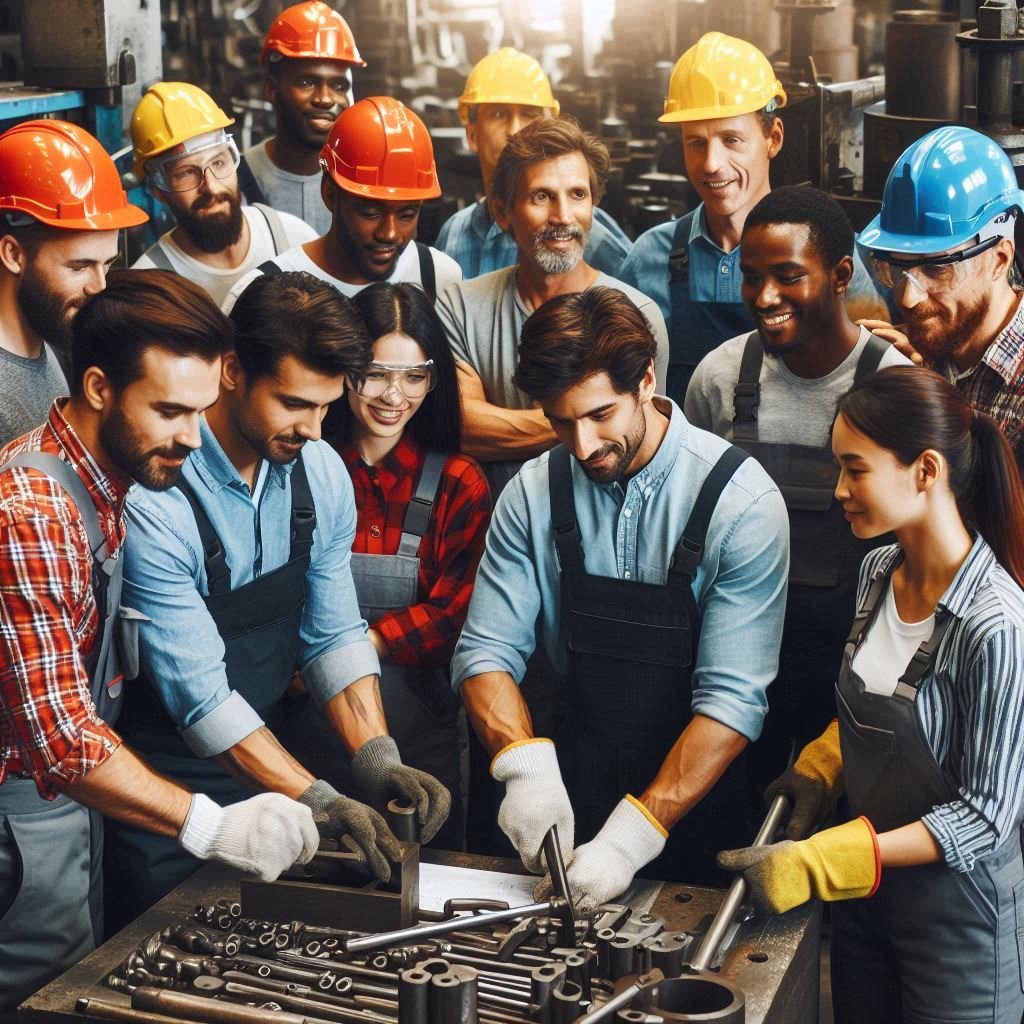
India has, therefore, become the forge of the world with manufacture and supply of forgings to industries like auto, aerospace, railways, oil and gas, construction, and heavy machinery. The forging suppliers within the country have adopted cost-efficient production methods to meet buy-and-demand for domestic and international markets instead of relying on new technology and highly skilled labor. Indian forging suppliers integrate precision, quality, and sustainability that would almost go a long way in assuring that they do contribute in making tomorrow’s industrial manufacturing.
Reasons for Why India is the Hub for Forging Suppliers
There are quite a few reasons that are at the very heart of India’s ranking at the top in the world for forging:
- Abundant Availability of Raw Materials: India acquires rich deposits of steel, aluminum, and other metals, which make it easier to procure raw materials for supply at a competitive price.
- High Technology for Manufacturing: Indian forging suppliers make advances in hot forging, cold forging, open-die forging and closed-die forging for the production of very strong and precision-engineered components.
- Cost of Production: Because of low cost of labor combined with productive production techniques, Indian suppliers therefore have the price advantage in the worldwide market.
- Complying with Global Standards: An Indian supplier complies with ISO, ASTM, DIN, and ASME quality standards, thereby ensuring international specification with respect to durability, safety, and performance.
- Robust Export Market: Exports of forged components from India to Europe, North America, and Asia only strengthen the global supply opportunities from India.
Industries Served by Forging Suppliers in India
1. Automotive Industry
The automotive sector in India is the largest consumer of forged components. The suppliers manufacture crankshafts, connecting rods, gears, axles, suspension components, and transmission parts, keeping them very long-lasting and fuel-efficient. Now Indian forging suppliers are taking up the challenge thrown by electric vehicles (EVs) and developing weight-saving and high-strength components to facilitate energy-efficient mobility solutions.
2. Aerospace and Defense
Parts for aircraft engines, landing gear components, turbine blades, and structural elements that are within the strict aerospace quality standards to meet the conditions of the Make in India initiative further encourage the domestic defense and aerospace forging industry.
3. Railways and Locomotive Industry
Some examples of forged components used for railways include wheel sets, axles, brake components, and couplers. Forging suppliers are producing components that will have a high-strength and wear-resistant design, which are important in developing high-speed rail and metro networks in India.
4. Oil and Gas and Power Sector
Forging plays an important role for oil and gas in valves, fittings, flanges, and drilling tools, all required to operate under high pressures and very high temperatures. The power sector is catered to by suppliers of turbine shafts, generator portions, and pipeline components-all sealable for ensuring effective energy production and distribution.
5. Heavy Machinery and Construction
Forging suppliers create hydraulic cylinders, industrial gears, and mining-related equipment, as well as crane components, which are designed and developed to handle big weights in heavy-duty applications.
Benefits of Indian Forging Suppliers
1. Quality and Precision Engineering
Indian forging suppliers use CNC machining, robotic automation, and AI-enabled quality control for dimensional accuracy and completely defect-free components.
2. Eco-Friendly and Sustainable Manufacturing
Forging companies in India are working on energy-efficient furnaces, waste recycling, and on green forging technologies that would bring down their carbon footprint.
3. Efficient Logistics and Global Supply Chain.
With a well-established port and rail and road networks, Indian forging suppliers ensure on-time delivery to domestic and international markets.Β
Conclusion
The quality of components which are precise-engineering would thus become the ultimate international benchmarks for manufacture in India, in the increased demand for automobiles, aerospace, infrastructure, and energy. This would, in turn, allow Forging suppliers India to seamlessly strengthen the country into the manufacturing paradigm of the global supply chain.
Leave a Reply