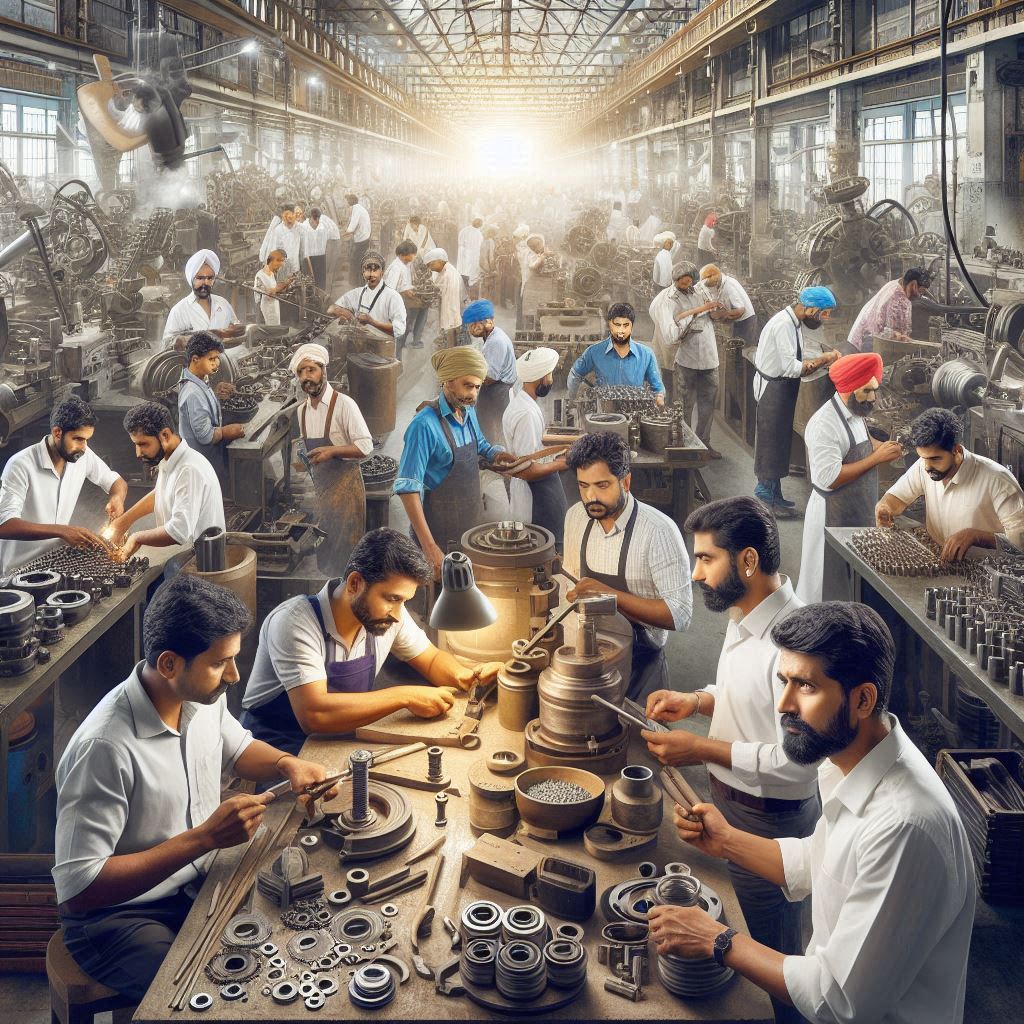
Forged components have been and continue to be thoroughly utilized in almost every industry on the account of their superior strength, toughness, and performance in many demanding applications. Among the uses of forged components are crankshafts, connecting rods, and gears which are all forged important parts that find their common use in the automobile industry, particularly in high-performance vehicles. This is predominantly because these parts need to be reliable under heavy loads and stresses continuously and are exposed to operation years over which the parts should serve. Similarly, forged turbine blades, landing gears, and engine parts are of crucial importance in aerospace to ensure that safety and efficient operations can be carried out within the ambit of the flight environment. Components for heavy-duty equipment such as gun barrels, armored plates, and parts for military vehicles are manufactured mainly out of forged materials. It is due to processing components in this mode that they become known within the defense space since these require extreme permanence owing to the extreme workloads under which they work. Applications can be found in industrial machining and power generation, with components such as pumps, valves, and turbines developing high-pressure and high-temperature working conditions. Forged components can also be seen applied within the oil and gas- forgings flanges, valve bodies, and connectors aligning with the extreme conditions that one can come face to face within offshore and onshore operations. They have strength and reliability, making them essential for such an advantage in these major industries.
How is forged components manufactured?
Forged components India is giving shape to metals under compressive force at elevated temperature for the alignment of the internal grain structure of the metal, thus providing it with strength and durability. The process begins by heating the raw material, usually a metal billet, to a temperature that allows deformation. An object can be heated to very high temperatures; it will combust when placed into a die that is confined within a forging machine, where the action of hammers or presses will compress and deform it. This will have the metal assume the shape desired while improving the grain flow and associated mechanical properties of the material. Several different forging kinds of processes can be employed, such as a precision forged, closed-die forging, or an open-die forging process, all of which can be changed depending on the difficulty level of part forming. Metal parts are then cooled, heat-treated, and given machining and finishing processes to guarantee proper dimensions and surface quality. This is how heat and pressure yield wrought components that give the best strength, reliability, and performance in applications when service stresses approach their limits.
Understanding market trends for forged components
Market trends in forged components reveal a growth in demand due to all the advancements seen in the automobile, aerospace, defense, and power generation industries. The industries moving ever up in importance for lightweight, strong, durable components that can withstand extreme stress and harsh environments. New forging techniques like precision forging and near-net-shape forging now allow manufacturers to develop components with high accuracy, low material wastage, and enhanced specification while considering sustainability. Today, a lot of manufacturers are slowly shifting to energy-efficient processing methods with green materials. Sustainability considerations are also driving many manufacturers to use energy-efficient processing methods, along with eco-friendly materials. Application of automation and digitalization to the forging process will, in that criterion, integrate changes toward cheaper and more effective. In India, rapidly developing infrastructure projects, government initiatives like “Make in India,” and a growing focus on self-reliance will serve to cement the place of India as a key player in the global supply chains for forged components.
Leave a Reply