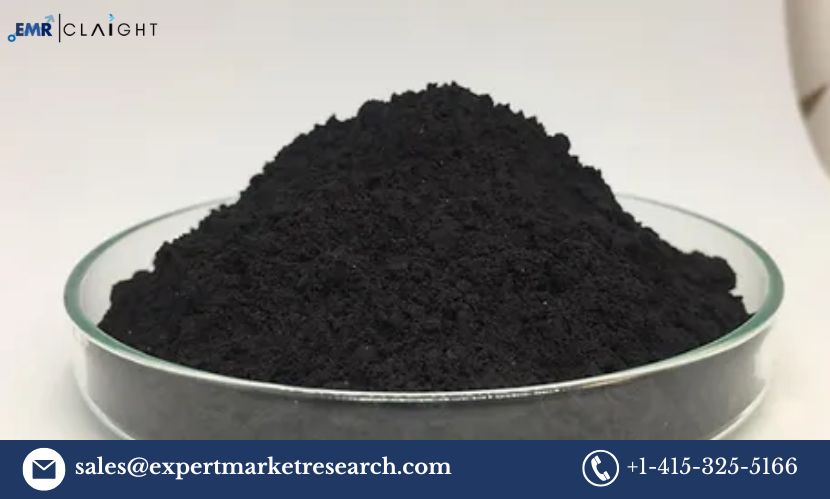
Introduction
Ferrite magnets, a type of ceramic magnet, are widely used in a variety of applications due to their low cost, corrosion resistance, and excellent magnetic properties. These magnets, typically composed of iron oxide (Fe2O3) and other metal oxides, are an integral part of numerous industries such as electronics, automotive, telecommunications, and renewable energy sectors. The Ferrite Magnet Powder Manufacturing Plant Project Report is a comprehensive document that outlines the various factors involved in setting up a manufacturing facility for ferrite magnet powder. It covers market analysis, production processes, required equipment, plant layout, and financial projections.
This project report is designed to guide potential investors, entrepreneurs, and manufacturers in understanding the technical, financial, and operational aspects of establishing a ferrite magnet powder manufacturing plant. The report will provide an in-depth analysis of the demand for ferrite magnets, manufacturing processes, the necessary equipment and technologies, cost structure, and profitability.
Market Demand for Ferrite Magnets
1. Growth in Consumer Electronics
Ferrite magnets are crucial components in a wide range of electronic devices such as speakers, headphones, microphones, and hard drives. With the increasing demand for consumer electronics driven by technological advancements and rising disposable incomes, the demand for ferrite magnets has seen substantial growth. Their low cost and magnetic strength make them the preferred choice for manufacturers of electronic products.
2. Expanding Automotive Industry
The automotive industry is another significant consumer of ferrite magnets. These magnets are used in various applications within vehicles, such as motors for power windows, electric locks, airbags, and sensors. The growing demand for electric vehicles (EVs) and hybrid vehicles, which rely heavily on electric motors, is expected to further fuel the demand for ferrite magnets. Additionally, as automotive manufacturers push for energy-efficient and lightweight solutions, ferrite magnets offer a cost-effective option.
Get a Free Sample Report with Table of Contents@
3. Telecommunications and Renewable Energy Sectors
Ferrite magnets also play a critical role in telecommunications equipment, such as antennas and signal amplifiers, as well as in renewable energy applications like wind turbine generators. As the world transitions to renewable energy sources and digital communications infrastructure continues to expand, the demand for ferrite magnets is poised for further growth.
4. Industrial Automation
The increasing adoption of automation in industrial settings has driven the need for ferrite magnets in motors, sensors, and actuators. Ferrite magnets are used in various industrial applications such as conveyors, automated machines, and robotics due to their strength and reliability in high-temperature and harsh environments.
5. Low-Cost and High-Performance
Ferrite magnets are popular because of their ability to provide high magnetic performance at a relatively low cost. This makes them attractive to manufacturers looking to reduce production costs without compromising on performance. The widespread use of ferrite magnets in budget-friendly products makes them a key player in a wide range of industries.
Plant Location and Infrastructure
1. Proximity to Raw Material Suppliers
The primary raw materials required for manufacturing ferrite magnets are iron oxide (Fe2O3) and other metal oxides such as barium carbonate (BaCO3) or strontium carbonate (SrCO3), depending on the type of ferrite being produced. The plant should be located near suppliers of these materials to reduce transportation costs and ensure a reliable supply chain.
2. Regulatory Compliance
The ferrite magnet manufacturing plant must comply with various industry regulations, including environmental, health, and safety standards. Depending on the location, this may include compliance with local regulations from bodies such as the Environmental Protection Agency (EPA) and occupational safety organizations.
3. Skilled Workforce
The plant will require a skilled workforce to handle the advanced machinery, monitor production processes, and ensure product quality. The location should have access to technical experts in chemistry, materials science, and mechanical engineering. Additionally, the plant will need skilled labor for day-to-day operations, including equipment maintenance and quality control.
4. Utilities and Infrastructure
A reliable supply of electricity, water, and gas is essential for the smooth operation of a ferrite magnet manufacturing plant. The plant will require high-powered furnaces and kilns for sintering the ferrite materials, making a stable power supply critical. Additionally, the location should have robust transportation links to facilitate the delivery of raw materials and the distribution of finished products.
5. Waste Management and Environmental Concerns
The production of ferrite magnets involves the use of chemical processes that may generate waste materials. The plant must implement an effective waste management system to handle hazardous byproducts and ensure compliance with environmental regulations. This includes managing dust, fumes, and chemical waste from the production process.
Manufacturing ProcessΒ
The manufacturing process of ferrite magnet powder is a highly technical and multi-step procedure that requires precision and careful control of various factors. Below is an overview of the key stages involved in the production of ferrite magnet powder.
1. Raw Material Preparation
The production of ferrite magnet powder begins with the procurement and preparation of raw materials. The main ingredients include iron oxide (Fe2O3) and either barium carbonate (BaCO3) or strontium carbonate (SrCO3), depending on the type of ferrite (barium ferrite or strontium ferrite) being produced. These materials are carefully weighed and mixed to create a homogeneous mixture.
2. Calcination
The mixed raw materials are then subjected to calcination in a high-temperature furnace. Calcination involves heating the raw materials to temperatures of around 1000β1300Β°C, causing chemical reactions that form the ferrite material. The process is carefully controlled to ensure that the desired chemical composition and crystalline structure are achieved.
3. Milling and Grinding
After calcination, the ferrite material is cooled and ground into a fine powder using ball mills or other grinding equipment. The size of the powder particles is crucial to the final magnetic properties of the ferrite magnets. A consistent particle size is required to ensure uniformity in the final product.
4. Pressing and Shaping
Once the ferrite powder is prepared, it is mixed with a binder and pressed into the desired shape. This is typically done using a hydraulic press or an isostatic pressing method. The shape of the magnet can vary based on the intended application, and it is essential that the pressing process produces high-density, uniform shapes.
5. Sintering
The pressed ferrite magnets are then sintered in a high-temperature furnace. Sintering involves heating the magnets to temperatures between 1000Β°C and 1300Β°C, allowing the particles to bond and form a solid, durable magnet. The sintering process is crucial for developing the desired magnetic properties and ensuring the structural integrity of the ferrite magnets.
6. Magnetization
After sintering, the ferrite magnets are magnetized using a strong external magnetic field. This process aligns the magnetic domains within the material to impart the desired magnetic strength and properties. Magnetization is a critical step as it determines the final performance of the magnets.
7. Grinding and Finishing
Once magnetized, the ferrite magnets may undergo additional grinding and finishing processes to achieve the required dimensions, surface finish, and shape. This ensures that the magnets meet industry standards and customer specifications.
8. Quality Control
Quality control is an integral part of the ferrite magnet manufacturing process. Several tests are conducted at various stages of production to ensure that the magnets meet the required specifications. These include magnetic property testing (such as residual flux density and coercivity), dimensional checks, and visual inspections to detect defects.
Equipment RequiredΒ
1. Furnaces and Kilns
High-temperature furnaces or kilns are used for calcination and sintering processes. These furnaces must be capable of reaching and maintaining temperatures up to 1300Β°C.
2. Milling and Grinding Equipment
Ball mills, jet mills, and other grinding equipment are required to achieve the fine powder necessary for ferrite magnet production.
3. Pressing Machines
Hydraulic presses or isostatic pressing machines are used to shape the ferrite powder into the desired forms. These machines must be capable of applying uniform pressure to ensure consistent quality.
4. Magnetizing Equipment
Specialized magnetizing machines generate strong magnetic fields to align the magnetic domains within the sintered magnets.
5. Quality Control Instruments
Instruments such as flux meters, microscopes, and dimensional measurement tools are used for quality control and to test the magnetic properties and dimensional accuracy of the finished magnets.
6. Packaging Machines
Automated packaging systems are necessary for safely packaging and labeling the finished ferrite magnets for distribution.
Financial Planning and Investment
1. Initial Capital Investment
The initial investment required for setting up a ferrite magnet powder manufacturing plant includes the cost of land, building infrastructure, procuring equipment, raw materials, and setting up the necessary utilities. Depending on the plant’s scale, the initial investment can range from a few million to tens of millions of dollars.
2. Operating Costs
Operating costs include raw material procurement, labor, utilities, maintenance, transportation, and marketing. Since ferrite magnets require significant energy input during calcination and sintering, energy costs form a significant portion of the operating expenses.
3. Revenue Generation
Revenue will be generated by selling ferrite magnet powder to manufacturers in various industries, including electronics, automotive, telecommunications, and renewable energy. The pricing strategy will depend on production costs, market competition, and customer demand.
4. Profitability
Profitability will depend on the efficiency of the manufacturing process, cost control, and the ability to meet the growing demand for ferrite magnets. By focusing on high-quality production, efficient resource utilization, and expanding market reach, the plant can generate substantial returns.
Media Contact
Company Name: Claight Corporation
Contact Person: Lewis Fernandas, Corporate Sales Specialist β U.S.A.
Email: sales@expertmarketresearch.com
Toll Free Number: +1β415β325β5166 | +44β702β402β5790
Address: 30 North Gould Street, Sheridan, WY 82801, USA
Website: www.expertmarketresearch.com
Aus Site: https://www.expertmarketresearch.com.au
Leave a Reply