endurance for extensive pressure and stress are characteristics of forged metals that minimize potential failure rates of forged products and, in turn, ensure more safety and life for vehicles. They also offer the best dissipation of heat and resistance to corrosion, making them suitable for use in high-temperature engine and brake applications. Contemporary forging methods guarantee accuracy and dimensional tolerance, reducing any further need for machining, thus offering a snug fit into intricate assemblies. Though initially more costly, mass automotive production favors forging because of the longer service life and fewer failures, coupled with minimal wastage of raw material, ensuring it will continue to be a pillar for the industry.
Applications of Forged Automotive Components
Forged parts assure strength, durability, and reliability for every segment in the automotive industry using them. Engine, transmission, suspension, and braking systems of passenger cars, for example, are often forged to ensure performance and longevity. Heavy-duty trucks or buses are usually subjected to work nearly below ground level and under heavy loads in occupations that ensure their performance efficiency and safety above that of lighter loads. High-performance and racing cars possess crankshafts, pistons, and connected rods made through forging, which withstand all extremes of stress at high RPMs. Forged axles, transmission gears, and suspension components will still remain significant in the high torque and power management of current electric motors as we face rapid changes with the technology of the future in electric vehicles (EVs). This versatility of application in forging technology indicates the core importance within automotive engineering today.
Conclusion
In terms of vehicle performance, safety, and efficiency, forged automotive components are critical. Strengthening the quality and their enhancing durability and precision have made these invaluable for modern automobile manufacturing. As the automotive culture thinks of involving lightweight components and electric vehicles, forging technology will hold the future in terms of producing top-quality, long-lasting automotive components. Hence, the choice of forged components will make the road all the safer, more trustworthy, and running smoothly.
Leave a Reply