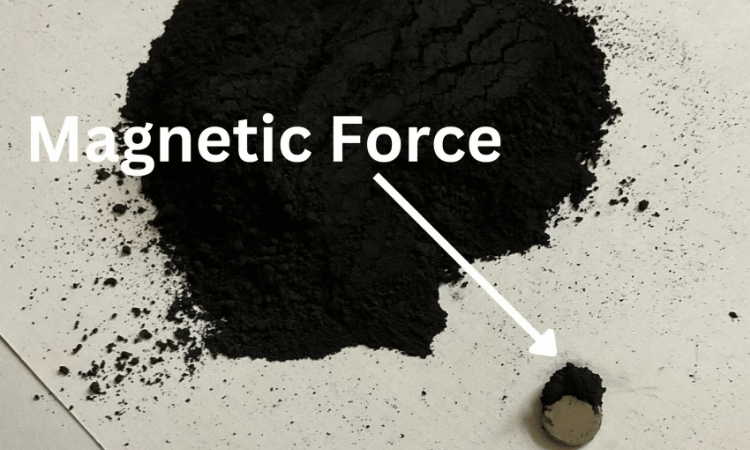
Ferrite magnet powder is a critical raw material widely used in the production of permanent magnets for applications ranging from household appliances to industrial equipment and automotive components. Known for its cost-effectiveness and excellent magnetic properties, ferrite magnet powder has gained immense popularity across various industries. Establishing a manufacturing plant for ferrite magnet powder offers a lucrative opportunity to cater to the growing demand for energy-efficient and high-performance magnetic solutions. Such a project requires meticulous planning, advanced technology, and adherence to environmental and industrial standards.
Understanding the Market
The demand for ferrite magnet powder is driven by its extensive use in industries such as electronics, automotive, renewable energy, and consumer goods. Its ability to retain magnetism over a long period, combined with resistance to demagnetisation and corrosion, makes it a preferred choice for manufacturing permanent magnets.
Primary consumer segments include:
- Electronics Industry: For applications in speakers, sensors, and electric motors.
- Automotive Sector: In components such as alternators, windshield wipers, and power steering systems.
- Renewable Energy Sector: Used in wind turbines and solar panel tracking systems.
- Consumer Goods: Incorporated into items like refrigerators, washing machines, and toys.
Get a Free Sample Report with Table of Contents@ https://www.expertmarketresearch.com/prefeasibility-reports/ferrite-magnet-powder-manufacturing-plant-project-report/requestsample
Location and Infrastructure
Selecting the right location for a ferrite magnet powder manufacturing plant is crucial for operational efficiency. Proximity to raw material sources, transportation hubs, and skilled labour markets can significantly enhance the plantβs productivity and reduce costs.
Key infrastructure requirements include:
- Raw Material Storage Units: Secure areas to store iron oxide, strontium carbonate, and other essential materials.
- Processing Units: Facilities equipped with kilns, grinders, and mixers for producing ferrite powder.
- Quality Control Labs: Advanced laboratories to ensure the consistency and performance of the final product.
- Packaging and Warehousing: Spaces for packaging the powder and storing finished goods.
- Administrative Offices: For overseeing operations, compliance, and customer relations.
Raw Materials and Components
The production of ferrite magnet powder requires high-quality raw materials and precision in their processing. Proper sourcing and handling are essential for maintaining the magnetic properties and durability of the final product.
Key raw materials include:
- Iron Oxide: A primary ingredient for creating magnetic properties.
- Strontium Carbonate or Barium Carbonate: Essential for producing hard ferrite magnets.
- Additives: Such as zinc or cobalt for enhancing specific characteristics.
- Grinding Media: Used in the milling process to achieve the desired particle size.
- Packaging Materials: For safe storage and transport of the powder.
Manufacturing Process
The production of ferrite magnet powder involves multiple stages, each requiring precision and adherence to quality standards. The process ensures that the final product meets the specifications required for diverse industrial applications.
- Raw Material Preparation: Weighing and mixing iron oxide with strontium carbonate or barium carbonate in precise proportions.
- Calcination: Heating the mixture in rotary kilns at high temperatures to initiate chemical reactions that create ferrite.
- Milling: Grinding the calcined material into fine powder using ball mills or jet mills.
- Mixing: Combining the powder with additives to enhance its magnetic properties.
- Quality Testing: Conducting tests to ensure the powder meets industry standards for particle size, magnetic strength, and purity.
- Packaging: Sealing the powder in moisture-resistant containers to preserve its properties.
- Storage and Distribution: Organising the finished product in warehouses for efficient dispatch to customers.
Automation in processes like milling and packaging can improve efficiency and consistency. However, skilled technicians are essential for monitoring quality and overseeing production.
Regulatory Compliance
Adhering to environmental and industrial regulations is crucial for operating a ferrite magnet powder manufacturing plant. Compliance not only ensures legal operations but also enhances the plantβs reputation among stakeholders.
Key regulatory areas include:
- Environmental Standards: Implementing measures to minimise emissions and waste.
- Workplace Safety: Providing protective equipment and training for employees handling raw materials and machinery.
- Material Handling Protocols: Ensuring safe storage and transport of hazardous materials.
- Product Labelling: Accurately marking containers with material specifications and safety information.
Packaging and Branding
Packaging plays a vital role in protecting ferrite magnet powder during storage and transportation. It also provides customers with critical information about the productβs quality and specifications.
Key considerations include:
- Material: Durable and moisture-resistant packaging materials to maintain product integrity.
- Labelling: Clear and detailed labels indicating batch numbers, magnetic properties, and handling instructions.
- Sustainability: Using recyclable or biodegradable materials to appeal to environmentally conscious clients.
Branding efforts should emphasise the productβs quality, consistency, and versatility. Highlighting certifications and adherence to industry standards can build trust and attract customers.
Marketing Strategies
A robust marketing strategy is essential to establish a presence in the competitive ferrite magnet powder market. The focus should be on showcasing the productβs unique attributes and forging long-term relationships with key clients.
Effective strategies include:
- B2B Outreach: Direct engagement with manufacturers of magnets, electronic components, and automotive parts.
- Digital Marketing: Leveraging online platforms to promote the plantβs capabilities and product portfolio.
- Industry Exhibitions: Participating in trade shows to network with potential customers and showcase product samples.
- Export Opportunities: Exploring international markets with growing demand for ferrite magnet powder.
Workforce and Training
A skilled workforce is critical for the efficient operation of a ferrite magnet powder manufacturing plant. Employees must be trained in handling raw materials, operating machinery, and adhering to safety protocols. Regular training ensures that the workforce remains updated on technological advancements and industry practices.
Key roles include:
- Production Technicians: Overseeing the calcination, milling, and mixing processes.
- Quality Assurance Teams: Conducting tests to maintain product consistency and adherence to standards.
- Safety Officers: Ensuring compliance with workplace safety regulations.
- Logistics and Sales Teams: Managing the distribution of finished products and customer relations.
Challenges and Opportunities
While the ferrite magnet powder industry offers significant opportunities, it also presents challenges such as fluctuating raw material prices, competition, and evolving industry standards. However, these challenges can be addressed through innovation and strategic planning.
Emerging opportunities include:
- Sustainable Practices: Developing eco-friendly production methods to align with global sustainability goals.
- Customisation: Offering tailored solutions for specific industrial applications.
- Technological Innovation: Investing in advanced equipment to improve efficiency and product quality.
- Global Expansion: Catering to international markets with high demand for magnetic solutions.
By focusing on quality, innovation, and effective marketing, a ferrite magnet powder manufacturing plant can establish itself as a trusted supplier in this dynamic industry.
Leave a Reply