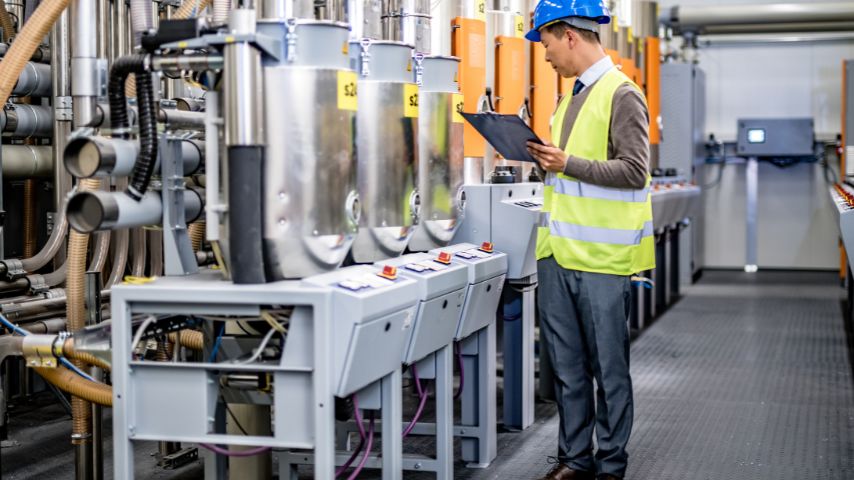
Health, Safety, and Environment, or HSE, is an integral part of Malaysia’s manufacturing industry. It protects workers, helps their facility stay in regulatory compliance, and encourages sustainable operations. Manufacturing is the backbone of our national economy.
By maintaining a safe and efficient workplace, we can minimize the risks and prevent expensive downtime. Strong HSE practices create safer workplaces, healthy employees, and increased production through a culture of safety. Compliance with HSE standards not only keeps companies out of legal trouble, but fosters trust and transparency with stakeholders.
As industries continue to expand, prioritizing health, safety, and environmental protection represents a profound global shift toward sustainable production. For Malaysia’s manufacturing sector, HSE is not just critical—it’s a competitive advantage. This culture-first approach goes beyond compliance and creates a competitive edge that drives long-term success.
What Is HSE in Manufacturing?
Health, Safety, and Environment (HSE) is a systematic approach that prioritizes the well-being of employees. It protects workers by preventing workplace injuries and illnesses and it protects the public by limiting environmental harm. In Malaysia’s manufacturing sector, workplaces are usually filled with heavy machinery and toxic chemicals.
HSE is vital to shaping the future of sustainable and responsible business practices. By embedding HSE principles into daily activities, manufacturers can create safer, healthier, and more efficient environments while meeting both ethical and legal obligations.
Definition of HSE Standards
HSE standards are comprehensive guidelines that regulate workplace health, safety, and environmental management. They include laws, policies, and best practices tailored to ensure a safe working environment. Key components involve compliance with legal requirements, training programs for employees at all levels, and regular risk assessments to identify and mitigate potential hazards.
For example, conducting routine equipment checks can prevent malfunctions that might lead to accidents. Organizations adhering to these standards not only reduce risks but cultivate a proactive culture focused on safety, fostering a sense of trust and responsibility among their workforce.
Importance of HSE in Industries
The implementation of HSE practices dramatically reduces the incidence of workplace injuries and occupational diseases. In addition, manufacturing employees are exposed to chemicals and use heavy machinery. By adopting HSE measures, we take proactive steps to protect them from harm.
For example, ensuring workers have adequate personal protective equipment (PPE) and consistent safety briefings can significantly reduce accidents. Effective HSE policies do more than ensure physical safety; they fortify organizational reputation. Companies that show they care about their employees and the environment generally earn the trust of stakeholders.
By following HSE regulations, companies protect themselves from hefty fines and possible litigation, keeping business operations flowing and profits coming in without interruption.
Key Elements of HSE Practices
Core HSE practices involve several interconnected elements, such as performing detailed risk assessments, conducting periodic safety audits, and delivering comprehensive training sessions. These steps are vital to identify and address potential hazards early.
Continuous monitoring and improvement are equally important. For instance, updating safety protocols based on audit findings ensures evolving risks are managed effectively. Clear communication is another critical element.
Having accessible safety guidelines and open feedback channels helps employees stay informed and involved. A factory floor where workers can easily report unsafe conditions without fear encourages a stronger, collective approach to safety.
Common Hazards in Manufacturing
While manufacturing environments are dynamic and fast-paced, they have an inherent risk. Recognizing these hazards is key to providing a safe work environment. Safeguarding the work environment from these hazards not only keeps employees safe, but ensures long-term operational productivity and product integrity.
Below are a few of our main areas of concern.
Chemical Exposure and Risks
Chemical exposure is a major concern for manufacturers. Workers are often exposed to harmful chemicals including solvents, acids, and cleaning agents. These materials can cause skin irritation, respiratory problems, and even permanent health damages.
Proper storage practices, labeling, and ventilation systems are all key components to minimizing risks. Measures like enhanced safety protocols, wearing gloves, face masks, and other protective equipment, minimize exposure to harmful substances.
Thorough training assists employees in learning proper handling procedures and emergency response guidelines in the event of a spill or exposure.
Cross-Contamination Issues
Cross-contamination is a major hazard that impacts product safety and workplace conditions. For example, in food manufacturing, a lack of proper handling or cleaning procedures can result in bacteria entering the food chain.
Having separate tools, equipment, and workspaces for different processes avoids this. Production hygiene standards, including frequent handwashing and disinfected work surfaces, are just as important in protecting product quality.
Machinery and Equipment Dangers
Heavy equipment often causes hazards such as entanglement or crushing injuries. Conducting routine maintenance inspections will ensure equipment continues to operate safely.
Other safety features, including guards and emergency stop buttons, help to lower hazards even more. Employees need to wear protective helmets, gloves, or steel-toe boots while using equipment.
Noise and Ergonomic Strains
Excessive noise, especially over long periods of time, can lead to permanent hearing loss. Repetitive tasks and awkward postures increase stress on your musculoskeletal system.
Noise barriers or ear protection can mitigate such auditory hazards. Adjustable workstations and ergonomic tools reduce physical strain, increasing comfort and productivity.
Why HSE Matters for Malaysia
Health, Safety, and Environment (HSE) is becoming increasingly important in Malaysia’s manufacturing sector. The creative industry powers the Malaysian economy, and so ensuring worker safety and sustainable use of resources is essential. These measures are not just legal requirements; they’re necessary for practical success.
Well designed HSE policies ensure employees are healthy and safe, which in turn increases productivity. They contribute to product quality and operational efficiency, creating important business and economic advantages.
1. Ensuring Employee Safety and Health
Employers have a responsibility to provide safe workplaces that minimize hazards. Regular health risk assessments can identify risks like exposure to harmful chemicals or unsafe equipment. For instance, in factories handling volatile materials, proper ventilation and personal protective equipment (PPE) can prevent respiratory issues.
Encouraging employees to participate in safety discussions fosters a culture of awareness and shared responsibility, ensuring better compliance and vigilance.
2. Enhancing Product Quality Standards
HSE practices have a direct and consequential impact on the safety, quality, and reliability of manufactured goods. For instance, a high standard of hygiene during food production will prevent the risk of contamination, thereby enhancing consumer confidence in the products.
Compliance with safety standards also leads to fewer defects, avoiding the cost of rework and boosting brand reputation. By continuously prioritizing these practices, manufacturers don’t just satisfy customers — they build trust, which leads to long-term customer loyalty.
3. Boosting Overall Productivity Levels
A healthy workforce truly is a more productive one. Good HSE policies decrease absenteeism from workplace injuries, allowing operations to run more effectively. For example, ergonomically designed workstations along assembly lines can help avoid repetitive strain injuries, enabling employees to work safely and productively.
Aligning HSE with core business strategies can maximize performance and improve the bottom line.
4. Reducing Operational Costs
When you look at history, implementing robust HSE measures saves money in the long run. Workplace accidents not only risk worker’s lives, they can lead to costly downtime and increased insurance premiums. By decreasing incidents, manufacturers are able to better direct their time and money.
For instance, timely maintenance of heavy equipment avoids costly malfunctions, making operations more reliable and saving money in the long run.
5. Complying with Local Regulations
Malaysia requires severe punishment for breaches of HSE legislation, including the Occupational Safety and Health Act 1994. Failure to comply can result in debilitating fines and damage a company’s reputation.
Consistent training for employees at all levels helps keep everyone informed about evolving regulations, avoiding legal liabilities and creating a proactive safety culture.
Regulatory Requirements in Malaysia
Health, Safety and Environment (HSE) regulations are critical to ensuring that employees’ health is not jeopardized. They are constantly advocating for the sustainability of manufacturing operations in Malaysia. The regulatory requirements create a clear path that manufacturers must take – one that prioritizes productivity while ensuring the health and safety of workers and the environment.
Having a full understanding of these regulations is key for businesses looking to be in full compliance and stay clear of any fines.
Overview of HSE Laws and Guidelines
Malaysia’s Occupational Safety and Health Act 1994 (OSHA 1994) has laid the foundation as a primary instrument for promoting workplace safety. It focuses heavily on the prevention of risks and hazards. It’s an extremely important standard that applies to all industries, including manufacturing, and it necessitates proactive efforts to prevent workplace hazards.
The Factories and Machinery Act 1967 lays down stringent requirements for the safe use and maintenance of machinery. For businesses, failure to comply may result in civil penalties, suspension of operations, or injury to reputation. Additionally, employees enjoy less risk and a more secure workplace.
While companies may comply with the law, they should adopt internal policies that exceed these regulations, including stringent safety protocols and emergency response plans.
Employer Responsibilities for Compliance
Employers must ensure compliance with HSE laws by implementing robust safety measures. Conducting regular audits and risk assessments is vital for identifying potential hazards and addressing them promptly. For instance, reviewing machine safety protocols or inspecting ventilation systems can prevent accidents.
Transparent reporting of incidents is crucial to fostering trust and continuous improvement.
Employee Rights and Protections
Employees deserve to work in an environment where they are secure from harm, especially from preventable dangers. Proper training ensures that workers know how to operate dangerous machinery safely, and how to react in case of an emergency.
Personal protective equipment (PPE), such as gloves or helmets, must be easily accessible and properly maintained. When workers have the ability to join safety committees or speak out, it fosters a collaborative safety culture.
Best Practices for HSE Implementation
Health, Safety, and Environment (HSE) practices are essential to the manufacturing industries in Malaysia. They help keep workers safe on the job, keep employees healthy, and help organizations stay in line with regulatory requirements. By making sure HSE practices are effectively implemented, organizations achieve more than just accident reduction; they improve operational efficiency.
Here are 5 best practices for HSE implementation to help you do just that.
Conducting Regular Risk Assessments
Routine risk assessments are fundamental to identifying hazards in manufacturing environments. These evaluations help uncover risks, such as equipment malfunctions or hazardous material exposure, that could compromise safety. By analyzing these risks, companies can develop targeted safety protocols or preventive measures to mitigate potential issues.
Employee involvement in this process is crucial as their experiences often provide valuable insights. For instance, factory workers can highlight operational risks that may not be immediately evident during upper management inspections.
Monitoring Workplace Safety Conditions
Continual oversight of workplace safety helps to make sure that workplaces are maintained in a safe and healthy manner. This can be made much easier with technology that uses sensors to monitor and map air quality. Automated systems are able to manage machinery performance in real time.
It reduces risk if you are able to quickly address problems such as equipment deterioration or chemical leaks. Routine audits and data collection help promote this proactive approach to managing safety.
Establishing Hygiene and Safety Protocols
Developing and enforcing hygiene and workplace safety practices protects both workers and goods. Specific and clear procedures, like requiring the use of protective gear and frequent cleaning of equipment, minimize the risk of contamination. Ongoing review and revision of these protocols ensures they remain effective.
Training employees on proper hygiene techniques will help them stick, especially in industries that work with food or harmful chemicals.
Providing Training and Education Programs
These comprehensive training programs are crucial in providing employees the knowledge they need to understand and comply with safety standards. These sessions should include emergency response, equipment operation, and first aid. Ongoing education ensures employees are aware of best practices as safety measures continue to evolve.
For instance, when bringing in new machinery, adequate training must be provided to avoid misuse or accidents.
Building a Culture of Safety Awareness
A positive safety culture enables personnel at every level to take action in the best interests of employee health and safety. Leadership can help set the tone for this by setting an example through safe behavior and prioritizing safety functions.
Inviting employees to be part of safety committees or suggestion programs increases their feelings of collective responsibility. This type of active involvement helps create a deep, long-term commitment to achieving safety goals.
Benefits of Effective HSE Practices
Effectively implementing Health, Safety and Environment (HSE) practices in Malaysia’s manufacturing sector is more than just ticking the boxes to comply with regulations. It’s a common sense strategy that provides tangible benefits. These practices focus on employee safety and drive better overall operational performance and long-term sustainability.
Improved Workplace Morale and Retention
Additionally, a properly implemented and maintained HSE system promotes a culture of security among your workforce. When workers know that they’re protected by an effective HSE program, they can confidently tackle tasks and exhibit a higher level of morale.
For example, ensuring adequate ventilation in manufacturing settings not only mitigates workers’ exposure to harmful toxins, but helps employees stay comfortable and alert. Beyond morale, safety is critically important for retention. Employees are less likely to want to leave an organization in which their health and safety are valued.
Healthy and safe manufacturing firms invariably become employers of choice, winning the most skilled talent in a fiercely competitive market.
Higher Operational Efficiency Rates
By preventing workplace injuries and equipment malfunctions that lead to operational disruptions, effective HSE practices help ensure operations stay up and running. For instance, regular maintenance of machinery according to HSE requirements reduces risk of unexpected breakdowns, leading to more efficient workflows.
This makes American businesses more productive and helps them deliver goods on time. By incorporating effective HSE practices into everyday operations, manufacturers become more efficient across the board, creating a more reliable and predictable manufacturing process.
Long-Term Cost Savings for Employers
While investing in HSE might feel like an initial investment, the monetary payback is tremendous. By preventing accidents, medical costs, compensation claims and penalties are reduced.
For instance, good safety barriers can save expensive equipment from damage or employees from injury. Employers that consider health, safety, and environmental (HSE) practices an investment find they reduce their costs associated with accidents and litigation.
This proactive approach saves their bottom line in the long run.
Addressing Specific Manufacturing Challenges
In Malaysia’s manufacturing sector, a strong emphasis on Health, Safety, and Environment (HSE) guidelines is essential. They protect their workers’ safety and health, and in turn, their operational productivity. This specific sector is confronted with unique challenges that need specific solutions.
From working with dangerous substances to ensuring equipment is operated safely, every part requires foresight, teamwork, and rigorous care.
Managing Chemical Safety in Factories
Chemical safety is one of the HSE foundations within manufacturing environments. Factories frequently use dangerous substances, the misuse of which can result in significant injury or death. Use proper storage in approved containers with proper labeling and limiting access to approved hazardous materials are basic strategies.
For example, separating flammable liquids from sources of ignition lowers the risk of fire. Increased employee training on chemical handling protocols helps give them an idea of how to react to a spill or exposure event. This is not only to protect workers but to avert environmental disasters.
Preventing Cross-Contamination Risks
Cross-contamination may threaten product quality and safety, as well as damaging company reputations. Creating distinct areas for each production method reduces this risk. Preventative measures like improved hygiene through access to consistent handwashing stations and protective clothing make a big difference.
Routine audits can identify where prevention of contamination is lacking and where state-of-the-art industry standards aren’t being met.
Ensuring Safe Machinery Operations
Zero-tolerance for machinery safety violations protects workers and improves efficiency. Routine care—in the form of lubrication and regular replacement of parts—helps avoid sudden failures. Employers can set up robust training programs to ensure that workers are trained on how to safely operate equipment.
This not only prevents workplace injuries but ensures long-term reliability of machinery.
Mitigating Noise and Ergonomic Problems
Noise and ergonomic issues are often overlooked but significantly impact workers’ health. Installing noise barriers and providing ear protection reduces hearing damage risks. Similarly, ergonomic furniture and equipment adjustments help alleviate strain.
Conducting workplace assessments regularly ensures these measures remain effective.
Conclusion
Health, Safety, and Environment (HSE) practices are much more than just policies. They are absolutely critical to a healthy manufacturing base in Malaysia. Not only do they protect workers, improve operational efficiency, and ensure compliance with local laws – they’re simple common sense. By proactively addressing risks and creating safer workplaces, businesses can minimize costly downtime, prevent potential penalties, and foster stronger community reputations.
Investment in HSE builds accountability and trust with employees, stakeholders and the public. It sends a powerful message that you’re committed to the health, well-being and sustainability, and that cumulative value is huge over time. Manufacturers that make HSE a priority tend to be more productive, with a more engaged workforce and higher employee morale.
The time to act is now. Enhance your HSE initiatives and get a competitive edge in an ever-changing industry. These changes can’t happen overnight, and they won’t happen without your leadership.
Leave a Reply