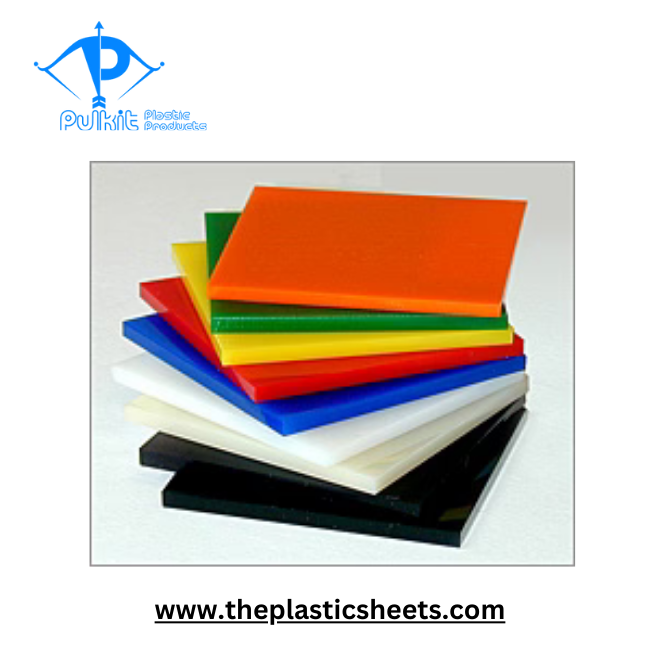
HDPE sheets are among the most versatile and durable materials used across various industries. Known for their excellent chemical resistance, impact strength, and cost-effectiveness, HDPE sheets have become a staple in manufacturing, construction, and beyond. In this guest post, we will dive into the benefits, applications, and frequently asked questions about HDPE sheets to give you a complete understanding of their utility.
What Are HDPE Sheets?
High-Density Polyethylene (HDPE) sheets are thermoplastic polymers known for their strength and lightweight properties. Made from petroleum, these sheets offer Pulkit Plastic Products impressive resistance to chemicals, moisture, and impact. Available in different thicknesses and sizes, HDPE sheets can be customized for various applications, making them a go-to material for industries ranging from packaging to construction.
Advantages of HDPE Sheets
1. Durability
HDPE sheets are exceptionally durable, withstanding impacts, abrasion, and harsh weather conditions. Their longevity makes them ideal for both indoor and outdoor use.
2. Chemical Resistance
These sheets resist most chemicals, acids, and solvents, making them perfect for use in industrial and laboratory settings.
3. Lightweight Yet Strong
Despite their lightweight nature, Polyethylene high density sheet offer high tensile strength, making them easy to handle without compromising on robustness.
4. Moisture Resistance
HDPE sheets are impermeable to water, making them a preferred choice for marine and aquatic applications.
5. Eco-Friendly
HDPE is 100% recyclable, making it an environmentally sustainable material. Recycled HDPE can be used to create new products without compromising quality.
6. Cost-Effective
Due to their durability and low maintenance requirements, HDPE sheets provide excellent value for money over their lifespan.
Common Applications of HDPE Sheets
1. Construction
HDPE sheets are used in construction for applications like underground pipe protection, geomembranes, and temporary flooring. Their moisture and chemical resistance make them indispensable for infrastructure projects.
2. Packaging
The food and beverage industry relies on HDPE sheets for packaging due to their non-toxic and food-safe properties. They are commonly used to create containers, lids, and cutting boards.
3. Agriculture
HDPE sheets are used in agricultural settings for irrigation systems, greenhouse coverings, and water storage tanks. Their UV resistance ensures they perform well under direct sunlight.
4. Automotive Industry
In the automotive sector, HDPE sheets are used for fuel tanks, liners, and other components that require durability and resistance to harsh chemicals.
5. Marine Applications
Thanks to their water resistance, HDPE sheets are used for boat parts, docks, and other marine-related projects.
6. Signage and Displays
Their lightweight and customizable nature make High density plastic sheet a favorite for creating signs, displays, and point-of-sale materials.
How Are HDPE Sheets Manufactured?
HDPE sheets are manufactured using a process called extrusion. Here is a simplified overview:
-
Raw Material Preparation: HDPE granules are prepared and cleaned to ensure consistency.
-
Melting: The granules are melted and fed into an extruder.
-
Sheet Formation: The molten material is passed through a die to form sheets of the desired thickness.
-
Cooling: The sheets are cooled using rollers or water baths to solidify them.
-
Cutting and Finishing: The sheets are trimmed, cut to size, and finished according to the requirements.
Maintenance Tips for HDPE Sheets
-
Cleaning: Use mild soap and water to clean the surface. Avoid harsh chemicals that may cause discoloration.
-
Storage: Store the sheets flat in a cool, dry place to prevent warping.
-
Repair: Minor scratches or damages can be repaired using heat guns or welding techniques.
-
Inspection: Regularly inspect for wear and tear, especially in industrial applications, to ensure optimal performance.
Conclusion
HDPE sheets are an exceptional material that combines durability, flexibility, and eco-friendliness. Their versatility allows them to serve a variety of industries, from construction to food packaging. Whether you need a reliable solution for protecting infrastructure, creating durable containers, or crafting signage, High density polyethylene sheets provide unparalleled performance and longevity.
Investing in HDPE sheets ensures not only the success of your projects but also a sustainable approach to material usage. With proper care and maintenance, these sheets will continue to deliver value for years to come. So, if you’re looking for a dependable, cost-effective, and environmentally friendly material, HDPE sheets are the way to go.
Frequently Asked Questions (FAQs)
1. What is the lifespan of HDPE sheets?
HDPE sheets can last up to 50 years or more, depending on the application and environmental conditions. Their durability and resistance to wear make them a long-term investment.
2. Are HDPE sheets safe for food contact?
Yes, HDPE sheets are FDA-approved for food contact. They are non-toxic and do not leach harmful chemicals, making them ideal for cutting boards, containers, and food packaging.
3. Can HDPE sheets be recycled?
Absolutely. HDPE is 100% recyclable, and recycled sheets can be used to create new products such as pipes, bottles, and construction materials.
4. What are the temperature limits for HDPE sheets?
HDPE sheets can withstand temperatures ranging from -50Β°C to 80Β°C (-58Β°F to 176Β°F), making them suitable for a wide range of applications in different climates.
Β
Leave a Reply