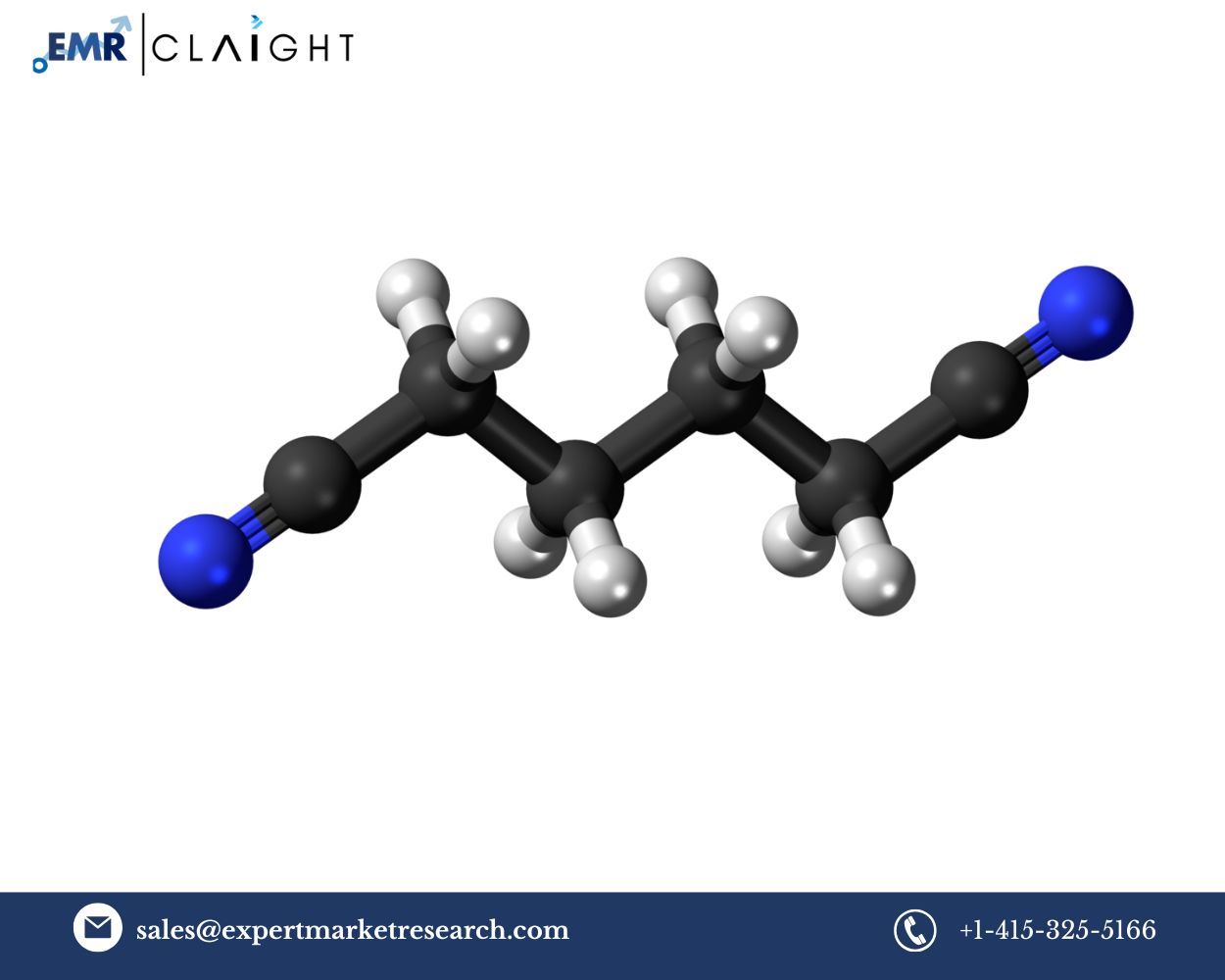
Introduction
The Adiponitrile Manufacturing Plant Project Report is a comprehensive document that outlines the establishment, operation, and financial analysis of an adiponitrile production facility. Adiponitrile is a crucial intermediate chemical widely used in the production of nylon 66, a type of polyamide fiber that is extensively used in industries such as automotive, textiles, and industrial applications. The demand for adiponitrile has been increasing due to its essential role in the manufacture of high-performance materials. As a result, establishing a manufacturing plant for adiponitrile presents an attractive business opportunity.
The process of manufacturing adiponitrile involves complex chemical reactions and requires significant expertise, investment, and resources. This report details the aspects of setting up such a plant, including the market demand, raw materials, production process, plant layout, equipment, financial considerations, and environmental impacts.
Industry Overview
Adiponitrile is primarily produced through the hydrocyanation of butadiene, a key process that converts the compound into adiponitrile. This intermediate is a precursor to hexamethylenediamine (HMDA), which is essential for the production of nylon 66. With the global growth in the automotive industry, along with the increasing demand for lightweight materials and high-performance textiles, the need for nylon 66 and, consequently, adiponitrile, is set to rise.
The production of adiponitrile is critical in the development of several industries, particularly in regions with rapidly expanding textile, automotive, and industrial sectors. Countries such as China, India, and the United States have been major players in this market. The manufacturing plant for adiponitrile, therefore, serves not only as a commercial enterprise but also plays a vital role in the global supply chain.
Get a Free Sample Report with Table of Contents@
Market Demand and Growth Potential
The demand for adiponitrile is closely linked to the growth of the nylon 66 market. As industries strive for more durable, heat-resistant, and lightweight materials, nylon 66 continues to experience an upward trajectory in demand. The automotive sector, which uses nylon 66 for components like airbags, under-the-hood applications, and seat fabrics, is one of the largest consumers of adiponitrile. Additionally, the growth in the textile industry and the demand for more sustainable, high-performance fabrics further boosts the need for adiponitrile.
According to industry analysts, the global adiponitrile market is expected to grow at a compound annual growth rate (CAGR) of approximately 6% in the coming years. This growth is driven by the rising applications of nylon 66 in various end-user industries, including automotive, electronics, and textiles. Therefore, an adiponitrile manufacturing plant represents a significant investment opportunity.
Raw Materials and Supply Chain
The primary raw material used in adiponitrile production is butadiene, which is commonly derived from petroleum or natural gas. Butadiene is a highly flammable, volatile compound, and its extraction requires sophisticated equipment. Other essential materials in the manufacturing process include hydrogen cyanide and catalysts.
The procurement of these raw materials is critical for maintaining a consistent supply and achieving cost-effectiveness in the production process. The availability of these raw materials, along with the cost of transportation and supply chain logistics, will significantly impact the overall cost structure of the plant. Securing reliable and cost-effective suppliers for these key materials is vital to the financial success of the adiponitrile manufacturing plant.
Manufacturing Process
The hydrocyanation process is the primary method used to produce adiponitrile. The process involves the reaction of butadiene with hydrogen cyanide in the presence of a catalyst. The reaction produces adiponitrile as the main product. The process is highly exothermic and requires precise temperature and pressure control to ensure optimal yields.
In more detail, the production steps include:
-
Preparation of Reactants: Butadiene and hydrogen cyanide are first prepared and mixed under controlled conditions.
-
Hydrocyanation Reaction: The prepared reactants are then passed through a reactor where they undergo the hydrocyanation reaction in the presence of a catalyst. This step results in the formation of adiponitrile.
-
Separation and Purification: After the reaction, the adiponitrile is separated from by-products and impurities through a combination of distillation and other purification techniques. This is a critical step to ensure the final product meets the required purity standards.
-
Storage and Packaging: The purified adiponitrile is then stored in tanks or drums and is ready for shipment to various customers.
The efficiency of the manufacturing process, as well as the quality control measures implemented during production, plays a major role in the overall success of the plant.
Plant Layout and Equipment
An adiponitrile manufacturing plant requires several key pieces of equipment, including reactors, distillation columns, heat exchangers, pumps, compressors, and storage tanks. The plant layout is designed to facilitate the efficient flow of raw materials and finished products while ensuring safety and compliance with environmental regulations.
Key Equipment in Adiponitrile Manufacturing:
-
Reactor: A specialized reactor is used to carry out the hydrocyanation reaction under controlled temperature and pressure conditions.
-
Distillation Columns: These columns are essential for separating the adiponitrile from other by-products and impurities to achieve the required product purity.
-
Heat Exchangers: Heat exchangers are used to regulate the temperature of the reaction mixture, which is crucial for the efficiency of the process.
-
Catalysts: Catalysts are used to facilitate the hydrocyanation reaction and are essential to the overall performance and efficiency of the plant.
-
Storage Tanks and Drums: Once the adiponitrile is purified, it is stored in tanks or drums for transportation to customers.
A carefully designed layout and the integration of efficient equipment are crucial for optimizing production efficiency and minimizing operational costs.
Financial Considerations
Establishing an adiponitrile manufacturing plant is a capital-intensive project. The initial investment includes costs for land acquisition, plant construction, equipment procurement, and installation. Moreover, operational costs such as raw material procurement, labor, maintenance, and utilities must be considered in the financial planning process.
A typical project report for an adiponitrile plant will outline the financial projections, including:
-
Capital Expenditure (CapEx): The upfront investment required to build the plant, purchase equipment, and implement safety and quality control systems.
-
Operational Expenditure (OpEx): Ongoing costs associated with running the plant, such as raw material purchases, energy costs, labor, and maintenance.
-
Revenue Projections: An analysis of expected revenue based on market demand, pricing strategies, and production capacity.
-
Return on Investment (ROI): A calculation of the expected return on investment based on the capital and operational expenditures, as well as projected revenue.
-
Break-even Analysis: The point at which the plant’s revenue will cover its fixed and variable costs.
Securing financing for such a project involves presenting a solid business case to investors, demonstrating the viability of the project, and showing potential for profitability.
Environmental Impact and Sustainability
Like any industrial operation, an adiponitrile manufacturing plant must adhere to strict environmental regulations to minimize its impact on the surroundings. The production process involves the use of chemicals such as hydrogen cyanide, which is hazardous and must be handled with care to avoid accidents. Additionally, the plant may generate waste products and emissions that require proper treatment and disposal.
Sustainability in the production of adiponitrile can be achieved by incorporating energy-efficient technologies, recycling waste products, and adopting greener practices in the production process. Implementing waste-to-energy systems and reducing greenhouse gas emissions are also important considerations for an environmentally responsible plant.
Adopting an environmental management system (EMS) that complies with ISO 14001 standards can help mitigate the environmental impact of the manufacturing process, ensuring compliance with global standards and fostering corporate social responsibility.
Safety and Risk Management
Given the hazardous nature of the chemicals involved in the adiponitrile manufacturing process, safety is a top priority. The plant must implement rigorous safety protocols to prevent accidents, protect workers, and minimize the risk of environmental contamination.
Risk management strategies include:
-
Regular Safety Training: Ensuring that all personnel are trained to handle chemicals and equipment safely.
-
Hazardous Material Handling: Establishing guidelines for the safe storage, handling, and transportation of chemicals such as hydrogen cyanide.
-
Emergency Response Plans: Developing plans for responding to potential accidents, including chemical spills, leaks, or fires.
-
Monitoring Systems: Installing monitoring equipment to detect any unsafe conditions, such as excessive pressure, temperature, or toxic gas emissions.
A comprehensive safety management system will help ensure the smooth operation of the plant and protect both the workforce and the environment.
Company Name: Claight Corporation
Contact Person: Peter Fernandas, Corporate Sales Specialist — U.S.A.
Email: sales@expertmarketresearch.com
Toll Free Number: +1–415–325–5166 | +44–702–402–5790
Address: 30 North Gould Street, Sheridan, WY 82801, USA
Website: www.expertmarketresearch.com
Aus Site: https://www.expertmarketresearch.com.au
Leave a Reply