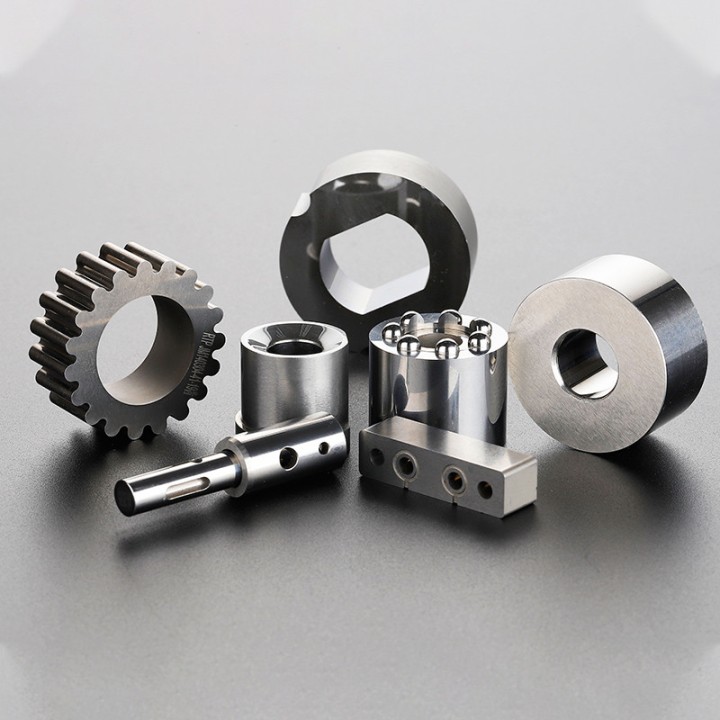
In the world of modern manufacturing, the need for precision and accuracy is paramount. Whether itβs in aerospace, automotive, electronics, or medical industries, precision components are the foundation of reliable, high-performance products. These components are crucial for the overall functionality, durability, and safety of the final product. This article delves into what precision components are, their importance in various industries, and the technology behind their creation.
What Are Precision Components?
Precision components refer to parts that are manufactured with a high degree of accuracy and tight tolerances. These components are designed to fit, function, and interact with other parts seamlessly within a given assembly or product. The manufacturing of precision components requires sophisticated equipment, such as CNC (Computer Numerical Control) machines, that can produce parts to the exact measurements specified by engineers and designers.
These components can be made from various materials, including metals like stainless steel, aluminum, and titanium, as well as plastics and composite materials. The primary goal is to ensure that each part is manufactured with extreme consistency and minimal deviation from the specified dimensions, ensuring that the entire product operates as intended.
The Importance of Precision Components
Precision components are critical in industries where performance, safety, and reliability are non-negotiable. The high accuracy required for these parts ensures that products work smoothly and maintain their integrity over time. Letβs take a closer look at the importance of precision components in various sectors.
1. Aerospace Industry
In aerospace, precision components are essential for ensuring the performance and safety of aircraft. Components such as turbine blades, landing gear, fuel systems, and avionics require tight tolerances to function correctly under high stress, extreme temperatures, and pressure. Even the smallest deviation in a partβs measurement could lead to catastrophic failure. CNC machining and other precision manufacturing techniques are commonly used in aerospace to create components that meet stringent quality standards and regulations.
2. Automotive Industry
The automotive industry relies heavily on precision components for everything from engine parts to brake systems, suspension components, and electrical systems. These parts must not only fit together perfectly but also withstand the wear and tear of everyday driving. Precision is critical in ensuring that vehicles perform at optimal levels and maintain safety features such as anti-lock braking systems (ABS), airbags, and powertrains. Advances in manufacturing technology have made it possible to produce lightweight yet durable automotive parts, contributing to fuel efficiency and overall performance.
3. Medical Devices
Precision components are pivotal in the medical industry, particularly in the creation of surgical instruments, implants, and diagnostic equipment. Components must be manufactured with extreme precision to meet strict regulatory standards and ensure patient safety. For example, medical implants like joint replacements and pacemakers must fit the human body with high precision to avoid complications. Additionally, diagnostic devices such as MRI machines or CT scanners rely on precision components for accurate imaging and readings. Any malfunction in these components can affect diagnosis and treatment, making precision manufacturing crucial.
4. Electronics Industry
The electronics industry has a constant demand for precision components that contribute to the performance of devices such as smartphones, computers, and consumer appliances. Printed circuit boards (PCBs), connectors, and microchips must be manufactured with high precision to ensure they work reliably in various electronic applications. As devices become more compact and feature-rich, the need for smaller, more precise components has grown. Precision manufacturing enables the production of components with intricate designs and small tolerances, supporting the miniaturization of electronic devices.
5. Industrial Equipment
In industrial applications, precision components are used in machinery, tooling, robotics, and heavy equipment. For instance, precision gears, shafts, and bearings are critical for machinery that operates at high speeds or under heavy loads. These components must be manufactured with precision to ensure smooth operation and avoid premature wear. Industrial equipment often operates in harsh environments, where even slight deviations in component measurements can cause equipment failures and downtime.
Methods of Producing Precision Components
Manufacturing precision components involves the use of advanced tools and technologies. The most commonly used methods include:
1. CNC Machining
CNC machining is one of the most popular methods for producing precision components. CNC machines are programmed with specific instructions, allowing them to perform tasks like milling, turning, and drilling with high accuracy. CNC technology allows for extremely tight tolerances and the production of complex geometries, making it ideal for industries that require precision.
2. Injection Molding
Injection molding is a common method used for manufacturing precision plastic components. In this process, molten plastic is injected into a mold and then cooled to form the final component. This method is particularly useful for producing high volumes of small, intricate parts with consistent quality and minimal defects.
3. Casting
Casting involves pouring molten material (such as metal or plastic) into a mold and allowing it to solidify into the desired shape. This method can be used for producing precision components in large quantities, particularly in industries like automotive and aerospace. Advanced casting techniques such as investment casting can achieve the necessary precision for critical parts.
4. Laser Cutting and Laser Engraving
Laser cutting is used for materials such as metal, plastic, and ceramics to achieve precision cuts with high accuracy. A laser beam is focused on the material, and a cutting action is performed based on the programmed design. Laser engraving can also be used to add markings, such as part numbers or logos, on precision components.
5. Electrical Discharge Machining (EDM)
Electrical Discharge Machining (EDM) is a process used to create complex shapes in hard metals by using electrical discharges (sparks). This method is highly accurate and is often used for producing molds, dies, and other intricate components that require high precision. EDM is especially useful for hard-to-machine materials such as tungsten or titanium.
6. 3D Printing
While not traditionally associated with high-precision manufacturing, 3D printing has advanced significantly and is increasingly used to produce precision components in certain applications. 3D printing can create highly complex geometries and parts with excellent dimensional accuracy, especially in industries like medical devices and aerospace.
Advantages of Using Precision Components
The use of precision components offers several benefits, particularly in industries where performance, reliability, and safety are critical. Here are some key advantages:
1. Enhanced Performance
Precision components are made to fit perfectly, which ensures that the product or system they are part of operates smoothly. Whether in aerospace or automotive systems, precise parts lead to better performance and higher reliability, ensuring that products function as intended.
2. Reduced Wear and Tear
Precision components are designed with tight tolerances, meaning they experience less friction and wear over time. This extends the lifespan of the entire system and reduces the need for maintenance or replacements, ultimately saving on operational costs.
3. Higher Safety Standards
In industries like aerospace and medical devices, the safety of the end product is paramount. The precision of components ensures that each part fits and functions correctly, reducing the likelihood of malfunctions or accidents. This is especially important in mission-critical applications where failure could have serious consequences.
4. Cost Efficiency in the Long Run
Although precision components may involve a higher initial cost due to the specialized manufacturing processes, they ultimately result in cost savings by improving performance, reducing downtime, and extending product lifespans. Additionally, precision manufacturing techniques minimize waste, reducing material costs.
5. Increased Reliability
Precision components ensure the reliability of the end product by minimizing variations in performance. Whether it’s a medical device or an industrial machine, parts that are precisely made are less likely to fail or perform inconsistently, which increases the overall reliability of the product.
Challenges in Precision Component Manufacturing
Despite the numerous benefits, there are also challenges in manufacturing precision components. These include:
- High Production Costs: Manufacturing precision components often requires advanced machinery and highly skilled operators, which can lead to higher upfront costs.
- Complexity: The intricate nature of many precision components can make them difficult and time-consuming to produce, particularly for custom or low-volume orders.
- Material Selection: Choosing the right material for a precision component is crucial, and it requires a thorough understanding of the part’s intended use and environment.
Conclusion
Precision components are a cornerstone of modern manufacturing, playing an integral role in industries such as aerospace, automotive, electronics, and medical devices. The ability to create parts with high accuracy and reliability ensures that products meet safety, performance, and durability standards. By employing advanced manufacturing technologies such as CNC machining, injection molding, and EDM, businesses can produce precision components that drive innovation and contribute to the success of their products. While challenges such as high production costs and material selection exist, the benefits of precision manufacturing far outweigh these obstacles, making it an invaluable process in todayβs high-tech world.
Leave a Reply