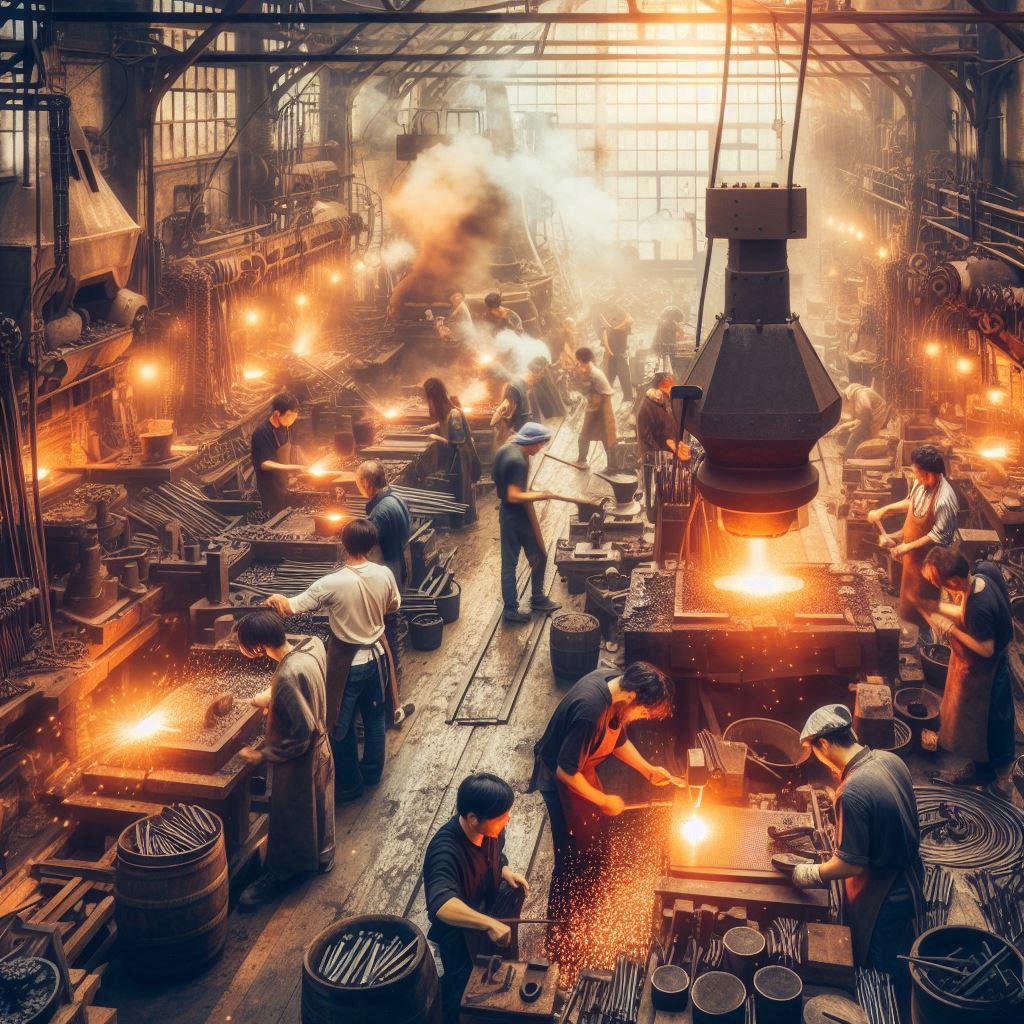
This article analyses the metal forging processes and their advantages. Metal forging is a manufacturing process for shaping metals by controlled application of heat and pressure that results in deformation. The forging process aligns the grain structure of the metal and increases its strength, toughness, and wear resistance capacity. Improved mechanical properties make wrought metals suitable to use where high-stress applications are concerned in the aerospace sector, automotive, or heavy machinery in particular. Therefore, since the forging process will exhibit much lower defects than any other processes, the consistency and reliability of the outcome that is the product, will be substantially higher Forging is a very important processing operation for manufacturing components requiring very high toughness and precision.
How do metal forging suppliers minimize time to market?
Metal forgings suppliers minimize the time to market through optimizing the production processes and efficiency. Advanced technologies, such as CAD and automated machines, are used for the very rapid production of high-quality parts, according to specifications. Normally supplier is maintaining a very huge stock of materials for quick turnaround and also to match with customer demand. Metal forging suppliers have come up with minimizing the rework and speeding up the prototyping phase for a rapid turnaround, which allows the companies to take advantage of fast-moving markets in their different domains such as material selection, tool design, and process optimization.
Tips for selecting the right metal forging suppliers
Among various factors pertinent in selecting suitable suppliers of metal forging are experience, reputation, and types of services provided by the said suppliers. Seek those from suppliers with a proven history of product quality, reliable, and complaisance to specified industry standards. Evaluating should also include their ability to meet your material and volume specifications. Look also for certifications such as ISO 9001 showing the supplier’s commitment to quality control. Communication, dealing with on-time delivery, and adaptability for changes in requirements are other essential traits. In that list, technology capabilities ought to include up-to-date manufacturing processes and equipment.
Leave a Reply