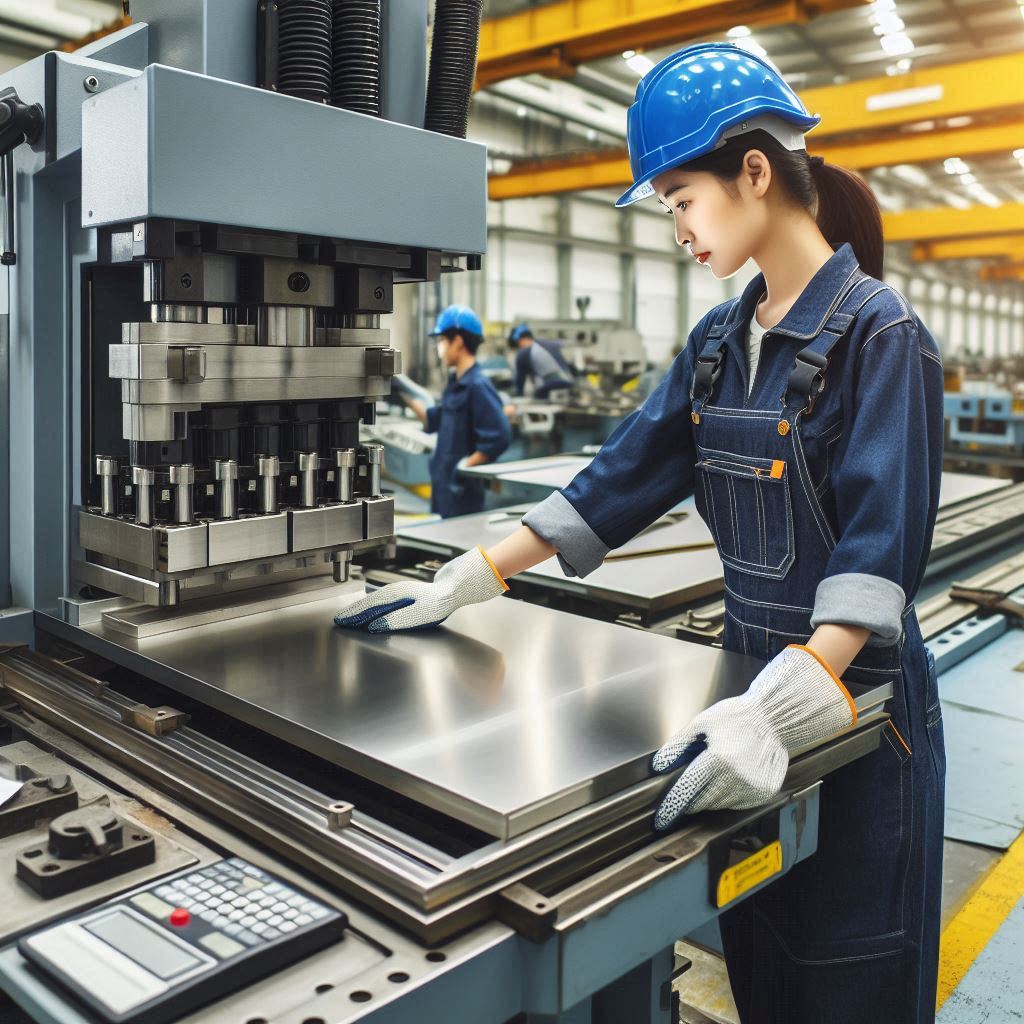
Hydraulic Press Brake Machine is revolutionizing the manufacturing world by offering very high precision and efficiency along with automation in bending metals. Models of hydraulic are quite different compared to the common mechanical press brake because they produce controlled force, using fluid pressure, thus bent the metal sheet with precision accuracy and consistency. With the integration of CNC, it allows these machines to perform high complex bending work with less man-in-the-loop intervention, boosting the production’s speed, quality, and accuracy. Hydraulic press brakes have enabled greater flexibility in the energy-efficiency and improved safety in industry sectors like auto, aerospace, construction, and metal fabrication industries. These modern machines are thus revolutionizing metal forming with low material waste and labor cost by raising the level of productivity generally in the industry.
Introduction to Hydraulic Press Brake Machine
A hydraulic press brake is an industrial, highly powerful device that bends or shapes metal sheets to a high degree of accuracy and efficiency. Hydraulic pressure is used to help the machine apply pressure on a punch and die system that determines the angle through which the metal should bend. Hydraulic press brakes are more flexible, precise, and reproducible than mechanical ones. They are generally suitable for the production of very complex and also high-volume projects. Most typical applications include automobiles, aerospace industries, constructional industries, as well as other metal fabrication plants. After all, hydraulic press brake machines are no exception to the world where there is modern CNC technology and automation; therefore, modern manufacturing relies upon their efficiency, safety, and cost-effectiveness for metal working applications.
Basic elements of Hydraulic Press brake machine
There are several basic elements of a Hydraulic Press Brake Machine that allow for the effective and precise bending of metals by working in a series. These include the pumps, cylinders, and valves that make up the hydraulic system, which provides and controls the force necessitated in bendings. The ram or slide moves vertically under hydraulic pressure, pressing the metal sheet against the die, shaping the material at the required angle. Punch and die sets are made to shape different angles and shapes, and frame and bed make the device sturdy in the whole construction so that the thing can be used for a long period of time. Again, there is also an application of programming through accurate control using CNC, which can be used for better automation to decrease the scope of human error and results in more reproducibility. Other major parts are back gauges for alignment, safety devices, and foot pedals to control operations that are factors that make the machine efficient, accurate, and safe for industrial applications.
Working principle of Hydraulic press brake machine
This kind of machine utilizes hydraulic pressure with which it presses and bends into shape metal sheets with precision accuracy. It mainly comprises a hydraulic system, which is applied to control the movement of the ram, or slide, exerting pressure on a punch that presses against the metallic sheet positioned on a die. When the operator turns it on, it generates force in hydraulic cylinders and the ram moves downward with an opposite motion to crush the sheet into the die for the desired bend angle. In that sense, this CNC system regulates both bending depth and pressure but does so with precise and reproducible positioning. The back gauge assist with proper setting up of sheet metal for a good bending job. A combination of punch and die sets, incorporating pressure regulating means, allows for the machine to accomplish complex configurations in shape and angle that have made this machine one of the most important machines used in the automotive, aerospace industries, but more importantly in the fabrication of metal products.
Application of hydraulic press brake in practical use
The hydraulic press brake machine is applied in various industries as a multi-purpose tool for bending, shaping, and forming metallic sheets with high accuracy and efficiency. It is applied in the automobilistic industries in producing chassis parts, body parts, and brackets. For manufacturing aircraft structural parts and other parts of spacecraft and jet engines, the aerospace industries use the hydraulic press brake machine. It is utilized in the construction and infrastructure industry in the form of steel beams, frames, and metal enclosures. Moreover, it finds use in metal fabrication workshops as it provides custom-cut sheet metal components, cabinets, and enclosures. In addition, hydraulic press brakes with CNC automation allow performing repetitive and complicated high-speed bending operations that can’t be neglected in the manufacturing industries of the present day requiring precision and cost-effectiveness in addition to productivity efficiency.
Conclusion
This way, Hydraulic Press Brake Machine India has replaced the conventional traditional methods of bending and fabrication processes in modern industry through efficiency, precision, and automation. Its hydraulic system with the integration of CNC enables industrial users to have high-accuracy metal components which require minimal loss of material. In addition, this process significantly reduces manual work. It has various applications within the industries for all types. Its applications come across in a productive, cost-effective, as well as secure manner. makes the process productive, safe, and cost-effective. Improving technology and automation make this hydraulic press brake irreplaceable in the emerging world of industry and commerce related to metalwork, especially fine metal products shaping.
Leave a Reply