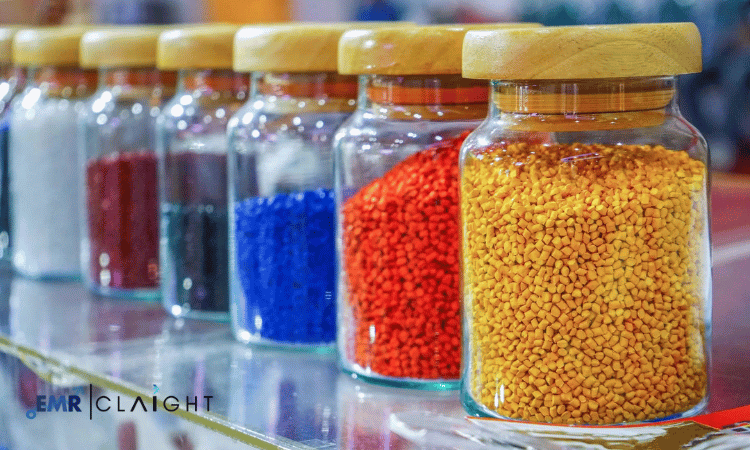
Plastic granules play a crucial role in the manufacturing industry as the primary raw material for creating various plastic products. These small, uniform beads are melted and moulded into a wide range of items such as bottles, containers, automotive parts, and household goods. With the growing global demand for plastic products, setting up a plastic granules manufacturing plant has become an attractive business venture. This article delves into the essential aspects of establishing such a plant, including the processes, materials, and factors to consider for a successful operation.
Overview of Plastic Granules
Plastic granules are tiny pellets or beads of raw plastic that are used in injection moulding, extrusion, and other manufacturing processes. They come in different types depending on the polymer used, such as polyethylene (PE), polypropylene (PP), polyvinyl chloride (PVC), and polystyrene (PS). These granules can be produced from virgin plastic or recycled materials, making the industry versatile and adaptable to modern environmental concerns.
Get a Free Sample Report with Table of Contents@ https://www.expertmarketresearch.com/prefeasibility-reports/plastic-granules-manufacturing-plant-project-report/requestsample
Key Components of a Plastic Granules Manufacturing Plant
-
Raw Material Procurement
Raw materials form the backbone of the manufacturing process. Virgin plastics, recycled plastics, or a mix of both can be used to produce granules. Recycled plastic is increasingly popular due to growing environmental awareness and regulations promoting sustainability. Sourcing high-quality raw materials ensures the production of superior granules. -
Machinery and Equipment
The success of a manufacturing plant largely depends on the quality and efficiency of its machinery. Key equipment includes shredders, extruders, granulators, and cooling systems. Advanced machinery enhances productivity, ensures consistency, and reduces energy consumption, leading to cost savings and better output quality. -
Plant Layout and Design
A well-planned layout ensures smooth workflow and optimal utilisation of space and resources. The design should accommodate all machinery, provide sufficient workspace for employees, and adhere to safety standards. Proper ventilation and waste management systems are also crucial. -
Workforce and Training
Skilled and trained personnel are essential for operating machinery and maintaining quality control. Regular training ensures workers stay updated with the latest techniques and safety protocols, boosting overall productivity and reducing errors. -
Utilities and Infrastructure
Adequate infrastructure, including electricity, water supply, and waste disposal systems, is vital. Reliable power sources are necessary to keep the machines running efficiently, while water is often required for cooling purposes during production.
Manufacturing Process of Plastic Granules
The production of plastic granules involves several stages, each requiring precision and efficiency:
-
Sorting and Cleaning
For recycled plastics, sorting and cleaning are essential first steps. Contaminants such as dirt, metals, and non-plastic materials are removed to ensure the quality of the final product. -
Shredding
The cleaned plastic waste is fed into shredders that break it down into smaller pieces. These flakes are easier to handle and process further. -
Melting and Extrusion
The plastic flakes or virgin material are melted in an extruder at high temperatures. The molten plastic is then forced through a die to create long, thin strands. -
Cooling and Cutting
These strands are cooled, usually in a water bath, and then cut into uniform granules using a pelletiser. The size and shape of the granules depend on the intended application. -
Packaging and Storage
The final granules are dried, sieved, and packaged for storage or transport. Proper labelling and packaging ensure traceability and ease of handling.
Market Potential and Applications
The demand for plastic granules is driven by their versatility and widespread use across industries. Some key sectors that rely on plastic granules include:
- Packaging Industry: Plastic granules are used to manufacture bottles, containers, and films, meeting the needs of food, beverage, and pharmaceutical sectors.
- Automotive Industry: Durable and lightweight parts made from plastic granules contribute to fuel efficiency and aesthetic appeal in vehicles.
- Construction Sector: Pipes, insulation materials, and fittings made from plastic granules offer cost-effective and durable solutions.
- Consumer Goods: Household items, electronics, and toys are commonly manufactured using plastic granules due to their affordability and ease of production.
Environmental Considerations
While the plastic industry has faced criticism for its environmental impact, advancements in recycling technologies and biodegradable plastics are helping mitigate these concerns. Recycled plastic granules reduce the dependence on virgin materials, conserving resources and lowering carbon footprints. Manufacturers are also exploring bio-based plastics made from renewable resources, which can decompose more naturally.
Key Challenges and Solutions
-
Raw Material Quality
Inconsistent raw material quality can affect the production process and final product. Building strong supplier relationships and implementing stringent quality checks can address this issue. -
Regulatory Compliance
Adhering to environmental regulations and safety standards can be challenging but is necessary for sustainable operations. Regular audits and staying informed about local laws help ensure compliance. -
Competition
The plastic granules market is highly competitive. Offering customisable solutions, maintaining high quality, and investing in branding can give manufacturers a competitive edge. -
Technological Upgrades
Keeping up with technological advancements can be costly but essential for maintaining efficiency and meeting customer demands. Gradual investments in upgrades ensure long-term benefits.
Sustainability in Plastic Granules Manufacturing
The growing emphasis on sustainability has reshaped the plastic granules manufacturing industry. Manufacturers are adopting eco-friendly practices such as using solar energy, implementing water recycling systems, and reducing waste through innovative processes. These measures not only improve the environmental impact but also enhance the brandβs reputation in a socially conscious market.
Key Success Factors for a Plastic Granules Manufacturing Plant
- Quality Control: Consistency in product quality builds trust and ensures long-term customer relationships.
- Cost Management: Efficient use of resources and energy-saving measures help optimise costs.
- Innovation: Developing new granule types and exploring niche markets can drive growth.
- Customer Relationships: Providing excellent service and understanding customer needs are crucial for success.
By focusing on these aspects, a plastic granules manufacturing plant can thrive in a competitive market, addressing the increasing demand for diverse plastic products across various industries.
Leave a Reply