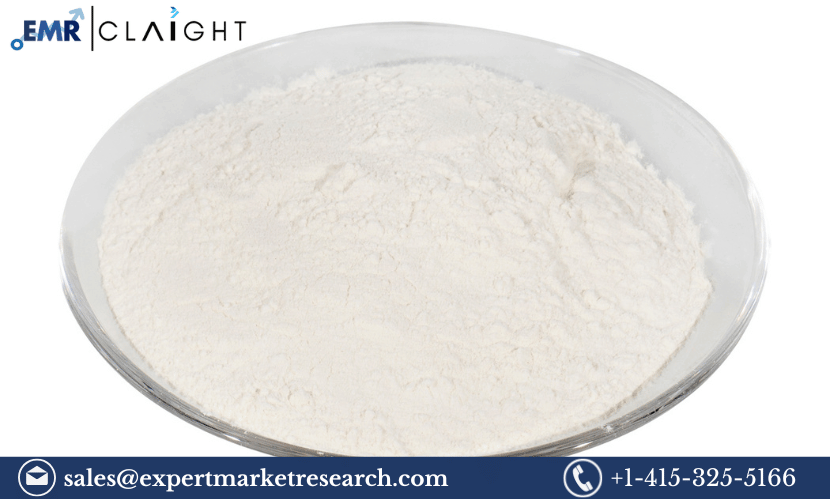
Allylamine, a colorless organic compound, is widely used in the chemical and pharmaceutical industries for the synthesis of various chemicals, including agrochemicals, pharmaceuticals, and surfactants. This versatile compound serves as a building block in the production of polymers, rubber, and resins, playing a significant role in numerous industrial applications. Allylamineโs ability to act as a reactive intermediate makes it valuable in processes such as polymerization and chemical synthesis. Establishing a manufacturing plant for allylamine offers significant business potential due to its widespread demand in various sectors. This report explores the critical aspects of setting up an allylamine manufacturing plant, including raw material sourcing, production processes, equipment, regulatory compliance, and market opportunities.
Overview of Allylamine
Allylamine (C3H7NH2) is an amine compound, primarily utilized as a precursor in the synthesis of other chemicals. It is produced by the reaction of ammonia with propene in the presence of a catalyst. Allylamine is widely used in the manufacture of alkylamine derivatives, such as allyl alcohol, which is used in the production of various resins and surfactants. Allylamine is also a key ingredient in the production of agrochemicals, particularly herbicides and fungicides, which are crucial for the agricultural industry.
In the pharmaceutical sector, allylamine is used as a building block for several drugs, including treatments for various medical conditions. Furthermore, allylamine is essential in the production of specialty chemicals, including surfactants and detergents. As a versatile chemical intermediate, the demand for allylamine continues to rise, especially in industries focusing on the development of advanced materials, sustainable agriculture, and pharmaceutical products.
Get a Free Sample Report with Table of Contents@ https://www.expertmarketresearch.com/prefeasibility-reports/allylamine-manufacturing-plant-project-report/requestsample
Key Considerations for Setting Up the Manufacturing Plant
Establishing a manufacturing plant for allylamine involves several important steps, ranging from site selection and raw material procurement to production processes, equipment, and market research. Below are the critical factors to consider:
1. Location and Site Selection
The location of the manufacturing plant is crucial for optimizing operational efficiency and reducing costs. Key factors to consider include:
- Proximity to Raw Material Suppliers: The primary raw materials for allylamine production are ammonia and propene. The plant should be located near suppliers of these materials to minimize transportation costs and ensure a continuous supply.
- Access to Utilities: The production of allylamine requires significant amounts of electricity, water, and waste disposal services. Ensuring the availability of these utilities is critical for uninterrupted operations.
- Logistics and Distribution: The plant should be located near transportation routes, such as highways or rail networks, to facilitate the movement of raw materials and finished products. Efficient distribution is necessary to meet customer demand and minimize transportation expenses.
- Labor Availability: The plant requires skilled labor for various stages of production, including chemical processing, machinery operation, quality control, and maintenance. The site should be near areas with access to a skilled workforce.
Choosing the right location reduces operational costs, improves production efficiency, and ensures the plant’s long-term success.
2. Raw Materials and Procurement
The primary raw materials for the production of allylamine are ammonia and propene. Securing a reliable supply of these materials is essential for maintaining a consistent production flow. Key procurement considerations include:
- Ammonia: Ammonia is widely available and typically produced through the Haber-Bosch process. It is an essential raw material for the production of allylamine and must be sourced from reliable suppliers to ensure consistency and quality.
- Propene: Propene is derived from petroleum refining processes, particularly from cracking processes. Ensuring a steady supply of high-quality propene is critical for maintaining production efficiency.
- Packaging Materials: Packaging materials for the finished product must be durable and resistant to moisture and other environmental factors to preserve the quality of allylamine during transport and storage.
Securing high-quality raw materials from trusted suppliers ensures smooth operations and helps maintain production schedules.
3. Manufacturing Process
The production of allylamine typically involves the following key steps:
- Ammonia and Propene Reaction: Allylamine is produced by reacting ammonia with propene in the presence of a catalyst. This reaction typically takes place in a high-temperature, high-pressure reactor. The ammonia and propene react to form allylamine, which is then purified and processed further.
- Purification: After the reaction, the resulting allylamine mixture undergoes purification to remove impurities such as unreacted ammonia, propene, and byproducts. Purification methods include distillation, filtration, and other separation techniques.
- Drying and Packaging: Once purified, allylamine is dried to remove any residual moisture. The final product is then packaged in suitable containers, such as drums or tanks, to protect it from contamination and ensure its stability during storage and transportation.
Each stage of the manufacturing process must be carefully controlled to ensure the consistent quality and purity of the final product.
4. Quality Control
Maintaining high-quality standards is crucial for ensuring that the allylamine meets industry specifications and customer requirements. Quality control measures should be implemented at every stage of production. Key quality control checks include:
- Raw Material Inspection: Ammonia and propene should be inspected upon delivery to ensure that they meet the required purity standards and are free from contaminants.
- Process Monitoring: During the reaction and purification stages, process parameters such as temperature, pressure, and chemical ratios should be carefully monitored to ensure that the allylamine is produced according to specifications.
- Purity Testing: The final product should be tested for purity and concentration using techniques such as gas chromatography, spectrometry, and titration.
- Physical Properties Testing: The physical properties of allylamine, such as color, viscosity, and appearance, should be inspected to ensure they meet the required standards.
- Packaging Inspection: After packaging, the allylamine should be inspected for any defects, such as damaged containers or improper seals, which could compromise the quality of the product.
Rigorous quality control ensures that allylamine is consistently produced to the highest standards, meeting both regulatory requirements and customer expectations.
5. Regulatory Compliance
Compliance with local and international regulations is essential for operating a successful allylamine manufacturing plant. Key regulatory considerations include:
- Chemical Safety Standards: Allylamine is a hazardous chemical, and its production must comply with chemical safety regulations such as OSHA (Occupational Safety and Health Administration) standards. Safety protocols should be followed to protect workers from exposure to harmful chemicals.
- Environmental Regulations: The production process involves the use of ammonia and propene, both of which can have environmental impacts if not properly managed. The plant must comply with regulations related to air and water emissions, waste disposal, and chemical handling.
- Product Labeling: Allylamine must be correctly labeled with safety warnings, handling instructions, and regulatory information to ensure proper storage, handling, and transport.
- Certifications: Obtaining certifications such as ISO 9001 for quality management or ISO 14001 for environmental management can help demonstrate the plantโs commitment to quality and sustainability.
Regulatory compliance ensures that the plant operates within legal guidelines, prioritizing worker safety and environmental responsibility.
Equipment and Technology
The production of allylamine requires specialized equipment to handle the chemical reactions, purification processes, and packaging. Key equipment includes:
- Reactor Vessels: These vessels are used to carry out the reaction between ammonia and propene. They must be able to withstand high temperatures and pressures while maintaining safety and efficiency.
- Separation and Purification Units: Distillation columns, filtration units, and other separation technologies are used to purify the allylamine and remove any impurities or byproducts from the reaction.
- Drying Equipment: Dryers are used to remove any residual moisture from the final product to ensure stability during storage.
- Packaging Machines: Automated packaging systems are used to fill and seal containers with the final product. These machines ensure that the allylamine is packaged securely and efficiently for transport.
Investing in advanced equipment helps streamline production processes, improve efficiency, and ensure high product quality.
Workforce and Training
A skilled workforce is crucial for the smooth operation of the allylamine manufacturing plant. Key roles in the workforce include:
- Production Operators: These workers are responsible for overseeing the reaction process, operating machinery, and ensuring that the plant runs smoothly.
- Quality Control Technicians: To monitor and test raw materials, in-process products, and finished allylamine to ensure that they meet quality standards.
- Machine Operators: To operate and maintain specialized equipment such as reactors, filtration units, and packaging machines.
- Safety Officers: Ensuring compliance with safety protocols and overseeing the implementation of protective measures for workers handling hazardous chemicals.
Training programs should be implemented regularly to ensure workers are equipped with the necessary skills and knowledge to operate machinery safely and efficiently.
Packaging and Distribution
The packaging and distribution process is essential for maintaining the quality of allylamine during transport. Key considerations include:
- Packaging Materials: Packaging should protect the allylamine from contamination, moisture, and other environmental factors. Containers should be made of materials that are resistant to chemical reactions.
- Labeling and Documentation: Proper labeling is required for regulatory compliance and to ensure the safe handling of the product. Packaging should include information about the product, safety guidelines, and handling instructions.
- Distribution Channels: Establishing reliable distribution networks ensures that allylamine is delivered efficiently to customers in the required quantities and on time.
Environmental and Safety Aspects
Ensuring sustainability and worker safety is essential in the allylamine production process. Key initiatives include:
- Waste Management: Implementing waste reduction and recycling systems to minimize environmental impact.
- Energy Efficiency: Using energy-efficient technologies and processes to reduce the plantโs carbon footprint.
- Worker Safety: Providing workers with proper PPE and ensuring that the plant adheres to health and safety regulations.
Market Applications and Trends
Allylamine has diverse applications across industries, including:
- Agriculture: In the production of agrochemicals, such as herbicides and fungicides.
- Pharmaceuticals: As a precursor for various pharmaceutical compounds.
- Chemicals: In the synthesis of specialty chemicals such as surfactants and resins.
Emerging trends include:
- Sustainable Practices: Increasing demand for sustainable production methods.
- Energy Storage: Growing interest in the use of allylamine derivatives in energy storage technologies, particularly in batteries.
Challenges in Manufacturing
Challenges in allylamine manufacturing include:
- Raw Material Availability: Ensuring a consistent and reliable supply of ammonia and propene.
- Safety Concerns: Managing the risks associated with handling hazardous chemicals.
- Regulatory Compliance: Adhering to changing regulations related to chemical safety and environmental standards.
By addressing these challenges, manufacturers can capitalize on the growing demand for allylamine and position themselves for long-term success in the market.
Leave a Reply