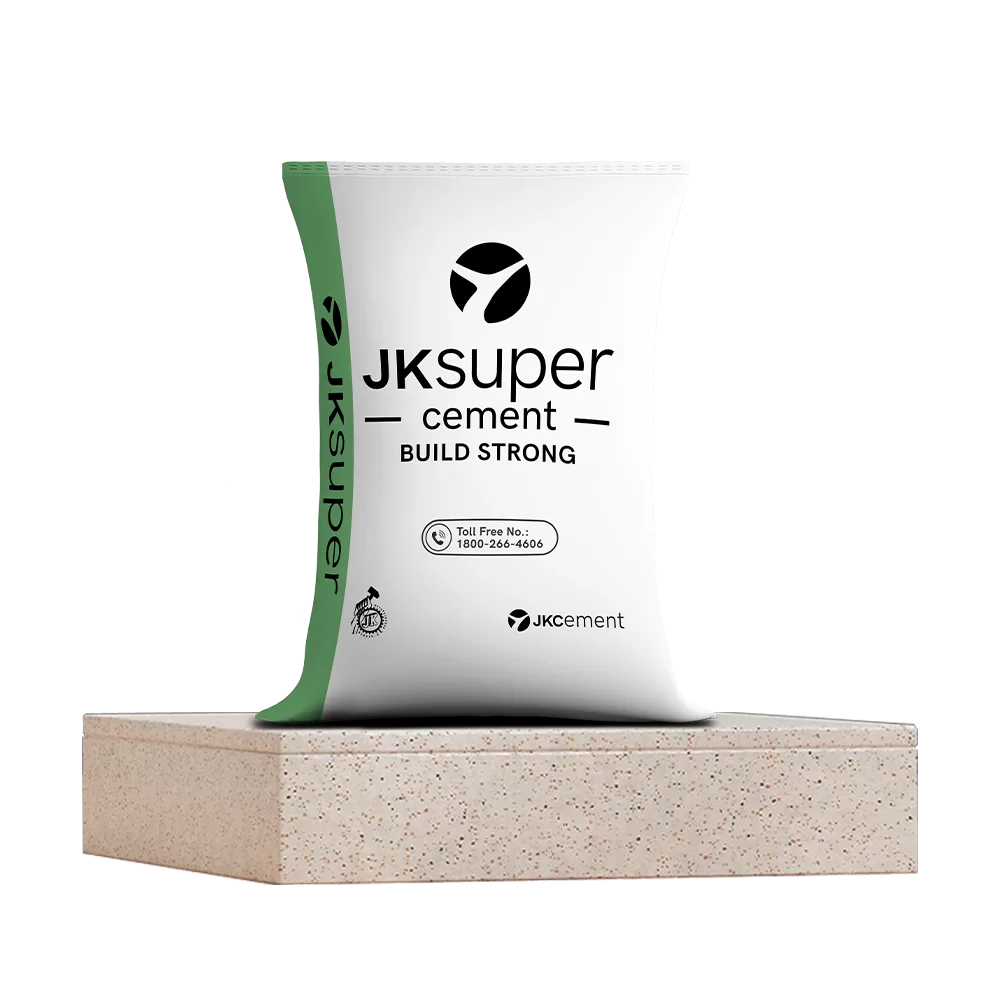
Building a home or commercial structure involves meticulous planning, especially when it comes to budgeting and material selection. Understanding construction cost per square foot, selecting the right cement company, and choosing the appropriate cement type are critical steps. Here is a comprehensive guide to help you navigate these essential aspects of construction.
Estimating construction costs per square foot
The construction cost per square feet varies significantly based on factors like location, materials, labour charges, and design complexity. Breaking it down helps in better budgeting:
- Material costs: Materials, including cement, steel, bricks, and tiles, form a significant part of the expense. Opting for a reliable cement company ensures consistent quality and durability, reducing potential long-term repair costs.
- Labor charges: Skilled and unskilled labour costs depend on the project’s scale and location. Urban areas often have higher labour costs than rural regions.
- Design and finishes: The cost of architectural designs, interiors, and finishes like flooring, painting, and fixtures adds to the overall expense. Modern and luxurious designs typically increase the cost per square foot.
Understanding these components allows for more accurate budgeting and efficient allocation of resources.
Choosing the right cement brand
Selecting a reputable cement company is important for the success of any construction project. High-quality cement contributes to the strength, durability, and longevity of a structure. Consider these points when choosing a supplier:
- Product range: Ensure the company offers various cement grades and types, which are ideal for general construction and masonry work.
- Reputation and reliability: Look for a company with a solid market reputation for quality and timely delivery. Customer reviews and project case studies can provide insights into their reliability.
- Sustainability practices: Companies that follow eco-friendly practices in cement manufacturing can align with modern sustainable construction goals.
Applications of OPC 43 cement
Among the various cement types, OPC 43 cement is a popular choice for its versatility and strength.
- General construction: Suitable for residential and commercial buildings, OPC 43 is commonly used in plastering, flooring, and finishing.
- Structural elements: It provides good compressive strength for columns, beams, and foundations, ensuring structural stability.
- Masonry work: OPC 43 is effective for bricklaying and stone masonry due to its smooth application and binding properties.
Balancing costs and quality
While managing construction costs, do not compromise on quality. Cheaper materials may reduce upfront costs but lead to higher maintenance expenses in the future. Investing in high-grade cement from a reputable cement company ensures long-term savings through reduced repairs and enhanced durability.
Conclusion
Estimating construction costs, selecting a reliable cement company, and using quality materials are key to achieving a successful construction project. A well-planned approach that balances cost and quality ensures your structure is built to last.
Leave a Reply