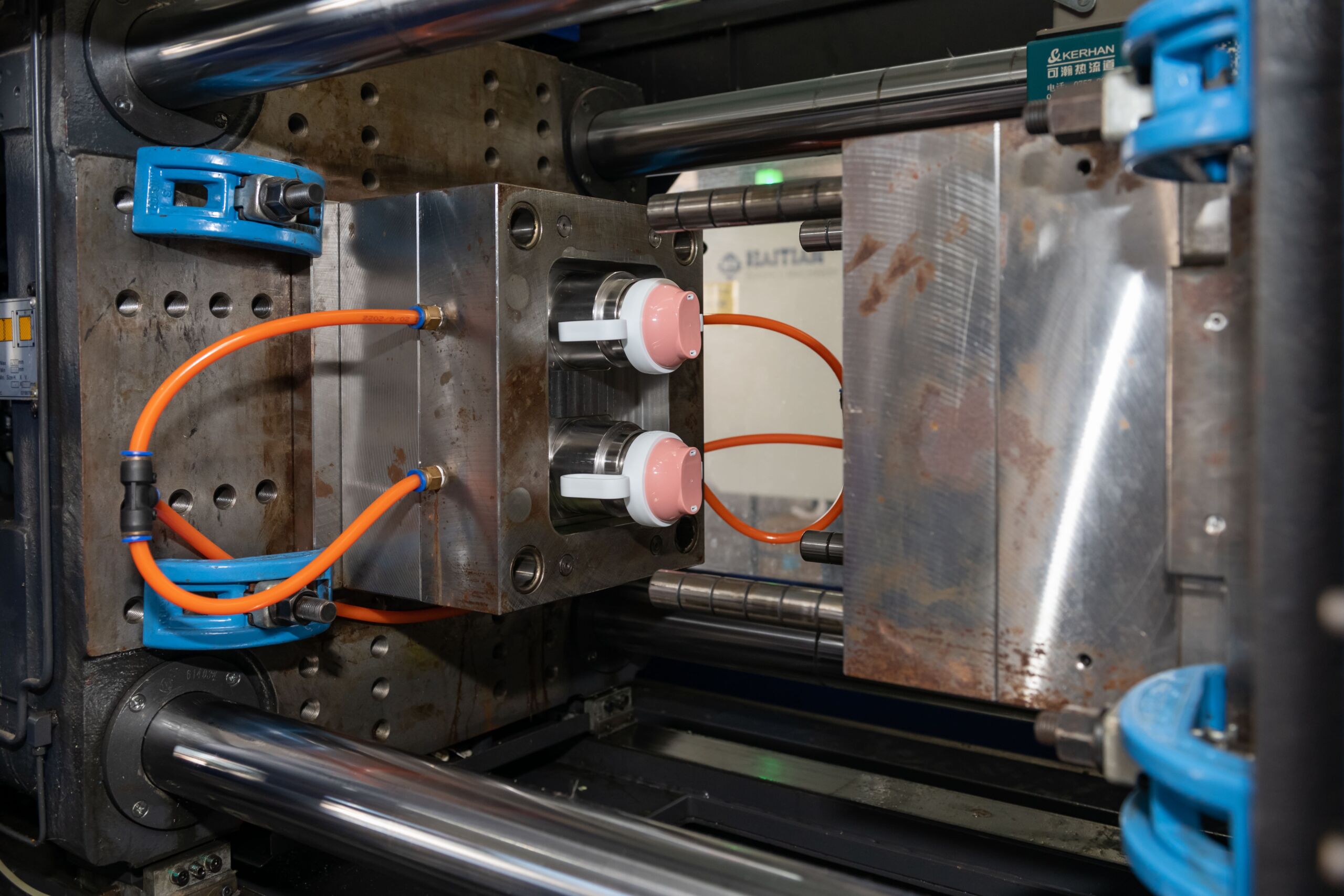
Introduction
Plastic injection molding is one of the most versatile and widely used manufacturing processes in the modern industrial landscape. It allows for the mass production of complex plastic components with high precision, making it a preferred method for industries such as automotive, healthcare, consumer goods, and electronics.
This article delves into the plastic injection molding process, its advantages, applications, and future trends, providing an in-depth understanding of why it has become an integral part of manufacturing worldwide.
What is Plastic Injection Molding?
Plastic injection molding is a manufacturing process that involves injecting molten plastic into a mold cavity under high pressure. Once the plastic cools and solidifies, the finished product is ejected from the mold. This technique is widely used for producing large volumes of identical plastic parts with remarkable accuracy and consistency.
The Injection Molding Process
The injection molding process consists of several key steps:
-
Clamping: The two halves of the mold are securely clamped together.
-
Injection: Molten plastic, heated to a specific temperature, is injected into the mold cavity.
-
Cooling: The plastic cools and solidifies into the desired shape within the mold.
-
Ejection: The finished part is ejected from the mold for further processing.
-
Repeat: The process is repeated for mass production.
Materials Used in Injection Molding
The choice of plastic material is crucial for determining the final product’s quality, durability, and functionality. Some commonly used materials in plastic injection molding include:
-
Polyethylene (PE): Used for packaging and containers.
-
Polypropylene (PP): Commonly found in automotive and medical applications.
-
Polystyrene (PS): Ideal for disposable cutlery and packaging.
-
Acrylonitrile Butadiene Styrene (ABS): Used in consumer electronics and automotive parts.
-
Polycarbonate (PC): A strong, impact-resistant material used in eyewear lenses and medical devices.
-
Nylon: Popular in the automotive and textile industries.
Each material offers unique properties, making them suitable for specific applications.
Advantages of Plastic Injection Molding
Plastic injection molding is favored in various industries due to its numerous benefits, including:
1. High Efficiency and Productivity
Once the mold is created, the process allows for rapid production of large volumes of parts, making it ideal for high-demand industries.
2. Cost-Effectiveness
Although the initial mold-making cost can be high, mass production significantly reduces the per-unit cost, making it an economical choice in the long run.
3. Design Flexibility
Injection molding allows for complex designs with intricate details, including undercuts, textures, and multi-material components.
4. Enhanced Strength and Durability
Various additives can be blended into the plastic to enhance durability, UV resistance, and flame retardancy.
5. Minimal Waste Production
Excess plastic from the injection molding process can be recycled and reused, promoting sustainable manufacturing.
6. Automation and Precision
Advanced robotics and AI-driven systems improve accuracy, consistency, and efficiency, reducing human error.
Applications of Plastic Injection Molding
Plastic injection molding is used in a wide array of industries. Some of the most common applications include:
1. Automotive Industry
Injection-molded components like dashboards, bumpers, and door panels are essential for vehicle manufacturing due to their durability and lightweight properties.
2. Medical Industry
Medical-grade plastics are used to produce syringes, IV components, and surgical instruments with high precision and hygiene standards.
3. Consumer Electronics
Smartphone cases, laptop housings, and TV remote enclosures are commonly produced using plastic injection molding.
4. Packaging Industry
Plastic injection molding enables the production of food containers, bottle caps, and packaging materials with excellent durability and seal integrity.
5. Household and Industrial Products
From kitchen utensils to power tools, injection molding plays a key role in manufacturing essential household and industrial items.
Challenges in Plastic Injection Molding
Despite its numerous advantages, plastic injection molding has some challenges, including:
1. High Initial Costs
The cost of designing and producing molds can be expensive, especially for small production runs.
2. Material Limitations
Certain plastics are not suitable for high-temperature or high-pressure applications, limiting their use in specific industries.
3. Quality Control Issues
Defects such as warping, sink marks, and voids can occur due to improper mold design or inconsistent processing conditions.
Future Trends in Plastic Injection Molding
The plastic injection molding industry is constantly evolving, with several emerging trends shaping its future:
1. Sustainable Materials
The shift toward biodegradable plastics and recycled materials is gaining momentum, reducing the environmental impact of plastic manufacturing.
2. Smart Manufacturing
Automation, AI, and IoT integration are revolutionizing injection molding by improving efficiency, reducing defects, and optimizing production.
3. 3D Printing and Rapid Prototyping
Additive manufacturing is being used alongside injection molding to create prototype molds, reducing development time and costs.
4. Lightweight and High-Performance Plastics
Innovative materials with enhanced strength, flexibility, and thermal resistance are being developed to replace traditional metals in various industries.
Conclusion
Plastic injection molding remains a cornerstone of modern manufacturing, offering unparalleled efficiency, cost-effectiveness, and design flexibility. As technology advances, the industry will continue to evolve with sustainable practices, automation, and innovative materials leading the way.
For businesses looking to optimize their manufacturing processes, investing in plastic injection molding is a strategic move that promises long-term benefits. Whether in automotive, healthcare, or consumer goods, this versatile manufacturing method continues to shape the world around us.
By understanding the principles, benefits, and trends in plastic injection molding, companies can make informed decisions to stay ahead in an ever-competitive market.
Leave a Reply