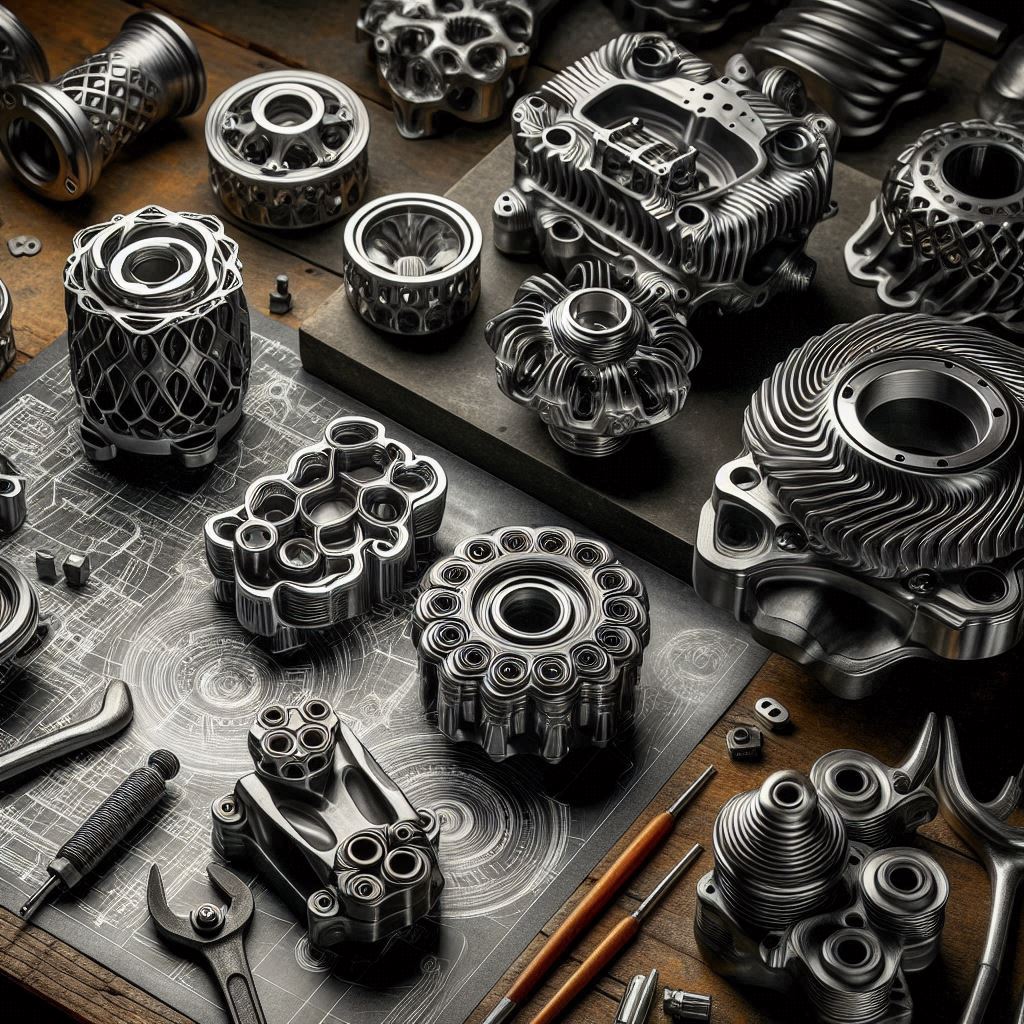
Metal forming can be defined to some extent as the conversion of metals into desired shapes subjected to variations of high pressure and temperature so that levels of property of the metal can further be enhanced to strength and reliability with the components. Ultimately the property of processes will depend on the selection of metal. The forging metals would therefore change from one metal to another depending on the mechanical properties regarding corrosion and heat resistance that different industry sectors will demand-applicable industries being automotive, aerospace, construction, oil and gas, heavy engineering, and machinery. This paper aims at bringing to limelight some of the more common forging metals and their industrial applications therewith.
1. Carbon Steel
Carbon Steel has been said to be the strongest and least expensive among the forging materials. It has very high toughness and wear-resistance properties, therefore being suited for various applications in automotive, construction, and heavy machinery with great significance of end-products such as gears, crankshafts, axles, and bolts. The low-carbon steels can be illustrated with ductility, the medium-high carbon steels are known for their appreciable strength accruing to it in the structure. But carbon steels are prone to corrosion, necessitating certain protective coating applications to improve their durability.
2. Alloy Steel
Alloy steel refers to performance metal, which generally becomes high forging metal with super properties in strength and toughness and impact-resistance qualities. It has found application largely in automotive fields and also aerospace and oil and gas, wherein the tests of extreme wear conditions are envisaged upon parts subjected to tensile and compressive loading. Alloying steel articles include shafts, transmission parts, connecting rods, and drilling tools. Chromium, molybdenum, and nickel inclusion boost corrosion protection and hardness under adverse service conditions.
3. Stainless Steel
Stainless Steel is a corrosion-resistant high-strength material, one that survives against the test of time and maintenance. Because of its moisture, chemicals, and temperature resistance, it finds application in food, medical, marine, and chemicals industries. Some recognized forged parts include fixed valves, pumps, surgical instruments, marine hardware, etc. Stainless steel also contributes its share to aerospace and automobile industries for high-performance exhaust systems and structures for prolonged service even at some extremely adverse conditions.
4. Aluminum
Ideal aluminum is the lightest and high strength metal and yet corrosion resistant with very good conductivity. Considerable importance is laid on this material in aerospace, automotive, and transport sectors since it matters in every detail to make every possible gain in efficiency and performance: aircraft frames, automobile suspension parts, and rail vehicles withstand great value from this. Aluminum is also found to be useful for chemical processing installations and marine installations because of its corrosion-resistant properties, to ensure even performance upon such high adverse environments.
5. Titanium
Titanium is a metal-seeming very soft in weight but extremely strong. Smithing requires treating it against corrosion, and it will withstand the highest temperatures known. Uses for titanium entail aerospace, marine, and medical. Exceptionally demanding parts, for instance, parts of aircraft engines and spacecraft components and even surgical implants are in such applications. Its biocompatibility pegs it among the applications in respect of components for automotive and sports sectors for high-performance applications requiring durability and strength.
6. Copper and Brass
Copper and Brass are ductile and corrosion-resistant metals giving an excellent conductor of electricity besides being laid thermally to a fine degree. Today, they find application in electrical, plumbing, and marine sectors. Copper finds application in electrical connectors as well as in heat exchangers and piping systems. The beauty and sturdiness of brass are in valves, fittings, and many decorative object applications. Such property gives them sufficient resistance to chemicals and moisture, which qualifies them suitable for use in many harsh environments.
7. Nickel Alloys
Nickel alloys provide an outstanding mechanical strength and toughness for components where the materials are used in high temperatures or severe aggressive environments. Applications may be in power generation, aerospace, or chemical industries. The forged applications comprise blade-type turbines, heat exchangers, and some jet engines. The performance and reliability of those components peak while standing against extremely hostile operational conditions for extended lengths of time.
Conclusion
Forging Components, in considering usage, must be viewed in the aspects of strength, endurance, resistance to corrosion, and weight against any specific application in general. The industries producing these metals-carbon steel, alloy steel, stainless steel, aluminum, titanium, copper, and nickel alloys-forged components from applications that add performance, safety, and sometimes longevity in the automotive, aerospace, oil and gas, medical, and construction industries. With forging technology in a fast lane of advancement, new materials developed alongside novel forging processes will only put an additional cast to the quality and economy for forgings made across diverse fields.
Leave a Reply