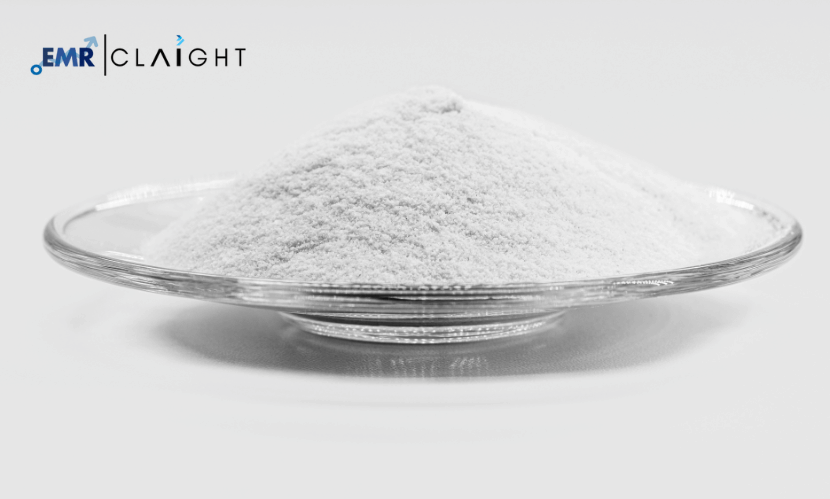
Magnesium phosphinate is a versatile compound widely used in various industries, including flame retardants, plastics, and advanced material applications. Its unique properties, such as thermal stability and environmental compatibility, make it a preferred choice for enhancing safety and performance in manufacturing processes. Setting up a magnesium phosphinate manufacturing plant involves advanced chemical processes, rigorous quality control, and adherence to environmental standards. This article provides an in-depth guide to the production processes, equipment requirements, and key considerations for establishing a successful magnesium phosphinate manufacturing facility.
Understanding Magnesium Phosphinate
Magnesium phosphinate is a phosphorus-based compound commonly employed as a flame retardant additive in thermoplastics, thermosets, and other polymers. Its ability to enhance fire resistance while maintaining material properties makes it essential in automotive, electronics, and construction sectors.
Get a Free Sample Report with Table of Contents@ https://www.expertmarketresearch.com/prefeasibility-reports/magnesium-phosphinate-manufacturing-plant-project-report/requestsample
Key Processes in Manufacturing
- Raw Material Sourcing and Preparation
- High-quality magnesium compounds and phosphinic acid are sourced. These raw materials undergo stringent quality checks to ensure compatibility and efficiency in the production process.
- Reaction Process
- Magnesium and phosphinic acid are combined under controlled conditions in a reactor. Temperature, pressure, and reaction time are monitored to optimise yield and product quality.
- Filtration and Purification
- The reaction mixture is filtered to remove impurities and by-products. Purification techniques ensure the final product meets industrial standards for purity and performance.
- Drying and Granulation
- The purified product is dried to remove moisture and then granulated into the desired particle size for ease of use in applications.
- Quality Testing
- Rigorous testing is conducted to verify the productβs thermal stability, flame retardant properties, and chemical composition.
- Packaging and Storage
- The finished product is packaged in chemical-grade containers to maintain quality during transportation and storage.
Essential Equipment for a Manufacturing Plant
Setting up a magnesium phosphinate manufacturing plant requires specialised equipment for efficient and safe production. Key equipment includes:
- Reactors: For conducting controlled chemical reactions.
- Filtration Systems: To remove impurities from the reaction mixture.
- Drying Units: For removing moisture and preparing the product for granulation.
- Granulators: To create uniformly sized particles for industrial use.
- Quality Testing Instruments: For analysing thermal stability, composition, and performance properties.
- Packaging Machines: For securely sealing and labelling containers.
Designing the Plant Layout
An efficient plant layout ensures streamlined operations and compliance with safety standards. Key considerations include:
- Raw Material Storage: Secure areas for storing magnesium compounds and phosphinic acid.
- Processing Zones: Dedicated sections for reaction, filtration, drying, and granulation.
- Quality Control Laboratory: Equipped for testing raw materials and finished products.
- Packaging and Labelling Areas: Automated systems for sealing and branding products.
- Waste Management Systems: Facilities for treating and disposing of by-products responsibly.
Quality Control in Manufacturing
Maintaining consistent quality is critical in magnesium phosphinate production. Key quality control practices include:
- Raw Material Testing: Verifying the purity and compatibility of magnesium compounds and phosphinic acid.
- Process Monitoring: Ensuring optimal reaction conditions for efficiency and consistency.
- Product Testing: Evaluating flame retardant properties, thermal stability, and chemical composition.
- Packaging Inspection: Checking for secure seals and accurate labelling.
Regulatory and Licensing Requirements
Setting up a magnesium phosphinate manufacturing plant involves compliance with various safety and environmental regulations. Key requirements include:
- Chemical Safety Certifications: Adherence to standards for handling and storing hazardous materials.
- Environmental Clearances: Managing emissions, waste, and effluents to minimise environmental impact.
- Labelling Compliance: Providing accurate product information, including safety precautions.
- Workplace Safety Regulations: Ensuring safe handling of chemicals and equipment through training and protocols.
Applications of Magnesium Phosphinate
Magnesium phosphinate has diverse applications across multiple industries, including:
- Flame Retardants: Used in polymers to enhance fire resistance in automotive, construction, and electronics products.
- Advanced Materials: Incorporated into composite materials for improved thermal stability.
- Plastic Additives: Added to thermoplastics and thermosets for superior flame retardant properties.
- Coatings and Paints: Used in fire-resistant coatings and industrial paints.
- Specialty Chemicals: Applied in research and development for customised formulations.
Sustainability in Manufacturing
Sustainability is a growing focus in magnesium phosphinate production. Key measures to enhance sustainability include:
- Efficient Resource Use: Optimising raw material utilisation to minimise waste.
- Emission Control: Implementing advanced technologies to reduce harmful emissions.
- Recycling By-Products: Developing systems to repurpose waste materials into useful products.
- Energy Efficiency: Employing energy-saving technologies in production and purification processes.
Market Trends and Opportunities
The magnesium phosphinate market is expanding due to its critical role in flame retardant applications. Key trends include:
- Growing Demand for Flame Retardants: Increased safety regulations drive demand in automotive, construction, and electronics industries.
- Innovation in Material Science: Development of advanced materials incorporating magnesium phosphinate.
- Sustainability Focus: Rising adoption of eco-friendly flame retardant solutions.
- Global Expansion: Higher adoption in emerging markets with growing industrialisation and infrastructure development.
Challenges in the industry include:
- Raw Material Availability: Ensuring a consistent supply of high-quality raw materials.
- Regulatory Compliance: Navigating complex environmental and safety standards.
- Market Competition: Differentiating products through innovation and consistent quality.
By leveraging advanced manufacturing technologies, ensuring stringent quality control, and focusing on sustainability, manufacturers can establish a successful magnesium phosphinate production facility to meet the growing global demand across industries.
Leave a Reply