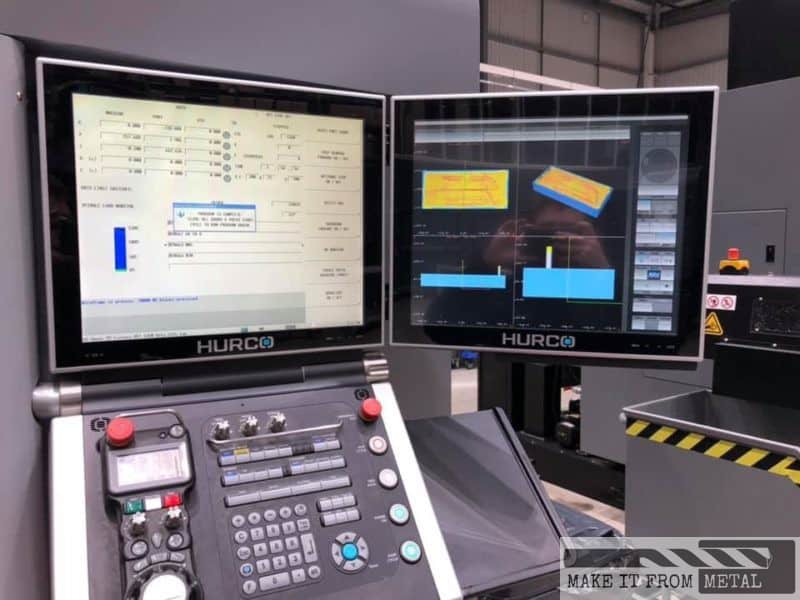
In the world of advanced manufacturing, precision and automation are the keys to success. CNC machining programming plays a vital role in this process, ensuring that machines are able to accurately produce parts from raw materials. Whether for the aerospace, automotive, medical, or any other industry, CNC machining programming helps streamline production, reduce errors, and increase efficiency.
This article explores the fundamentals of CNC machining programming, the various methods used, its importance, and how it has revolutionized modern manufacturing.
What is CNC Machining Programming?
CNC machining programming is the process of creating a set of instructions, typically written in G-code, to control CNC machines. These instructions direct the machineโs movements, tool changes, cutting speeds, and other parameters required to shape raw material into a finished product.
The primary function of CNC programming is to bridge the gap between a computer-generated design (often created using CAD software) and the physical execution of that design on a CNC machine. It ensures that each tool movement is executed with precision and accuracy, which is critical when manufacturing parts with complex geometries and tight tolerances.
Why is CNC Machining Programming Important?
CNC machining programming is essential for several reasons:
1. Precision and Accuracy
CNC programming allows for highly precise machining of parts. With detailed instructions, CNC machines can perform operations such as cutting, drilling, turning, and milling with minimal deviation from the design. This level of precision is critical in industries like aerospace and medical device manufacturing, where even the slightest imperfection can result in failure.
2. Consistency and Reproducibility
Once a CNC program is written, it can be used repeatedly without changes, ensuring that each part produced is identical to the last. This repeatability is essential for mass production, where consistent quality is necessary across thousands of identical parts.
3. Optimization of Production Time
By carefully selecting cutting tools, feed rates, and toolpaths, CNC programming can help reduce the overall time spent on manufacturing parts. Efficient programming ensures that CNC machines operate at their optimal speeds, reducing unnecessary downtime and tool wear while maintaining high-quality production.
4. Minimizing Human Error
CNC programming automates the production process, which minimizes the potential for human error. Unlike traditional manual machining, where operators could introduce errors due to fatigue, inexperience, or lapses in attention, CNC programming ensures that each operation is executed according to the predefined code.
Methods of CNC Machining Programming
There are several approaches to CNC programming, depending on the complexity of the project and the available tools. Below, we outline the most common methods used in CNC machining:
1. Manual Programming
Manual programming, also known as part programming, is one of the most traditional forms of CNC programming. In this method, programmers manually write the G-code (the language used to communicate with CNC machines) that dictates the machineโs movements. Manual programming typically involves using a computer or the CNC machineโs control panel to input the necessary commands for tool movement, speed, and cutting paths.
This type of programming is typically used for simpler, small-run projects where the part design is not too complicated. However, for more complex parts, this method can be time-consuming and prone to errors.
Advantages of Manual Programming:
- Low cost for small production runs.
- Full control over the program, with direct adjustments.
Disadvantages:
- Time-consuming, especially for intricate designs.
- Requires high-level programming expertise.
- Risk of human error.
2. Computer-Aided Manufacturing (CAM) Programming
CAM programming is the most common method used today. It involves the use of CAM software to generate the CNC program. The process starts with creating a 3D model of the part using CAD software, and then the CAM software translates this model into G-code. The program details all the machining operations, including the toolpath, tool selection, feed rates, and cutting parameters.
One of the major benefits of CAM programming is that it can optimize the toolpaths, reducing machining time and improving overall efficiency. Many CAM systems also allow for simulation, which helps detect potential errors before the program is sent to the CNC machine.
Advantages of CAM Programming:
- Faster and more efficient, especially for complex parts.
- Allows for toolpath optimization.
- Provides simulation capabilities to verify the program before machining.
Disadvantages:
- Requires specialized software and knowledge of CAM tools.
- Initial software investment can be high.
3. Conversational Programming
Conversational programming is a more user-friendly method of CNC programming. It is commonly found in CNC machines with conversational controls, where the operator answers a series of prompts on the machineโs interface. The system then generates the G-code based on the userโs input. This is ideal for smaller, simpler parts or operations, where ease of use is a priority over complex automation.
This method doesnโt require in-depth knowledge of G-code and is often used by operators with little programming experience. Itโs common in machine shops where quick programming and setup are essential for small production runs or prototyping.
Advantages of Conversational Programming:
- Easy to use, even for operators with minimal programming experience.
- Quick and efficient for simple tasks and parts.
Disadvantages:
- Not suitable for complex or high-precision parts.
- Limited customization compared to other methods.
4. Adaptive CNC Programming
Adaptive CNC programming refers to programming systems that can adjust in real-time based on feedback from the machine. This approach is often used in high-precision machining environments where tool wear, material inconsistencies, or other factors could affect the machining process.
Adaptive systems monitor real-time data, such as temperature, vibration, or cutting forces, and adjust the program as needed to maintain optimal machining conditions. This method is often used in industries where precision is critical, like aerospace or medical device manufacturing.
Advantages of Adaptive Programming:
- Improves precision by adjusting machining conditions in real-time.
- Reduces the need for manual adjustments during production.
Disadvantages:
- Requires advanced sensors and real-time feedback systems.
- More complex and expensive to implement.
The CNC Machining Programming Process
The process of CNC machining programming involves several steps that ensure the machine performs the correct operations efficiently and accurately. Hereโs an overview of the typical process:
1. Create the Part Design
The first step is to create the partโs digital design using CAD software. This design must be detailed and precise, specifying all dimensions, tolerances, and features necessary for the part.
2. Select Materials and Tools
After finalizing the part design, the next step is to choose the appropriate material (metal, plastic, or composite) and cutting tools (such as drills, mills, or lathes). The material choice directly impacts tool selection and machining parameters.
3. Define Machining Operations
At this point, the programmer specifies the required operations, such as drilling, milling, or turning, and sets the feed rates, cutting speeds, and toolpaths. The programmer ensures the machineโs operations are optimized for efficiency and quality.
4. Generate the CNC Program
Using either manual programming, CAM software, or conversational methods, the CNC program is created. This program contains all the instructions necessary for the machine to perform the required operations.
5. Simulate the Machining Process
Before executing the program, it is often simulated using CAM software to check for potential errors in the toolpath. This helps ensure that the program will run smoothly and that no collisions or mistakes will occur.
6. Run the Program on the CNC Machine
Once verified, the program is uploaded to the CNC machine, and the machining process begins. Operators closely monitor the machine to ensure everything runs correctly and make any necessary adjustments during production.
7. Quality Control
After machining, the part is inspected for dimensional accuracy and quality. If any adjustments are needed, the CNC program is modified, and the process is repeated.
The Future of CNC Machining Programming
As technology continues to evolve, CNC programming is becoming increasingly sophisticated. New advancements, such as artificial intelligence, machine learning, and cloud-based programming, are making it easier for manufacturers to optimize production processes and create even more precise and complex parts.
In particular, the integration of 5G technology and IoT (Internet of Things) will allow CNC machines to communicate in real time, enabling greater automation and remote monitoring. Additionally, the combination of CNC machining with additive manufacturing (3D printing) could lead to more versatile manufacturing methods.
Conclusion
CNC machining programming is an essential element in the modern manufacturing process. Whether using manual programming, CAM software, or conversational programming, the ability to accurately and efficiently transform digital designs into physical parts has revolutionized manufacturing across industries. As technology advances, CNC machining programming will continue to play a crucial role in improving production efficiency, reducing errors, and meeting the growing demand for precision in manufacturing.
Leave a Reply