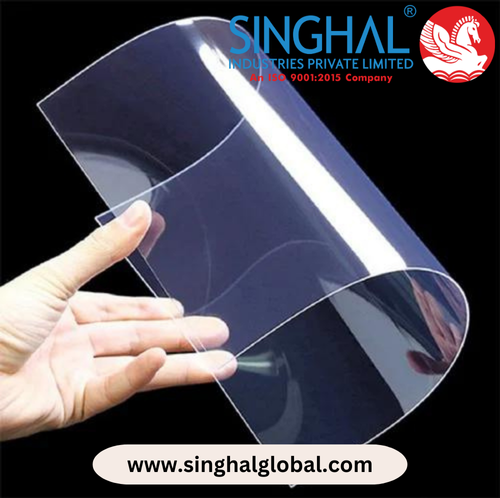
In today’s competitive market, businesses constantly seek innovative ways to improve their product lines, enhance their manufacturing processes, and offer customers high-quality, durable products. One of the most versatile and cost-effective materials used in product manufacturing is plastic. Among the various methods of shaping plastic, vacuum forming stands out as an efficient solution for producing lightweight yet strong products in a wide array of industries. Vacuum forming plastic sheets have revolutionized manufacturing, offering businesses the flexibility to produce complex shapes and designs with minimal waste. In this article, we will explore how vacuum forming plastic sheets can enhance your product line, and we will discuss the role of Vacuum forming plastic sheets manufacturers in India, particularly in Ahmedabad, where a growing number of companies are making their mark.
What Is Vacuum Forming?
Vacuum forming is a process in which a plastic sheet is heated until it becomes soft and pliable. The sheet is then draped over a mold, and a vacuum is applied, pulling the plastic tightly over the mold. Once the plastic cools and hardens, it takes the shape of the mold, creating the desired product. This process is highly suitable for producing large quantities of products with consistent quality, making it ideal for a range of industries including automotive, packaging, consumer goods, medical devices, and more.
Why Choose Vacuum Forming Plastic Sheets?
-
Cost-Effective Production One of the primary reasons businesses choose vacuum forming plastic sheets is the cost-effectiveness of the process. Vacuum forming is a low-cost alternative to traditional injection molding or other complex plastic manufacturing processes. It reduces material waste, which helps cut down on production costs and contributes to a more sustainable manufacturing process.
-
Customizable Shapes and Sizes Vacuum forming allows manufacturers to create products in various shapes, sizes, and designs, making it an ideal choice for businesses that require a wide range of customizable products. The ability to produce complex shapes, contours, and textures with a high level of accuracy gives businesses the flexibility to bring their product ideas to life.
-
Quick Turnaround Time Vacuum forming is a fast process, allowing manufacturers to meet tight deadlines and fulfill customer demands quickly. Once the mold is created, the vacuum forming process itself is relatively fast, which is a significant advantage in industries where time-to-market is critical.
-
Durability and Strength Vacuum formed products are not only lightweight but also strong and durable. The plastic sheets used in vacuum forming can be made from a variety of materials, including ABS, PET, PVC, and HIPS, each offering different levels of strength and durability. This makes vacuum forming an excellent option for creating products that need to withstand wear and tear, such as automotive parts or protective packaging.
-
Wide Range of Applications Vacuum formed plastic sheets have a broad range of applications across different industries. In the automotive sector, vacuum-formed parts are used for dashboards, door panels, and interior trims. In packaging, vacuum forming is used to create custom trays, clamshell packaging, and blister packs. The medical industry uses vacuum formed sheets for protective covers, trays, and containers. Additionally, consumer goods such as electronics, toys, and appliances often rely on vacuum forming for parts that require precise dimensions and durability.
Role of Vacuum Forming Plastic Sheets Manufacturers in India
India has become a global hub for manufacturing, and the demand for high-quality vacuum forming plastic sheets has surged in recent years. Among the leading Vacuum forming sheet manufacturers in Ahmedabad are those based in Ahmedabad, a city renowned for its industrial growth and innovation.
Manufacturers in India are playing a pivotal role in meeting the growing demand for vacuum forming plastic sheets across various sectors. These manufacturers specialize in producing high-quality plastic sheets that are tailored to meet specific requirements. With the ability to offer customized solutions, they provide businesses with the materials needed to produce superior products.
Indian manufacturers also focus on using advanced technologies and quality control measures to ensure that the vacuum formed plastic sheets meet international standards. This makes India an attractive destination for companies looking for reliable and cost-effective suppliers.
Manufacturers of Vacuum Forming Sheet in Ahmedabad
Ahmedabad is home to numerous plastic sheet manufacturers that cater to the needs of industries requiring vacuum forming solutions. These manufacturers offer a wide range of plastic sheet products in various thicknesses, colors, and finishes. By leveraging the latest vacuum forming technologies and having access to a skilled workforce, manufacturers in Ahmedabad ensure that their products meet the highest quality standards.
The city’s central location and well-developed infrastructure also make it an ideal base for distributing plastic sheets across India and internationally. Many businesses choose Ahmedabad-based manufacturers for their cost-effectiveness, quality products, and reliable service.
Vacuum Sheets Manufacturers in India: Global Reach
While India is an emerging player in the vacuum forming industry, manufacturers in the country are increasingly catering to global markets. With advancements in technology and the availability of high-quality raw materials, Indian manufacturers are able to produce vacuum forming plastic sheets that meet the diverse needs of international businesses.
Exporting vacuum forming plastic sheets to countries across North America, Europe, and the Middle East has become a lucrative opportunity for manufacturers in India. As demand continues to grow, these manufacturers are investing in state-of-the-art facilities, cutting-edge equipment, and quality assurance processes to ensure that their products meet the rigorous standards required by international customers.
Benefits for Your Business
By sourcing vacuum forming plastic sheets from trusted manufacturers in India, you can enhance your product line in several ways:
-
Access to Cost-Effective Solutions: Manufacturers in India offer competitive pricing without compromising on quality, helping you reduce production costs and increase profit margins.
-
Customization Options: Whether you need a specific color, texture, or size, vacuum forming plastic sheets can be customized to suit your business’s needs.
-
Sustainability: By minimizing material waste and using recyclable plastic materials, vacuum forming is an environmentally friendly manufacturing process.
-
Consistency and Quality: Indian manufacturers are known for their focus on quality control, ensuring that every batch of vacuum forming plastic sheets meets the highest standards.
-
Scalability: As your business grows, vacuum forming can scale with you. With the ability to produce large quantities quickly, vacuum forming offers the flexibility to meet increasing demand.
Conclusion
In conclusion, vacuum forming plastic sheets are an excellent way to enhance your product line, offering cost-effective, customizable, and durable solutions for a variety of industries. By partnering with reliable Vacuum forming sheets manufacturers in India, particularly those in Ahmedabad, you can ensure that your business benefits from high-quality materials that meet your specific requirements.
Frequently Asked Questions (FAQs)
-
What types of plastic materials are used for vacuum forming?
Various types of plastic materials are suitable for vacuum forming, including ABS (Acrylonitrile Butadiene Styrene), PVC (Polyvinyl Chloride), PET (Polyethylene Terephthalate), and HIPS (High Impact Polystyrene). The choice of material depends on the application, required strength, flexibility, and durability. -
How long does the vacuum forming process take?
The vacuum forming process is relatively quick. Once the mold is created, the actual forming process takes only a few minutes. The time it takes to form a product depends on the size and complexity of the mold, as well as the material used. -
Can vacuum formed plastic sheets be used for outdoor applications?
Yes, vacuum-formed plastic sheets can be used for outdoor applications, especially when made from UV-resistant materials. ABS and PVC are commonly used for outdoor products, as they are resistant to weather conditions, UV rays, and other environmental factors.
Leave a Reply