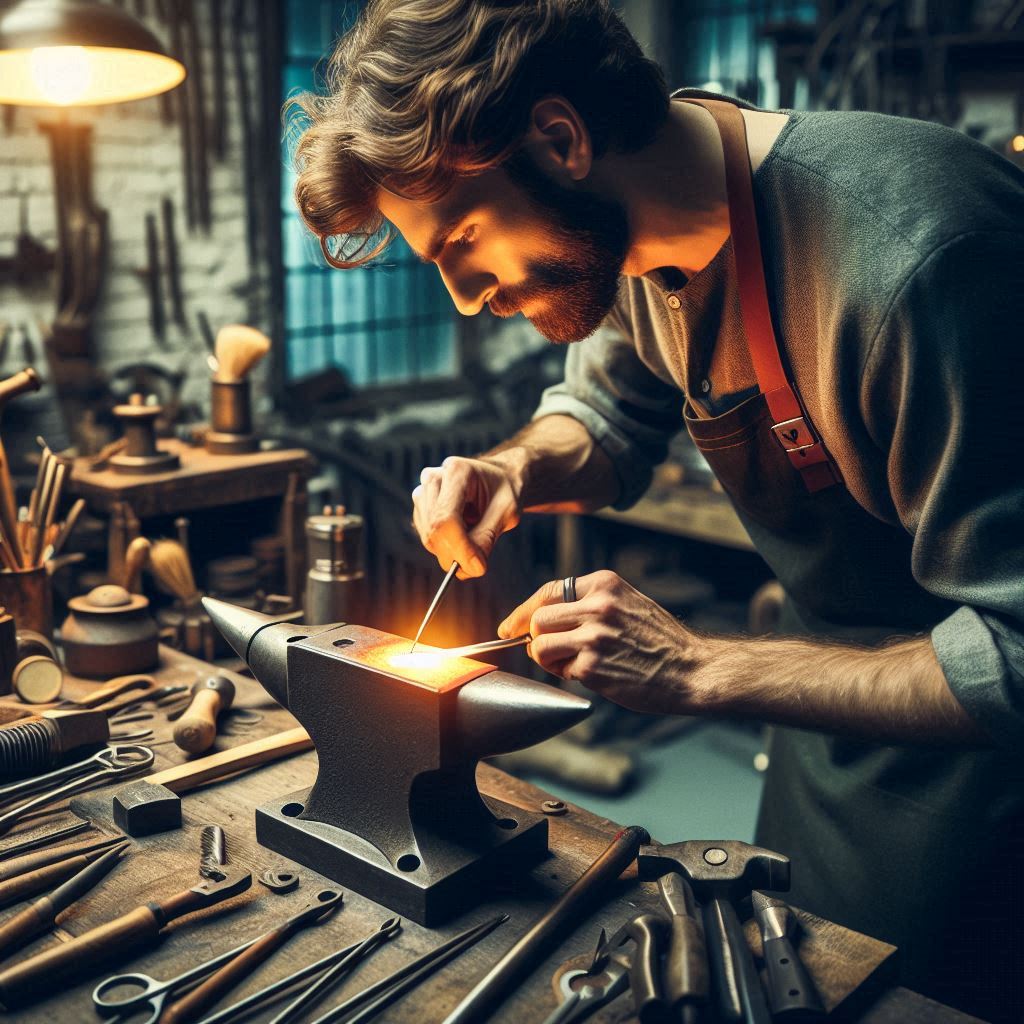
With modern capabilities and advanced forging technologies, coupled with high international industrial quality standards, forging companies are engineering the future of industrial manufacturing. India has become the global hub for forging manufacturing in the industry of best quality forged products for automotive, aerospace, railways, oil & gas, construction, and heavy engineering public services.
Growing The Forging Industry In India
Overall, India’s forging industry has made a rapid growth quite unprecedented due to an increase in demand for high-performance components and technological advancement and also government initiatives like ‘Make in India’. However, domestic demand and export market thrust much from automotive, infrastructure, and industrial sectors. At the same time, Indian forging companies are still in constant international competition, thanks to their efficient and cost-effective type of manufacturing, well-trained workforce, and access to best-quality raw materials such as steel, aluminum, titanium, and nickel alloys. The industry is fur rowed towards sustainable and environment-friendly furniture-making practices that include well-planned advanced heat treatment and precision machining for expected longevity and care for the environment.
Types of Forging Processes in Use Indian Forging Industries
The different forging processes have been used by India forging industries for different industrial requirements. Open-die forging is used for large and relatively simple component shapes, such as shafts and blocks, well-fitted into the hands of power generation and heavy engineering. Closed-die forging is, however, ideal for much intricate parts to be manufactured while producing an enormous volume with high accuracy and strengths, thereby making it a suitable candidate for applications in the automotive and aerospace field. Cold forging is carried at the ambient temperature and preserving good accuracy with a fine surface finish: utilized largely in the automotive industry and the fastener manufacturing industry. Hot forging is engaged in very high-temperature levels of processing; it is for much ductility and even higher-strength components, such as railway, oil & gas, and heavy machinery. Precision forging thus reduces the amount of machining needed after forging, keeping very high accuracy for components such as gears, transmission components, and aerospace parts, thus keeping the Indian forging manufacturers ahead on the world stage into high-performance component production.
Application Of Forged Components In India
India has a very strong foothold in the forge component facing international industries due to a combination of strength, hardness, and small tolerances. The giant automotive actors in the world now depend on Indian forging companies for crankshafts, connecting rods, camshafts, axles, and gears that essentially go into high-performance vehicles. The high-strength forged alloys are used in aerospace and defense for landing gear, engine components, and various structural parts to provide safety and durability under harsh operating conditions. In the railways and locomotion applications of forged train axles, couplings, and suspension elements, it helps tap into both high-speed and freight rail networks. Forged drilling tools, fittings for pipelines, and valve bodies are harnessed in the oil and gas world to withstand extreme pressures and corrosive environments during offshore and onshore exploration. Heavy engineering and construction also employ forged hydraulic cylinders, mining equipment, and structural components for bridges, buildings, and power plants, making an enormous contribution to the infrastructural development of India.
Why An Indian Forging Company?
They would meet all international standards like ISO, ASTM, DIN, and ASME in terms of product quality and reliability, and all standards would be above par. Given their cheaper labor and then operations costing lower, the Indian manufacturer makes the economically feasible offer for products without compromising precision and durability. With their modern facility of CNC machining, advanced heat treatment, and robotic automation, efficiency is permitted to the point of production in the case of the forgings produced in India. In addition, there is already an established export network covering these key components in Europe, the US, and Asia. There is also increased attention on sustainability and innovation, leading India to be selected for its energy-efficient stealing service and environment-friendly forging approaches for high-performance forged components.
Forging Industry Future In India
Forging company India will grow significantly in all directions and pressures as the pace of demand for components engineered with precision surges while forging automation reaches new heights. The Industry 4.0 technologies like AI, IoT, and data analytics are being adopted in the industry to optimize smart manufacturing by improving efficiency, quality control, and predictive maintenance. The steering of forging lightweight components for batteries, drivetrains, and chassis systems toward electric vehicles (EVs) has further contributed to bringing such a momentum into the industry. In addition, various initiatives of the government, especially the PLI scheme, are key enablers to making the domestic manufacturing and export a reality, putting India on the global map as a hub for high-performance forged components in fields such as automotive, aerospace, and heavy engineering.
Leave a Reply