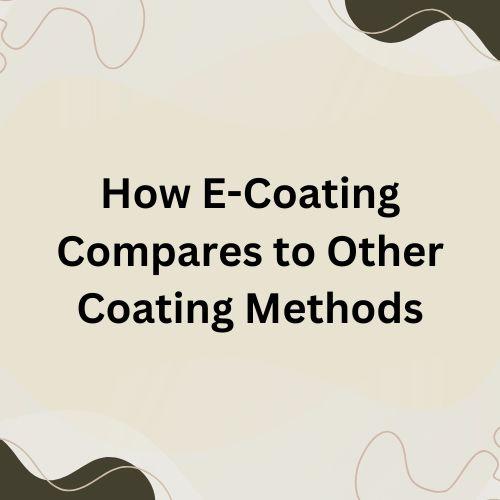
In the industrial world of coatings, durability, efficiency, and cost-effectiveness come together to set the perfect stage. Among several methods, the most promising and widely used electrophoretic coating, commonly known as E-coating, has been getting a lot of attention. Yet, how is it compared with other widely adopted coating techniques: powder coating, electroplating, and good old liquid paint? In this blog, let’s explore E-coating pros and cons with respect to others in terms of durability, application, cost, and environmental considerations.
What is E-Coating?
E-coating or electrophoretic deposition is a process whereby a part is submerged in a water-based paint bath, with an electric charge applied to evenly deposit the coating. The coated component is then cured in an oven to ensure proper adhesion and durability. This method has gained popularity among various industries like automotive, aerospace, appliances, and heavy machinery because of superior corrosion resistance and uniform application.
Comparison of E-Coating with Other Coating Methods
1. E-Coating vs. Powder Coating
- E-coating and powder coating are two very common protective coatings. However, there are several important differences that set these two apart from each other.
- E-coating is a submersion-based process, which is ideal for achieving perfect and extensive coverage even on the most complex components and recessed areas. It has applications in automotive body components and metal constructions where anticorrosive protection is the chief requirement.
- Powder coating, in contrast, is an electrostatic spray process where the powdered paint is applied and then baked to cure. Powder coating has a much thicker, more textured finish and excellent mechanical resistance but fails in deep recesses, which, generally speaking, causes poor coverage in complex shapes.
The advantage of E-coating in terms of accuracy and cost-effectiveness is also possible through thin layers and no added slump, which eliminates waste in material, while powder coating encompasses a wider range of textures and finishes, making it better for decorative applications. In terms of environment, both are green, although E-coating is water-based, which is slightly lower in VOC emissions as compared to the powder coating, which requires special recovery systems for overspray.
2. E-Coating Compared with Electroplating
- Electroplating is primarily used for decorative finishes and corrosion resistance, especially in industries requiring metallic coatings like chrome, nickel, or gold plating.
- During this process, a metal component is submerged in a chemical bath, and an electric current is applied that will deposit a thin layer of metal onto the surface. Electroplating has aesthetic appeal and excellent electrical conductivity but has significant environmental disadvantages in the use of toxic chemicals and heavy metal waste.
- E-coating, on the other hand, offers better corrosion resistance but is more environmentally friendly and cheaper. It could be applied to a greater variety of materials, from conducting to some non-conducting surfaces, while electroplating is limited strictly to metal substrates.
- Moreover, E-coating allows for more choices for color and finish than electroplating, the latter of which is, in most cases, limited to metallic finishes. Nevertheless, electroplating is still the favored technique where a bright, metallic appearance is desired.
3. E-Coating vs. Liquid Painting
- Liquid painting is probably one of the oldest and most widely used methods of coating. It applies a liquid paint using spraying or brushing, then it dries or cures on the surface. Liquid painting allows for an extraordinary range of color and is also very fast, but there are several disadvantages it has compared to E-coating.
- E-coating has more uniform application, as the product is completely immersed, which avoids drips, runs, or uneven spots on the object. It also offers superior durability and adhesion, thus it is more resistant to corrosion, impact, and wear. Liquid painting is more easily applied in small-scale or touch-up applications but has the disadvantage of having inconsistency and needing multiple coats to attain the same level of protection.
- Moreover, E-coating has a lesser environmental impact because it is water-based. Liquid painting, on the other hand, has high VOC emissions that are hazardous to the environment.
Key Benefits of E-Coating Over Other Methods
- Uniform Coverage: Unlike spray-applied coatings, E-coating ensures even coverage on complex and recessed areas, eliminating uneven finishes.
- Corrosion Resistance: Provides exceptional long-term protection against rust, especially for metal parts.
- Cost Efficiency: Lower material wastage and reduced labor costs make it more economical for mass production.
- Eco-Friendly: With its low VOC emissions and water-based composition, E-coating is a greener alternative compared to traditional liquid painting and electroplating.
- Scalability: A highly automated process, it is excellent for high-volume manufacturing with consistent results.
When to Use E-Coating?
E-coating is the best choice if you require:
- Superior corrosion resistance in metal parts.
- Uniform application on complex-shaped components.
- Cost-effective and scalable production.
- Environmentally friendly coating with minimal waste.
However, if you need a thick, textured finish like in powder coating or a bright metallic finish like electroplating, these other methods may be better suited to your requirements.
Conclusion
E-coating is, upon comparison, a very effective method of coating compared to powder coating, electroplating, and liquid painting. It excels in corrosion resistance, uniformity, and cost-effectiveness and is therefore the best choice for automotive, aerospace, and industrial applications. Although other methods have their advantages, the versatility and sustainability of E-coating make it an excellent choice for manufacturers seeking reliable protective coatings.
Leave a Reply