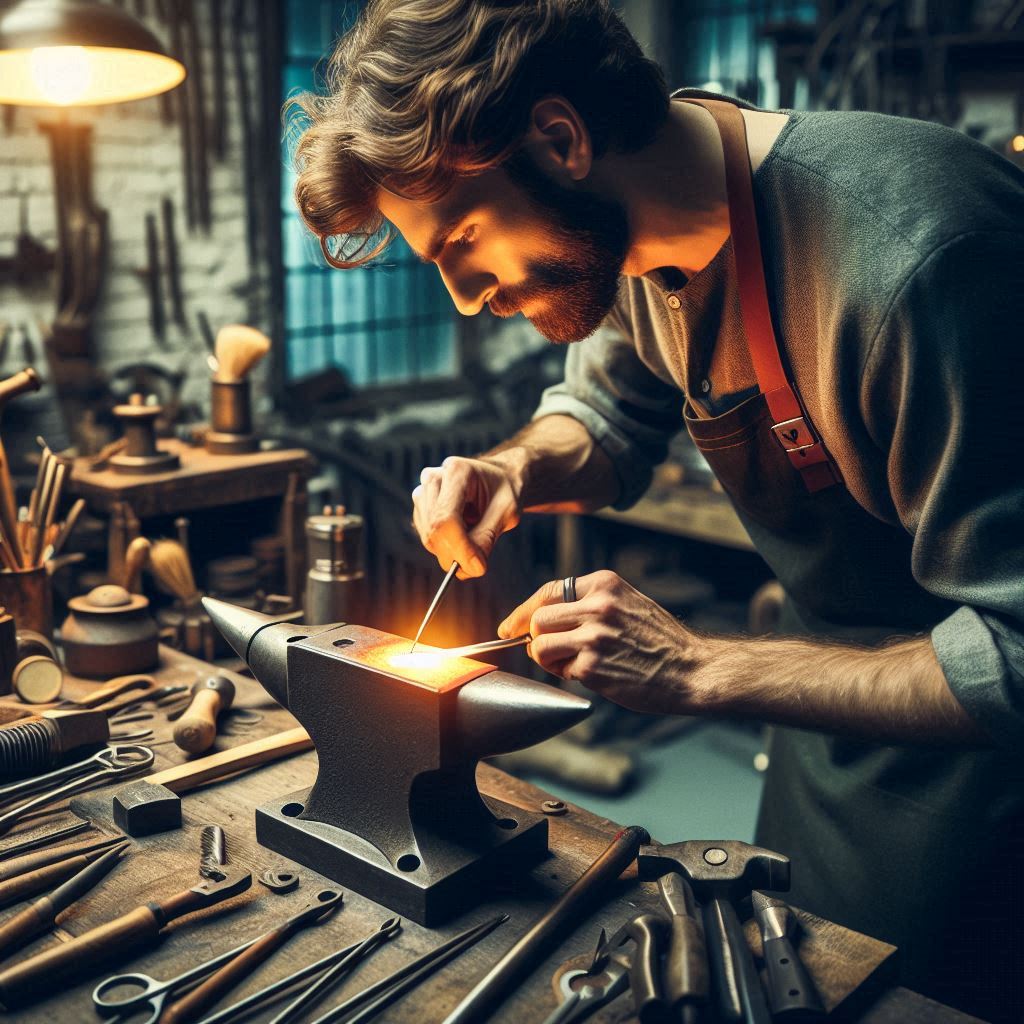
Precision forging is a highly advanced technique established in the area of manufacturing for production of near-net-shape, high-strength components with minimum waste from the material during the forming process. It is controlled shaping of metals above very high pressure and at high temperature for very good mechanical properties, dimensional accuracy, and efficiency cost. This is used in the automotive and aerospace, defense, medicine, and power generation industries, where there can be excellent requisite high-performance components.
Understanding Precision Forging
Precision forging will have much small significant form processing later, such as machining and finishing, in comparison with normal forging. It achieves tight tolerances direct and fine surface finish, as well as complex geometry. Therefore, it provides better conservation of material, increases production efficiency, and lowers total cost of manufacture.
The Precision Forging Basic Parameters are:
- Near net shape production: Minimal machining required after forging.
- Improved strength & endurance: Grain structure refinement improves mechanical properties.
- High dimensional accuracy: Done with minimal secondary machining.
- Cost- and material-efficient: Much less material goes wasted as compared to traditional forging.
- Uniformity and repeatability: Ideal for mass production, where uniformity must be maintained in quality.
Types of Precision Forging:
- Hot Precision Forging: That is, it is about conducting procedure at a pretty high temperature in which ductility is increased and thus permits flow of forging to be reduced. Mainly used in aerospace and automobile industry and some heavy machinery parts, warm forging is concentrated in parts depending on their strength.
- Warm Precision Forging: It is warm because it’s done at a temperature that is not high, just moderate enough to bring in a balanced effect of good material flow while keeping strength really good on the integrity of metals. Possibly the method will be very effective for applications with gears, bearings, and products associated with transmission parts or other similar fields, where the properties of the metals merit strength accuracy.
- Cold Precision Forging: Cold precision forging is done at ambient temperature, and it produces a lot better dimensional accuracy and surface finish. Typical applications are fasteners, bearings, and small automotive parts where high precision is required.
Precision Forging Industries
1. Automotive Industry
Components precision forged like these are crankshafts, gears, connecting rods, and transmission parts, all adding up to the enhancement of vehicle performance as well as fuel economy and longevity. The electric vehicle (EV) industry also employs precision forging to develop lightweight and high-strength components.
2. Aerospace & Defense
All parts from aircraft engine components turbine blades, landing gear components, and structural fittings require high precision, strength along with weight reduction. Precision forging guarantees high fatigue resistance and consistent performance under extreme conditions.
3. Medical
Precision forging for surgical instruments, orthopedic implants, and prosthetic components in terms of good biocompatibility, strength, and surface finish.
- Gas turbines, steam turbines, and components of wind energy need parts to be forged for increasing efficiency as well as durability at high temperature and pressure.
- Heavy Machinery and Industrial Equipment: Forged shafts, axles, hydraulic components, and machine tools carry an enormous load, resist wear, and have tough conditions in which they typically operate, such as found in industry.
Benefits of Precision Forging
- Increased strength: Refined grain structure helps fatigue and impact resistances.
- Improved surface finish: Reduces machining requirements and enhances functionality.
- Material saving: Tends to lesser wastage of material compared to machining intensive processes.
- Production efficiency: Manufacturing cycles come much faster for mass production.
- Sustainability: Lower energy consumptions and reduced effects on the environment.
Conclusion:
Precision forging is revolutionizing the manufacturing world through which high strength, cost-effective, and dimensionally accurate compositions would be availed for critical industries. With the rising demand for parts that are lightweight, durable, and efficient simultaneously, precision forging is one of the top technologies to spearhead innovation and industrial advancement.
Leave a Reply