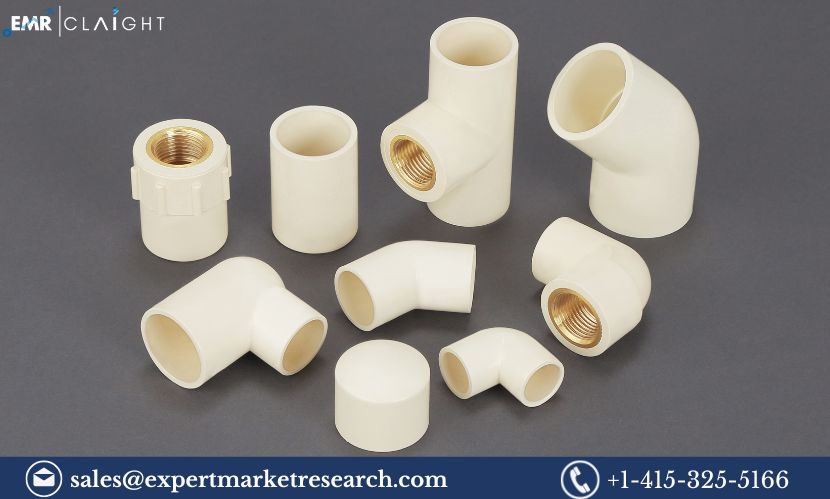
Introduction
A CPVC Pipe Manufacturing Plant Project Report is an essential document that provides comprehensive information for establishing a facility to produce Chlorinated Polyvinyl Chloride (CPVC) pipes. CPVC pipes are widely used in a variety of applications such as plumbing, industrial processes, fire sprinkler systems, and sewage disposal due to their excellent resistance to corrosion, high-temperature tolerance, and durability. The global demand for CPVC pipes is growing, especially in construction and industrial sectors, driven by the increasing need for efficient water and sewage systems.
This project report aims to provide detailed insights into the various aspects involved in setting up a CPVC pipe manufacturing plant, including market analysis, raw materials, manufacturing processes, required equipment, plant layout, financial projections, and regulatory considerations. By developing a robust project report, investors, entrepreneurs, and stakeholders can evaluate the feasibility of the venture and make informed decisions about the setup and operations of the plant.
Market Overview of CPVC Pipes
The CPVC pipe market is experiencing significant growth globally due to the increasing demand for reliable and durable piping solutions in residential, commercial, and industrial construction. CPVC pipes offer a range of advantages over traditional metal pipes, including corrosion resistance, cost-effectiveness, ease of installation, and resistance to high temperatures and chemicals. These features make CPVC pipes ideal for water supply systems, sewage management, and industrial fluid transportation.
With rapid urbanization, the expansion of infrastructure projects, and growing awareness of environmental sustainability, the demand for CPVC pipes is expected to rise. The construction and plumbing sectors, particularly in emerging economies, are key drivers of this demand. Additionally, the increasing need for fire protection systems, which require CPVC pipes due to their heat resistance, is contributing to the growth of the CPVC pipe market.
The market for CPVC pipes is particularly prominent in regions such as North America, Europe, and Asia-Pacific. As the demand for safer and more efficient water management systems continues to rise, CPVC pipes are gaining popularity for both new construction projects and pipeline replacement projects.
Get a Free Sample Report with Table of Contents@
Key Drivers of the CPVC Pipe Industry
Several factors contribute to the growth and demand for CPVC pipes, which make establishing a CPVC Pipe Manufacturing Plant a viable business opportunity. Some of the key drivers of the CPVC pipe industry include:
-
Growing Infrastructure Development: Rapid urbanization and the development of new residential, commercial, and industrial buildings create a steady demand for CPVC pipes in plumbing, water supply, and drainage systems.
-
Awareness of Environmental Benefits: CPVC pipes are an environmentally friendly alternative to metal pipes. They have a longer service life, reduce energy consumption, and require less maintenance compared to traditional piping materials.
-
Increasing Demand for Fire Protection Systems: CPVC pipes are widely used in fire sprinkler systems due to their ability to withstand high temperatures. As fire safety regulations become stricter globally, the demand for CPVC pipes in fire protection systems is increasing.
-
Corrosion Resistance: One of the key advantages of CPVC pipes is their resistance to corrosion, unlike metal pipes, which can rust and degrade over time. This property makes CPVC pipes highly desirable for water and chemical transport systems.
-
Government Regulations and Standards: Government regulations aimed at improving water management systems and infrastructure development are driving the demand for durable, reliable, and safe piping materials, boosting the use of CPVC pipes in public and private projects.
CPVC Pipe Manufacturing Process
The manufacturing process of CPVC pipes involves several stages, from raw material procurement to final product packaging. Each stage requires careful attention to ensure the quality, strength, and durability of the CPVC pipes. Below is an overview of the typical process involved in manufacturing CPVC pipes:
1. Raw Material Procurement
The key raw materials required for the production of CPVC pipes include CPVC resin, stabilizers, lubricants, and other additives. CPVC resin is produced by chlorinating PVC resin, and the final properties of the CPVC pipes depend on the quality and composition of the raw materials. It is crucial to source high-quality CPVC resin from reliable suppliers to ensure the desired properties of the pipes.
2. Mixing of Raw Materials
In this stage, CPVC resin is mixed with stabilizers, lubricants, and other additives in precise proportions. The mixing process ensures uniform dispersion of all ingredients, allowing the CPVC material to possess the required properties such as flexibility, strength, and resistance to heat and chemicals.
3. Extrusion Process
The mixed CPVC material is then fed into an extruder, which is a machine that melts and shapes the material into a continuous pipe. The extrusion process involves heating the material until it becomes molten, and then forcing it through a die to form the desired shape and size of the pipe. The extruder also controls the thickness and diameter of the pipes.
4. Cooling and Calibration
After extrusion, the hot CPVC pipe is cooled rapidly using water or air, which helps the pipe retain its shape and rigidity. Once cooled, the pipe undergoes calibration, where it is passed through a sizing die to ensure that it conforms to the required dimensions.
5. Cutting and Inspection
The cooled and calibrated pipes are then cut into standard lengths, depending on the required size and customer specifications. The pipes are subjected to rigorous inspection to check for defects such as cracks, surface imperfections, and variations in diameter. Quality control tests are carried out at this stage to ensure that the pipes meet industry standards for strength, pressure resistance, and durability.
6. Packaging
Once the pipes pass quality inspection, they are packaged for distribution. The pipes are typically bundled together and wrapped in plastic to prevent damage during transport. They are labeled with product specifications, manufacturing details, and any required safety information.
Equipment and Technology for CPVC Pipe Manufacturing
To successfully manufacture CPVC pipes, a range of specialized equipment and technology is required. The following are the essential machines and systems used in CPVC pipe production:
-
Extruder Machines: The extruder is the primary machine used in the pipe manufacturing process. It melts the CPVC resin and shapes it into pipes. The extruder ensures that the pipes have a consistent size and uniform wall thickness.
-
Mixing and Compounding Equipment: This equipment is used to mix the raw materials such as CPVC resin, stabilizers, and additives in the correct proportions. It ensures that the material has the desired properties.
-
Cooling and Calibration Tanks: These tanks are used to cool the hot CPVC pipes after extrusion and help shape the pipes to the required dimensions.
-
Cutting Machines: These machines are used to cut the CPVC pipes into the desired lengths after they are cooled and calibrated.
-
Testing and Quality Control Systems: Various testing equipment is used to check the mechanical properties, pressure resistance, and dimensions of the pipes. Common tests include burst pressure tests, impact resistance tests, and dimensional inspections.
-
Packaging Machines: Automated packaging machines are used to bundle and wrap the CPVC pipes for shipment. These machines help streamline the packaging process and ensure consistent packing.
Plant Layout and Design
A well-organized CPVC Pipe Manufacturing Plant layout is crucial to maximize efficiency, minimize the risk of contamination, and ensure smooth production. The plant should be designed with the following considerations:
-
Raw Material Storage: A designated area for storing CPVC resin and other raw materials should be available. Proper storage conditions, such as dry and cool environments, should be maintained to ensure the quality of the materials.
-
Production Area: The production area should be spacious enough to accommodate the extruder, mixing equipment, cooling tanks, and other machinery. The flow of materials should be streamlined from one stage to the next, ensuring minimal handling and faster production.
-
Quality Control Lab: A separate area for quality control testing should be incorporated into the plant design. This area should be equipped with the necessary testing equipment and staffed by trained personnel.
-
Packaging and Shipping Area: The packaging area should be designed to ensure proper handling and storage of finished pipes before shipment. The area should be kept clean and free from contaminants.
-
Waste Management: An efficient waste disposal system should be in place to manage any waste generated during the manufacturing process, including plastic scraps and defective products.
Financial Projections and Investment Requirements
A CPVC Pipe Manufacturing Plant Project Report should provide a detailed analysis of the financial aspects of the project. This includes estimates of the capital investment, operational costs, revenue projections, and potential profits. Key financial elements to include are:
-
Capital Investment: The initial capital investment includes costs related to land, building, machinery, raw materials, and installation.
-
Operational Costs: These include ongoing expenses such as raw material procurement, labor, utilities, maintenance, and marketing.
-
Revenue Projections: Revenue projections should be based on anticipated production volumes, market demand, and pricing strategies. These projections help estimate the expected turnover and profitability of the business.
-
Profit and Loss Statement: A detailed breakdown of projected profits and losses over a certain period, such as monthly or yearly, helps assess the financial viability of the business.
-
Return on Investment (ROI): The ROI analysis helps determine the payback period and expected profitability of the venture.
Related Reports
https://www.expertmarketresearch.com/articles/top-meat-companies
Media Contact
Company Name: Claight Corporation
Contact Person: Peter Fernandas, Corporate Sales Specialist — U.S.A.
Email: sales@expertmarketresearch.com
Toll Free Number: +1–415–325–5166 | +44–702–402–5790
Address: 30 North Gould Street, Sheridan, WY 82801, USA
Website: www.expertmarketresearch.com
Aus Site: https://www.expertmarketresearch.com.au
Leave a Reply